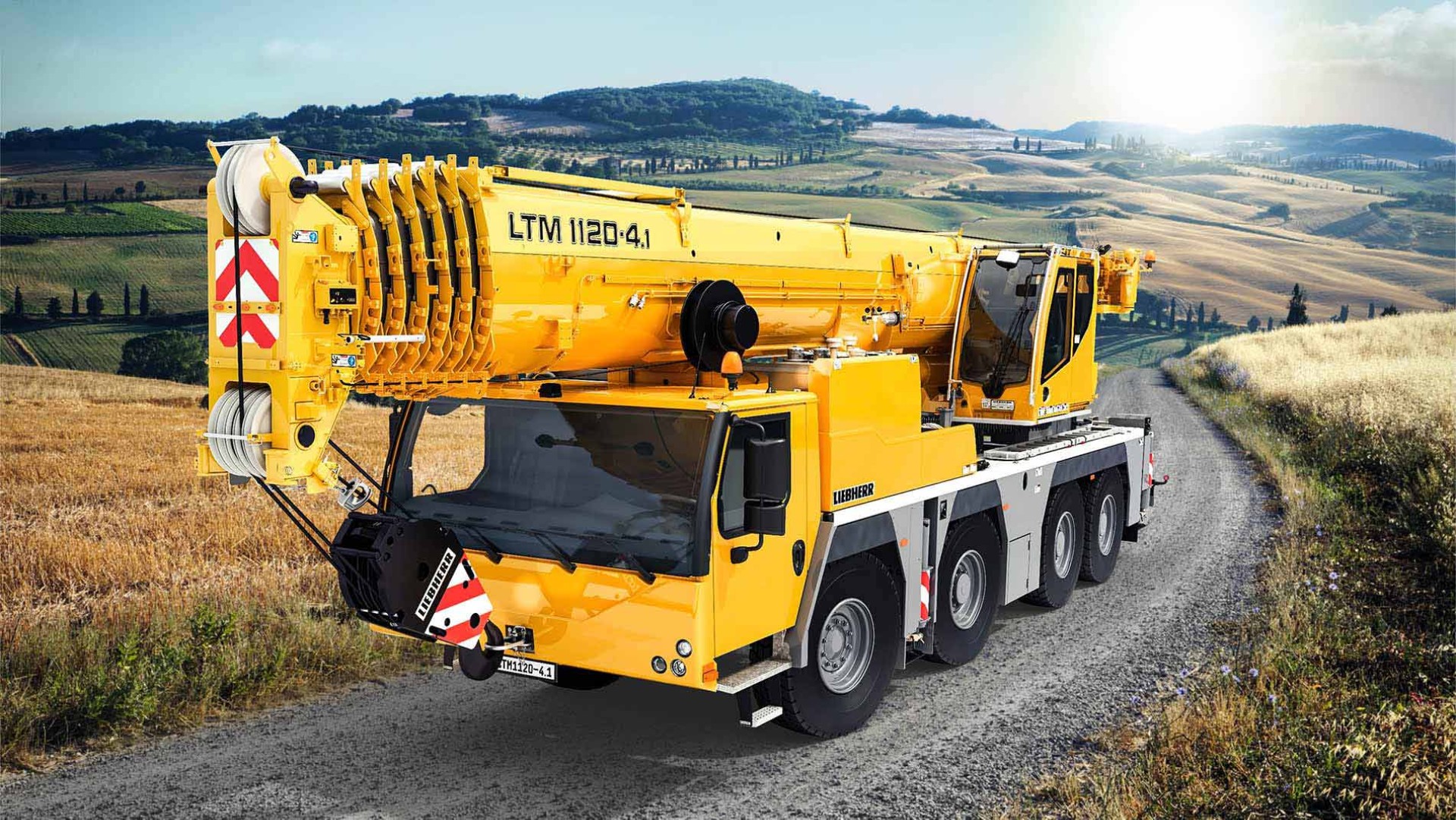
3 minutes | magazine 01/2020
Why has Liebherr changed the axle layout on its new four-axle cranes?
When Liebherr unveiled the new LTM 1090-4.2 in 2017, some industry insiders were a little irritated by the appearance of the crane from the side. It looked a little unusual somehow. But what exactly was it? The chassis looked as though it had been stretched a little. Normally the axles on four-axle all-terrain cranes are fairly close together and the outriggers are positioned right at the front and right at the rear. But the situation is different on the new Liebherr 90-tonne crane: the front outriggers are between axles 1 and 2. Jan Keppler, Head of the Product Management Department, explains the benefits and why Liebherr has repeated the trick in 2020 on the LTM 1120-4.1.
Yes, we actually have done it again. The front outrigger on the new LTM 1120-4.1 is also between the first and second axle. Admittedly, the new chassis are not quite as compact as the ones on the previous models. But the benefits of the new layout significantly outweigh this drawback.
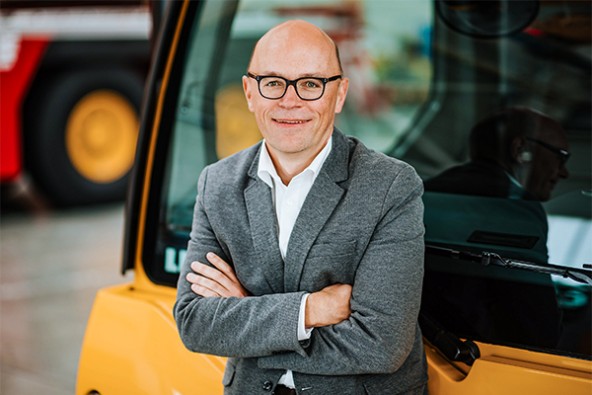
Jan Keppler, Head of Product Management
It creates more space in the ballast storage area on the undercarriage which makes the ballast radius adjustment range much larger. This is because we are using our innovative VarioBallast® system on the new LTM 1090-4.2 and LTM 1120-4.1 four-axle cranes. The cranes can be operated with two different ballast radii – mechanically slewing ballasting cylinders are used to adjust the ballast radius quickly and easily by 94 centimetres. On the LTM 1090-4.2, the small ballast radius is actually inside the outrigger width. And on the LTM 1120-4.1 it is actually 28 centimetres smaller than on its predecessor. This solution makes the crane much easier to use in constricted conditions.
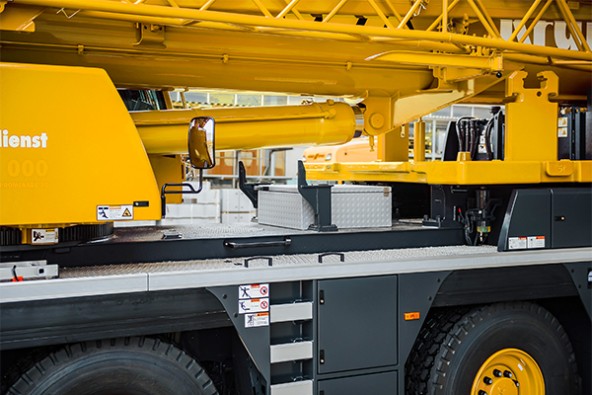
Everything stowed safely – New box near the ballast storage area.
If, however, there is plenty of space on the site, the large ballast radius can be used to good effect. The significantly longer lever arm of the counterweight means that the new models require much less ballast weight – around six tonnes on the LTM 1090-4.2 and over seven tonnes on the LTM 1120-4.1.
And there is another benefit. The greater space between axles 2 and 3 is used to store support timbers. This eliminates the need for a storage box at the rear of the vehicle. In addition, the new four-axle cranes have additional storage compartments for attachments and other equipment on the crane chassis.
What is more, even if the spacing between the axles has been increased slightly, our designers have managed to retain the manoeuvrability of the new cranes at a high level.
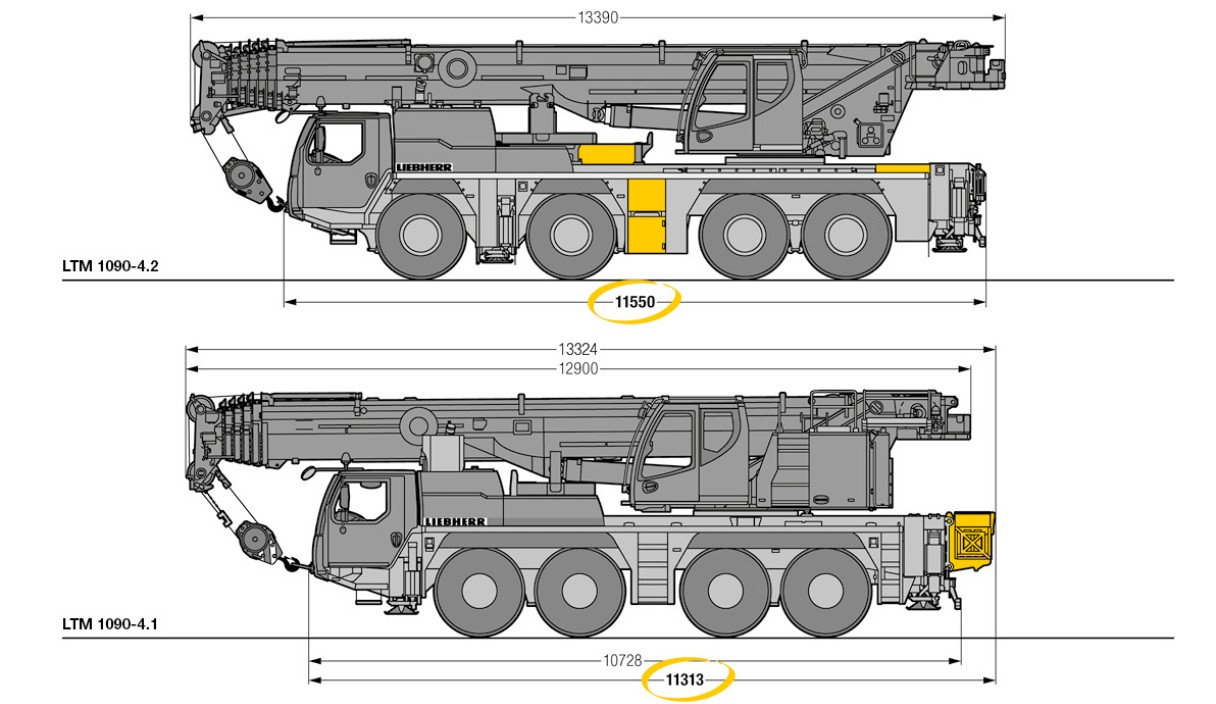
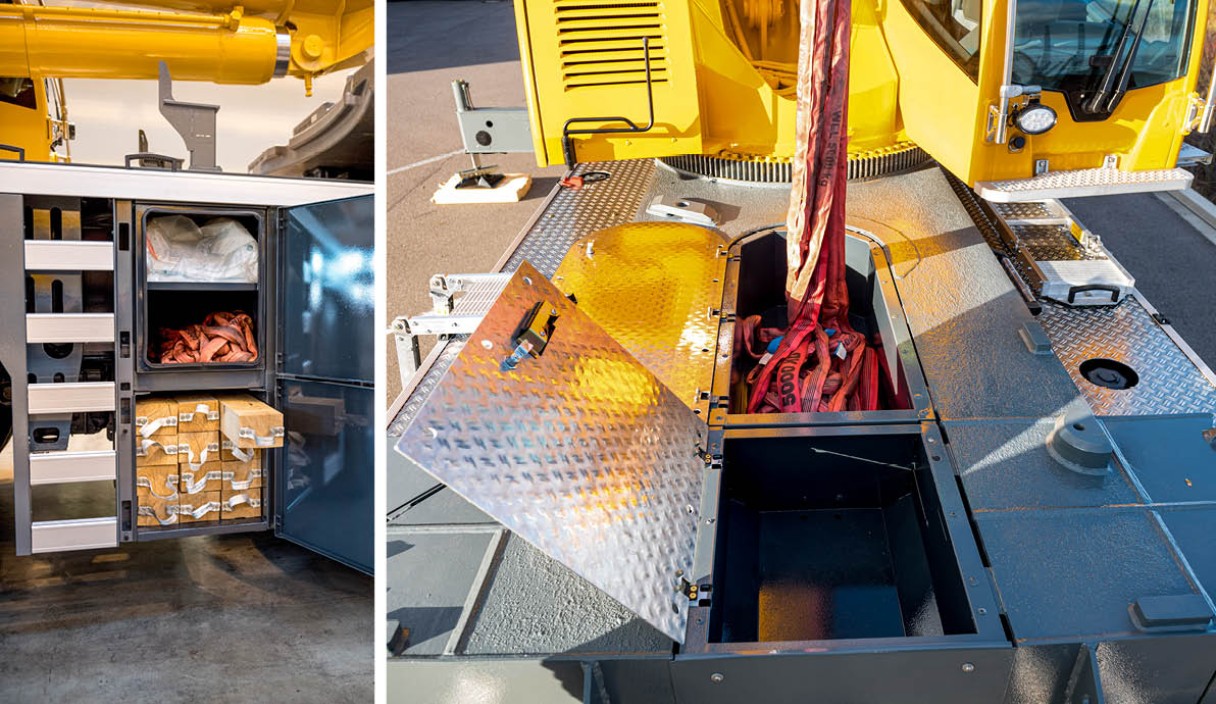
The storage boxes are integrated on the new four-axle cranes. There is therefore no longer any need for a storage box at the rear of the vehicle.
Finally, we have a little something for the connoisseurs among you – years ago we built a four-axle LTM crane on which the front outriggers were positioned between the first and second axle. You know, which crane model this was? Clue: It was only available in certain markets.
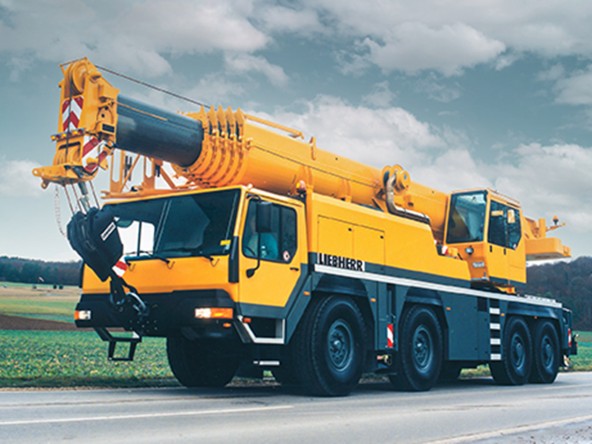
The LTM 1080/1 L was delivered between 2001 and 2005, mainly to customers in the USA.
And the Winner is...
We were delighted to receive so many answers from all over the world. And the vast majority of them were correct: Yes, it was the LTM 1080/1 L!
We asked which 4-axle LTM crane from many years ago had its front outriggers between the first and second axle (UpLoad 01/2020, page 27).
We built the LTM 1080/1 L around 20 years ago specifically for customers in the USA. The extended crane had a long axle spacing, which delivered benefits for licensing in many US states. But we must admit that its appearance took a bit of getting used to.
So many entered our competition, we decided to award five rather than three models of the LTM 1090-4.2 as prizes. Congratulations to the winners:
Nadine Sailer, Germany
Torsten Lange, Germany
Tavis Sayers, USA
Clint Debner, Australia
Martijn Jacobs, Netherlands
This article was published in the UpLoad magazine 01 | 2020. The announcement of the winners was in the 01 | 2021 issue.