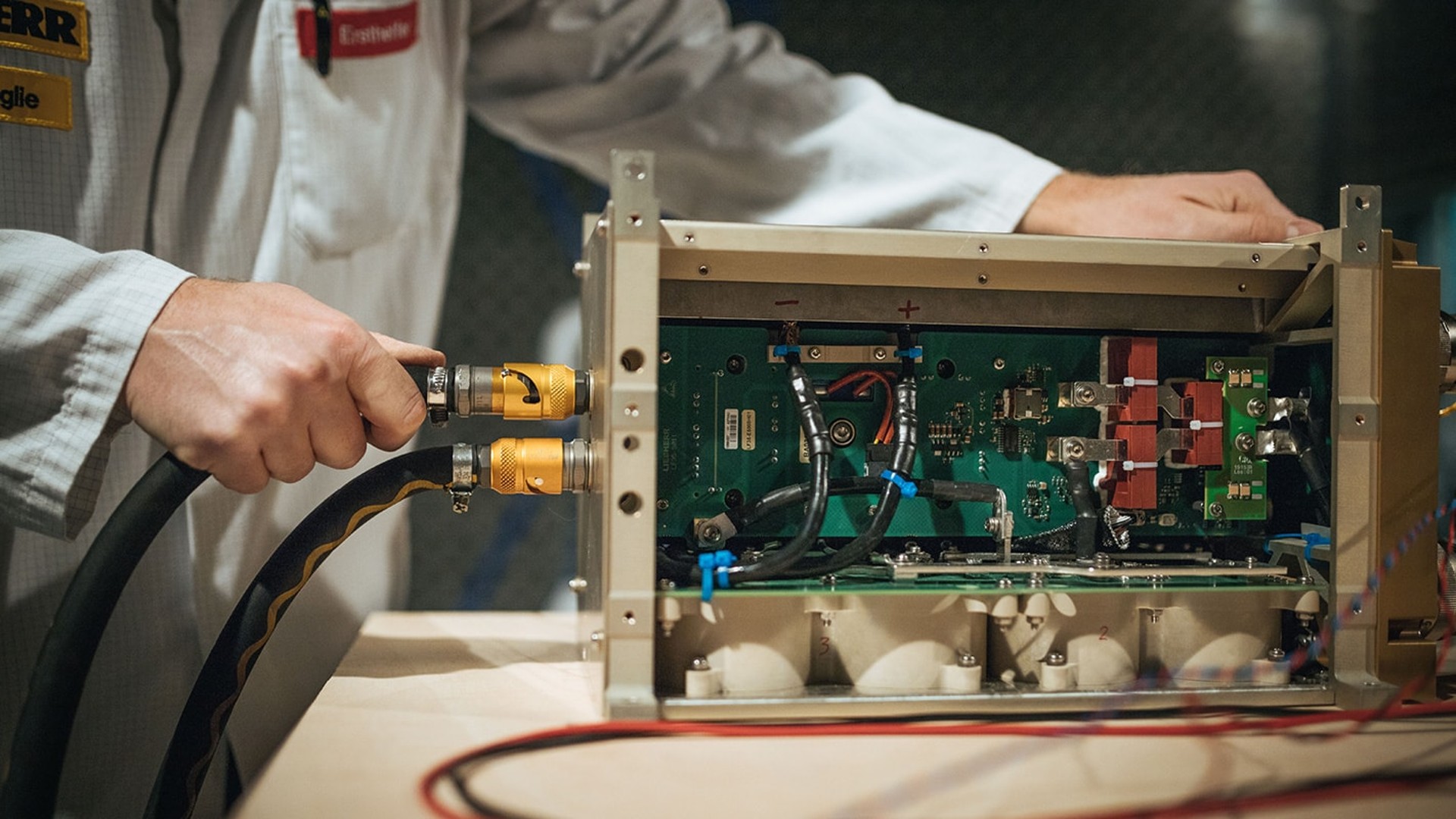
11 Minuten Lesezeit
Auf dem Weg zum elektrischen Fliegen
Bessere Energieversorgung, weniger Gewicht und insgesamt effizientere Flugzeuge – Liebherr forscht an drei Standorten im großen Stil an elektrischen Systemen, die schon bald das Fliegen revolutionieren können.
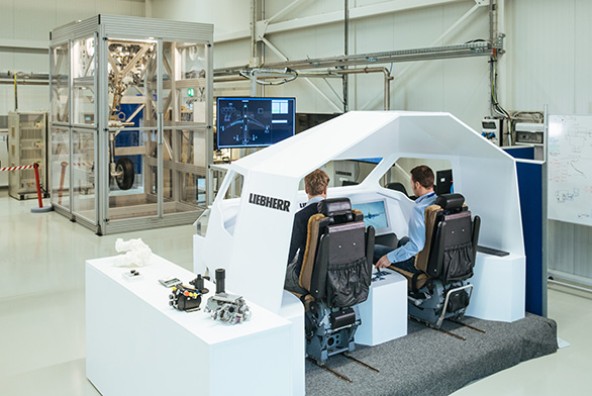
„Ready for take-off!“
Im Cockpit ist höchste Konzentration angesagt. Das Flugzeug beschleunigt, hebt ab, ein Knopfdruck, die Piloten fahren das Fahrwerk ein - und können dabei zusehen. Denn das Bugfahrwerk befindet sich direkt vor ihrem Cockpit-Fenster. Die Piloten sind Ingenieure und steuern einen Flugzeugsimulator im E-WING-Forschungszentrum von Liebherr-Aerospace in Lindenberg (Deutschland).
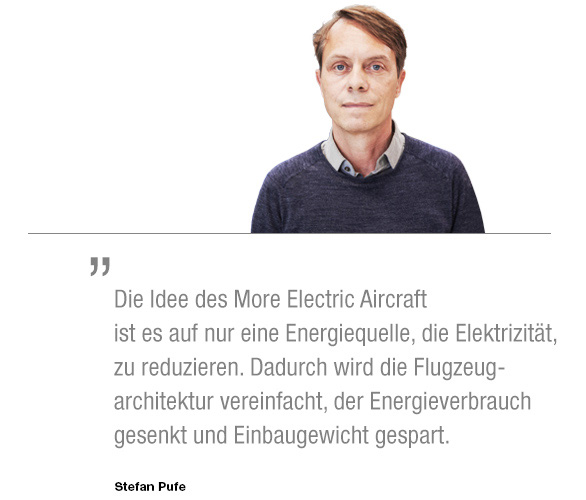
Weniger ist mehr
Stefan Pufe leitet in Lindenberg als Director Research & Technology ein Team von Ingenieuren und Entwicklern, das gemeinsam mit zwei weiteren Projektteams in Lindau (Deutschland) und in Toulouse (Frankreich) einer neuen Dimension des Fliegens auf der Spur ist: dem More Electric Aircraft. Das Ziel des „MEA“: das Fliegen in Zukunft leichter, effizienter und umweltverträglicher zu gestalten. Mit deutlich weniger Leitungen, Antriebswellen und Verkabelungen.
Im besonderen Blickfeld sind dabei die sogenannten Aktuatoren. Darunter versteht man Geräte, die zentral generierte hydraulische Energie in mechanische Bewegung umwandeln. Die Liebherr-Entwickler tüfteln in Lindenberg daran, wie solche hydraulische Systeme künftig durch elektromechanische oder elektrohydrostatische ersetzt werden, die zum Beispiel von einem zentralen elektrohydraulischen Power Pack auf Starkstrombasis (540 V Gleichstrom) mit Energie versorgt werden.
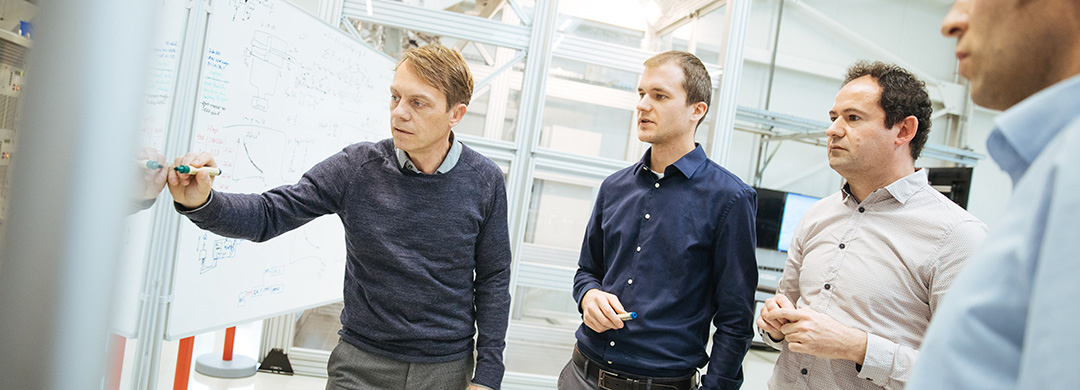
Research in Progress
„Wir testen und vermessen dazu im E-WING an fünf Prüfständen unterschiedliche Möglichkeiten der Aktuatoren-Ansteuerung: klassisch hydraulisch, elektrohydraulisch und elektromechanisch“, erklärt Stefan Pufe. Die einzelnen Konzepte sind als Demonstratoren miteinander verschaltet und können in ihrem tatsächlichen Betrieb simuliert werden. Deutlich zu sehen ist dies beim Modell einer Flugzeugtragfläche. Hier arbeiten diese drei Systeme parallel nebeneinander und bewegen, vom Simulator-Cockpit aus angesteuert, Spoiler-Klappen, wie sie zum Bremsvorgang nach der Landung aufgestellt werden.
Indem Sie auf „AKZEPTIEREN“ klicken, willigen Sie für dieses Video gemäß Art. 6 Abs. 1 lit. a DSGVO in die Datenübermittlung an Google ein. Wenn Sie künftig nicht mehr zu jedem YouTube-Video einzeln einwilligen und diese ohne diesen Blocker laden können möchten, können Sie zusätzlich „YouTube-Videos immer akzeptieren“ auswählen und damit auch für alle weiteren YouTube-Videos, welche Sie zukünftig auf unserer Website noch aufrufen werden, in die jeweils damit verbundenen Datenübermittlungen an Google einwilligen.
Erteilte Einwilligungen können Sie jederzeit mit Wirkung für die Zukunft widerrufen und damit die weitere Übermittlung Ihrer Daten verhindern, indem Sie den entsprechenden Dienst unter „Sonstige Dienste (optional)“ in den Einstellungen abwählen (später auch aufrufbar über die „Datenschutzeinstellungen“ in der Fußzeile unserer Website ).
. Weitere Informationen erhalten Sie in unserer Datenschutzerklärung sowie in der Google-Datenschutzerklärung.Datenschutzerklärung von Google.*Google Ireland Limited, Gordon House, Barrow Street, Dublin 4, Irland; Mutterunternehmen: Google LLC, 1600 Amphitheatre Parkway, Mountain View, CA 94043, USA** Hinweis: Die mit der Datenübermittlung an Google verbundene Datenübermittlung in die USA erfolgt auf Grundlage des Angemessenheitsbeschlusses der Europäischen Kommission vom 10. Juli 2023 (EU-U.S. Data Privacy Framework).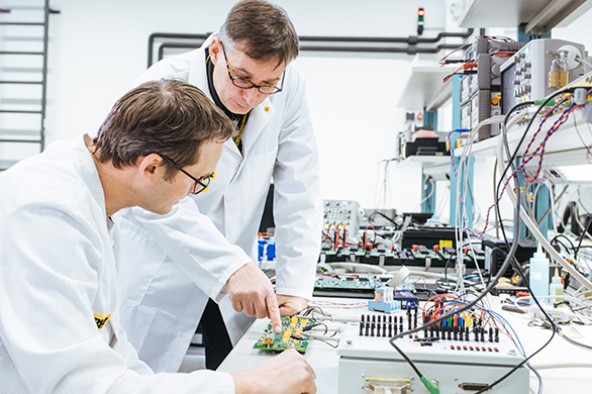
Goldenes "Power Pack"
Dass sich Luftfahrtpioniere am Bodensee wohlfühlen, zeigt die Geschichte. Hier hoben schon im frühen 20. Jahrhundert die ersten Zeppeline sowie erstmals Flugzeuge und Flugboote aus Ganzmetall ab. Knapp ein Jahrhundert später arbeitet ein 80-köpfiges Team der Liebherr-Elektronik GmbH in Lindau (Deutschland) an neuen Luftfahrtinnovationen. Die Elektroingenieure, Softwareentwickler, Maschineningenieure und Testingenieure haben eine wesentliche Komponente des More Electric Aircraft der Zukunft im Blick: die Leistungselektronik.
Dazu gehört ein goldenes „Power Pack“. „Der Wechselrichter ist auf das elektrisch optimierte Fliegen ausgerichtet“, erläutert Dr.-Ing. Alfred Engler, Leiter Entwicklung Technologien bei der Liebherr-Elektronik GmbH. Der Wechselrichter sorgt dafür, dass die hohe Gleichspannung (540 V) zu den Aktuatoren in die Tragflächen und Steuereinheiten gelangt und darüber hinaus ganz neue Wege der Klimatisierung des Flugzeugs eröffnet. Bislang kommen in Flugzeugen standardmäßig Geräte mit 115 Volt 400 Hertz Wechselstrom zum Einsatz.
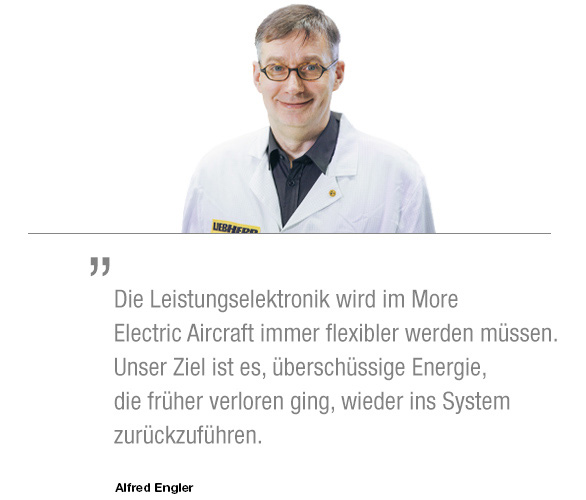
Auf die harte Tour
Die Forscher testen nun in ihren Laboren, ob die neuen starkstrombasierten Geräte auch unter allen erdenklichen Flugbedingungen wie erwartet funktionieren. Dabei bleibt dem Wechselrichter nichts erspart: Er wird gerüttelt, geschüttelt, bestrahlt und tiefgefroren – und dabei sorgfältig überwacht. Sicher ist sicher.
Indem Sie auf „AKZEPTIEREN“ klicken, willigen Sie für dieses Video gemäß Art. 6 Abs. 1 lit. a DSGVO in die Datenübermittlung an Google ein. Wenn Sie künftig nicht mehr zu jedem YouTube-Video einzeln einwilligen und diese ohne diesen Blocker laden können möchten, können Sie zusätzlich „YouTube-Videos immer akzeptieren“ auswählen und damit auch für alle weiteren YouTube-Videos, welche Sie zukünftig auf unserer Website noch aufrufen werden, in die jeweils damit verbundenen Datenübermittlungen an Google einwilligen.
Erteilte Einwilligungen können Sie jederzeit mit Wirkung für die Zukunft widerrufen und damit die weitere Übermittlung Ihrer Daten verhindern, indem Sie den entsprechenden Dienst unter „Sonstige Dienste (optional)“ in den Einstellungen abwählen (später auch aufrufbar über die „Datenschutzeinstellungen“ in der Fußzeile unserer Website ).
. Weitere Informationen erhalten Sie in unserer Datenschutzerklärung sowie in der Google-Datenschutzerklärung.Datenschutzerklärung von Google.*Google Ireland Limited, Gordon House, Barrow Street, Dublin 4, Irland; Mutterunternehmen: Google LLC, 1600 Amphitheatre Parkway, Mountain View, CA 94043, USA** Hinweis: Die mit der Datenübermittlung an Google verbundene Datenübermittlung in die USA erfolgt auf Grundlage des Angemessenheitsbeschlusses der Europäischen Kommission vom 10. Juli 2023 (EU-U.S. Data Privacy Framework).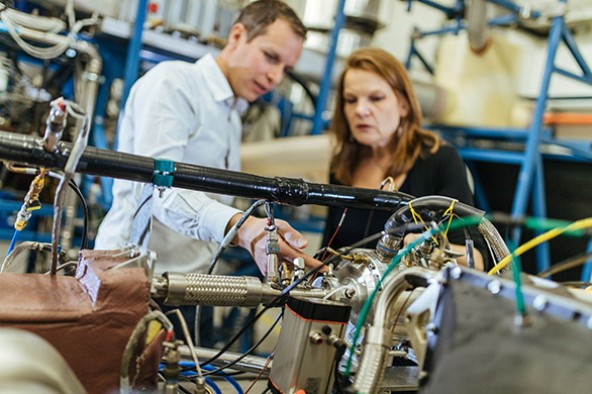
Einzigartige Testumgebung
In Toulouse leitet Nathalie Duquesne, Director Research & Technology bei der Liebherr-Aerospace Toulouse SAS, das Projekt GETI (Dynamisches Management von elektrischer und thermischer Energie). Im Blickfeld des Liebherr-Teams in Toulouse stehen die Optimierung der elektrischen Klimaanlage und des elektrischen Vereisungsschutzsystems für Tragflächenvorderkanten. Ziel ist es auch hier, das Gewicht und den Treibstoffverbrauch des Flugzeugs zu verringern und eine signifikante CO2- und Stickoxid-Emissionsreduktion zu ermöglichen.
Dazu hat Nathalie Duquesne mit ihrer Mannschaft mit GETI eine einzigartige Testplattform entwickelt, die auf der globalen Vision des elektrifizierten Flugzeugs und seiner nicht zum Vortrieb benötigten Energie basiert. „In GETI können wir die wichtigsten elektrischen Bedarfsträger für das elektrische Flugzeug der Zukunft identifizieren", erklärt Duquesne. Der Fokus der Plattform liegt darüber hinaus auf Modellen, die entwickelt wurden, um das elektrische und thermische Verhalten der verschiedenen Systeme zu reproduzieren. „Alle unsere Aktivitäten und Forschungen für das elektrische Flugzeug erfolgen in Zusammenarbeit mit den verschiedenen Standorten. So testen wir beispielsweise bereits Produkte aus Lindau. Das heißt auch, dass andere Energieverbraucher aus Lindenberg problemlos in diesen Prüfstand eingebracht werden können. Die verschiedenen Puzzleteile aus Tragflächensystemen, Leistungselektronik und Klima- und Thermomanagement fügen sich perfekt zu einem Gesamtbild zusammen. Das alles trägt dazu bei, den Energiebedarf und das Gewicht der Systeme zu optimieren“, so Nathalie Duquesne.
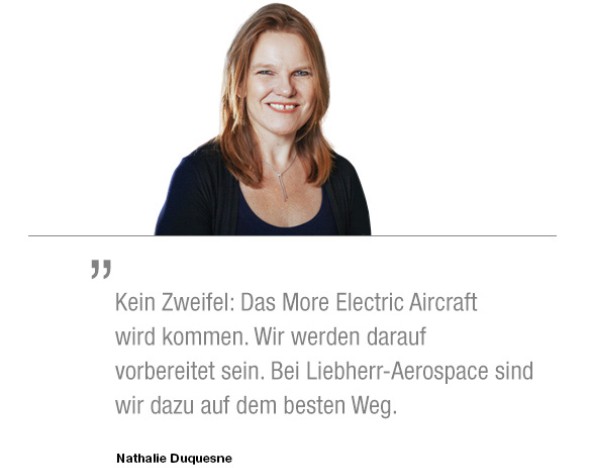
Die Zeichen weisen in die Zukunft
Parallel dazu haben sich Flugtestkampagnen, die sich auf elektrische Klimatisierungssysteme konzentrierten, als wettbewerbsfähige Lösung erwiesen", sagt Nathalie Duquesne. Sowohl intensive interne Tests als auch Flugtests haben die Robustheit und Stabilität der Systeme bestätigt. „Wir haben eine vielversprechende elektrische Klimatisierungs- und Eisschutzarchitektur für das More Electric Aircraft entwickelt. Das Ergebnis ist rundum zufriedenstellend. Nun ist es an der Zeit, die einzelnen Komponenten und Systeme noch weiter zu optimieren. Die Zukunft der Luftfahrt hat begonnen", sagt Duquesne. „Wir von Liebherr gestalten sie mit.“
Indem Sie auf „AKZEPTIEREN“ klicken, willigen Sie für dieses Video gemäß Art. 6 Abs. 1 lit. a DSGVO in die Datenübermittlung an Google ein. Wenn Sie künftig nicht mehr zu jedem YouTube-Video einzeln einwilligen und diese ohne diesen Blocker laden können möchten, können Sie zusätzlich „YouTube-Videos immer akzeptieren“ auswählen und damit auch für alle weiteren YouTube-Videos, welche Sie zukünftig auf unserer Website noch aufrufen werden, in die jeweils damit verbundenen Datenübermittlungen an Google einwilligen.
Erteilte Einwilligungen können Sie jederzeit mit Wirkung für die Zukunft widerrufen und damit die weitere Übermittlung Ihrer Daten verhindern, indem Sie den entsprechenden Dienst unter „Sonstige Dienste (optional)“ in den Einstellungen abwählen (später auch aufrufbar über die „Datenschutzeinstellungen“ in der Fußzeile unserer Website ).
. Weitere Informationen erhalten Sie in unserer Datenschutzerklärung sowie in der Google-Datenschutzerklärung.Datenschutzerklärung von Google.*Google Ireland Limited, Gordon House, Barrow Street, Dublin 4, Irland; Mutterunternehmen: Google LLC, 1600 Amphitheatre Parkway, Mountain View, CA 94043, USA** Hinweis: Die mit der Datenübermittlung an Google verbundene Datenübermittlung in die USA erfolgt auf Grundlage des Angemessenheitsbeschlusses der Europäischen Kommission vom 10. Juli 2023 (EU-U.S. Data Privacy Framework).Die Energiequellen an Bord
Flugzeuge benötigen einen hohen Kraft- und Energieaufwand, um ihre beweglichen Teile zu betätigen und um den Luft- und Kabinendruck kontrollieren zu können. Dafür werden bislang in der Regel hydraulische oder pneumatische Systeme genutzt. Im More Electric Aircraft werden diese zunehmend durch elektrische Alternativen unterstützt oder sogar ersetzt. Da lohnt es sich einmal genauer hinzuschauen, welche Energiequellen bisher im Flugbetrieb eingesetzt werden.
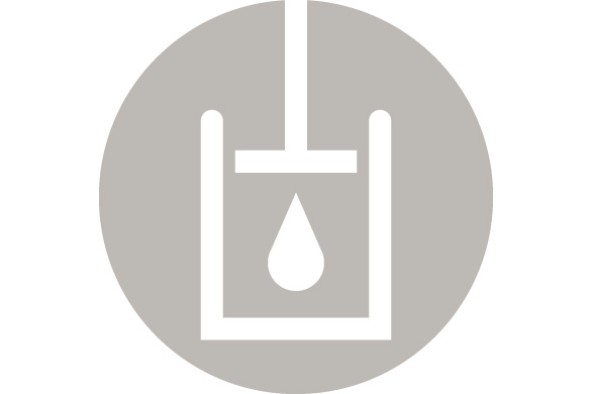
Hydraulik
Der Begriff stammt aus dem Griechischen und verbindet „Hydro“ (Wasser) mit „Aulos“ (Rohr). Die Hydraulikflüssigkeit, meist ein spezielles Mineralöl, überträgt Leistung mittels Druck und Flüssigkeitsstrom und kann damit enorme Kräfte erzeugen. Etwa wenn Hydraulikleitungen die Steuerflächen eines Flugzeugs in der Größe von Scheunentoren bewegen – sogar bei Wind mit Orkanstärke. Die Bewegung am Steuerknüppel löst dabei über Sensoren den entsprechenden Befehl aus. Die Nachteile der Hydraulik: hydraulische Anlagen mit ihren Flüssigkeiten sind sehr schwer, das Verlegen der Leitungen ist sehr aufwendig und die Anlage muss stets betriebsbereit sein und steht deshalb immer unter Druck, was einen höheren Kraftstoffverbrauch mit sich bringt.
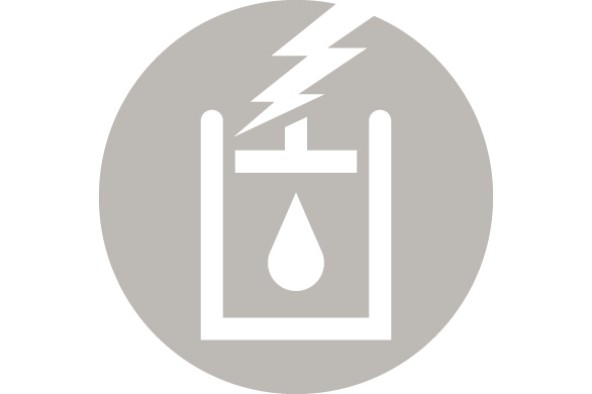
Elektrohydraulik
Bei diesem Verfahren wird die Hydraulik von einem elektrischen Impuls gesteuert und der hydraulische Druck wird erst lokal dort produziert, wo er gebraucht wird. Hier sind erhebliche Einsparungen in der Verrohrung und im Flüssigkeitseinsatz möglich. Bei einem elektrohydrostatischen Aktuator werden beispielsweise die weiterhin hydraulischen Aktuatoren durch ein lokales Hydrauliksystem versorgt, das durch eine eigene Elektromotor-Pumpe-Einheit gespeist wird.
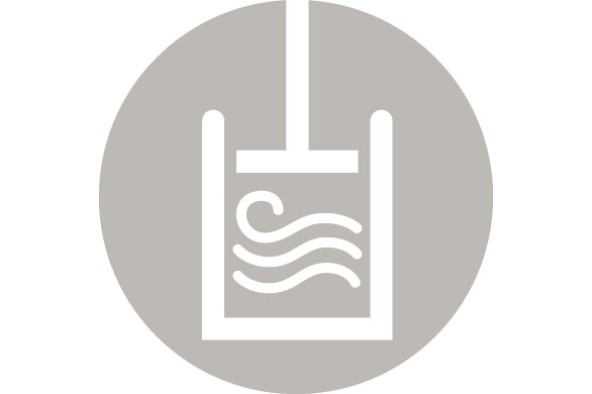
Pneumatik
Der Begriff Pneumatik kommt ebenfalls aus dem Griechischen (pneuma = Wind) und bezeichnet den Einsatz von Druckluft in geschlossenen Systemen. Im Flugzeug wird die benötigte Luft in den Kompressorstufen des Triebwerks entnommen. Diese gelangt über entsprechende Leitungen und Rohre in die Klimaanlage, wo die Temperatur über ein komplexes System von Kompressoren und Turbinen geregelt wird. Dabei wird der Druck entsprechend dem Flightlevel angepasst - die so genannte Kabinenhöhe. Die Spanne des Luftdrucks bei Verkehrsflugzeugen reicht von rund 1000 hPa am Boden bis zu etwa 200 hPa in Reiseflughöhen von 33.000 Fuß und höher. Passagiere empfinden während des Flugs einen Luftdruck von nicht weniger als 700 hPa als angenehm. Dies muss über die gesamte Flugdauer sichergestellt werden.
Finanzierung dieses Forschungsprojektes
Dieses Projekt wird durch die EU-Technologie-Initiative Clean Sky 2 im Rahmen des Forschungs- und Innovationsprogramms Horizon 2020 finanziert (Finanzhilfevereinbarung Nr. 807081), wobei die Ergebnisse dieser Veröffentlichung nur die Ansicht des Autors wiedergeben. Das Gemeinschaftsunternehmen Clean Sky ist nicht verantwortlich für die Verwendung der enthaltenen Informationen.
Dieses Projekt wurde vom Bundesministerium für Wirtschaft und Energie auf der Grundlage einer Entscheidung des Deutschen Bundestages unterstützt.

Aufgrund besserer Lesbarkeit verwenden wir bei Berufsbezeichnungen ausschließlich die männliche Form. Diese steht hier repräsentativ für eine geschlechtsneutrale Bezeichnung. Gemeint sind grundsätzlich alle Geschlechtsidentitäten (m/w/d).