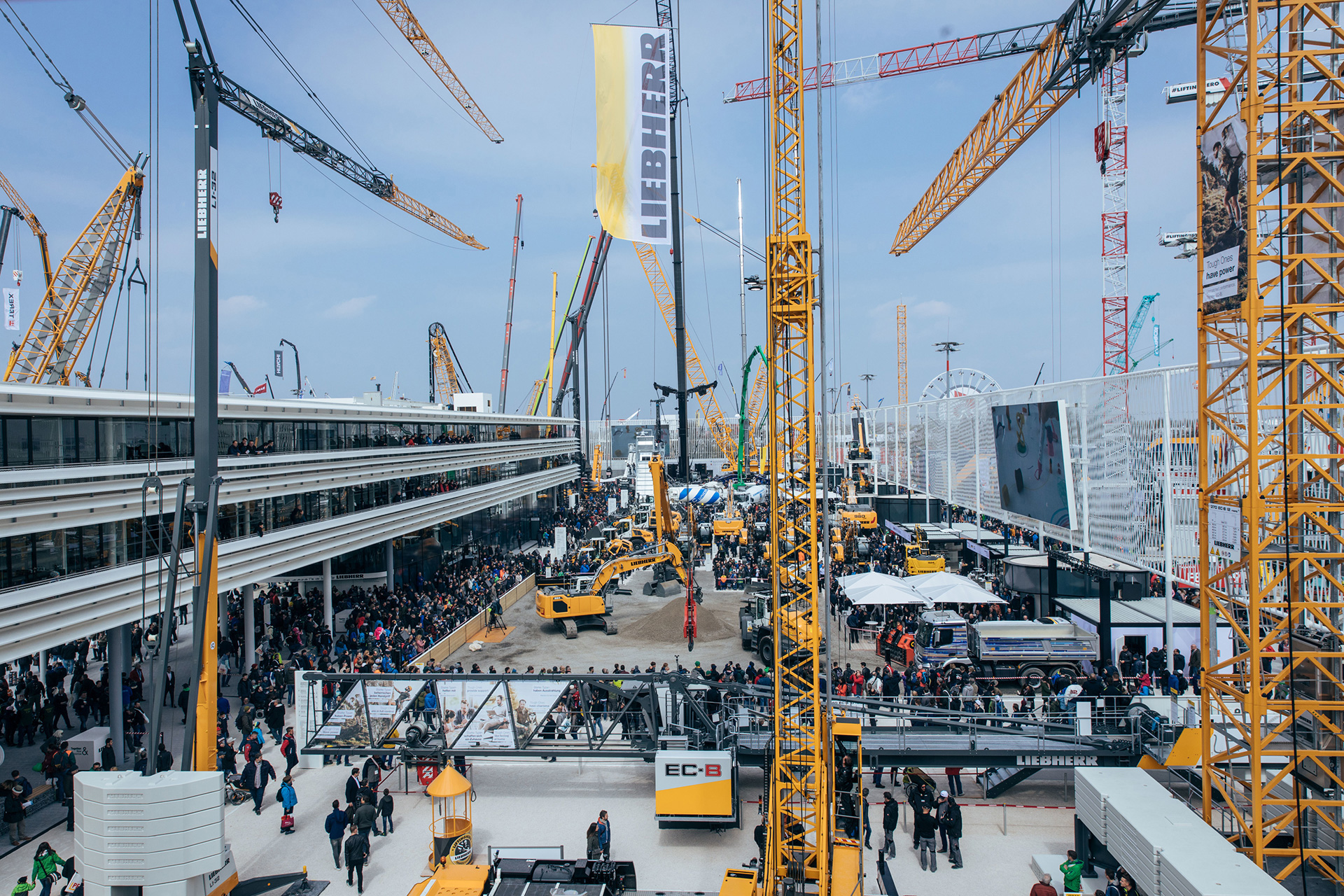
Klicken Sie auf VIDEO FREIGEBEN und folgen Sie den Datenschutzhinweisen.
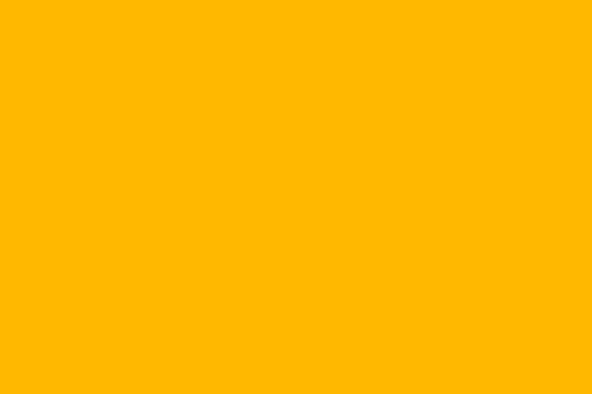
Dimensionen
Die Bauma ist die größte Fachmesse der Welt und Liebherr einer der größten Aussteller. Auf einer Fläche von 14.500 m² stellt Liebherr alle drei Jahre Innovationen, Lösungen, Giganten und Zukunftstrends vor. Ein internationales Publikum aus aller Welt taucht für sieben Tage ab in die faszinierende Welt der Baumaschinen und Mining-Geräte.
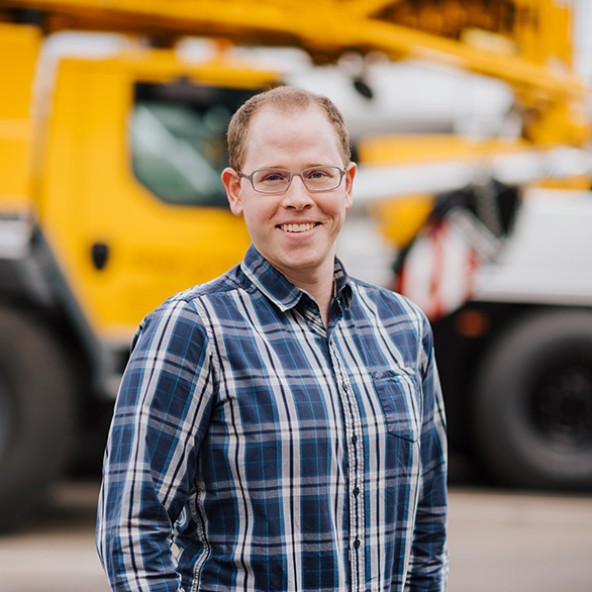
Von der Bauma zum Traumjob
Eigentlich wollte Ricardo Dieing bei der Bauma nur ein bisschen staunen. Kurz darauf hatte der 29-Jährige seinen Traumjob bei Liebherr in Ehingen gefunden.
„Ein Gang über die Bauma ist für mich Pflicht“, sagt Ricardo Dieing. Schon dreimal war der 29-jährige Bauingenieur auf der weltgrößten Messe für Baumaschinen. Und jedes Mal führte ihn sein Gang auch zum Liebherr-Stand. „Die großen Baumaschinen und vor allem die Krane haben mich schon immer in ihren Bann gezogen“, sagt er.
Eher zufällig sei er diesmal auch am Karrierestand stehen geblieben und dort mit dem HR-Manager Stefan Füller ins Plaudern gekommen. „Ich hatte nach dem Studium einen guten Einstieg bei einem großen Gerüsthersteller und deswegen auch nach nichts Bestimmtem gesucht. Zwei Wochen später schickte mir Stefan dann eine Stellenausschreibung, die perfekt passte“, erinnert er sich.
Im Oktober nahm Dieing dann seine Arbeit in Ehingen auf. „Sympathische Kollegen, reizvolle Aufgaben und eine tolle Arbeitsumgebung: Besser hätte der Einstieg nicht laufen können“, stellt er fest.
Stahlbau und die Finite-Elemente-Berechnungen hätten ihn schon im Studium besonders interessiert: „Sich in der Gitterstatik eines Krans an die Grenzen des Materials heranzurechnen, ist super spannend“, sagt Dieing.
War das nun Zufall oder Schicksal? „Eigentlich egal“, sagt der junge Bauingenieur. „Ich habe schon jetzt große Schritte nach vorn gemacht. Im Kranbau wird mir ganz sicher niemals langweilig.“
Die Bauma gehört zu Liebherr und Liebherr gehört zur Bauma
Seit mehr als 60 Jahren ist Liebherr auf der Leitmesse vertreten. Über die Jahre hat sich viel getan.
Das war die Bauma 2019
Test bestanden: die emissionsfreie Baustelle der Zukunft
In Vorarlberg wurde erfolgreich die Baustelle der Zukunft getestet. Die auf der Bauma von Liebherr vorgestellten E-Maschinen wiesen dabei den Weg zu „Local Zero Emission“. Eine Zwischenbilanz mit Martin Hofer von der i+R-Gruppe, die gemeinsam mit Liebherr und ihrem Start-up Suncar HK die elektrische Umrüstung des Großdrehbohrgeräts LB16 unplugged vorgenommen hatte. Eine Weltpremiere mit Aussichten.
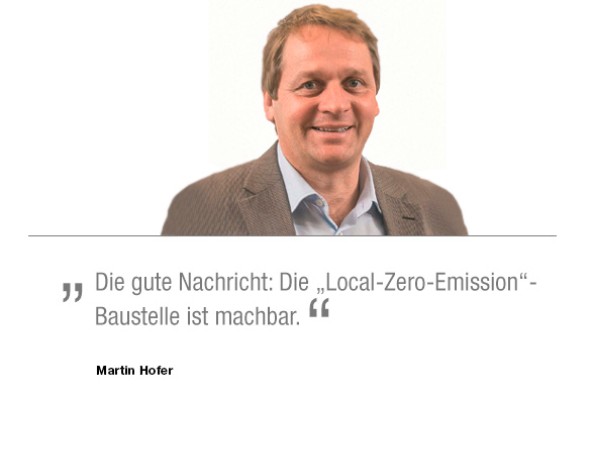
Herr Hofer, auf einer Baustelle, gerade im Spezialtiefbau, geht es richtig zur Sache. Wie steht es da um die Nachhaltigkeit und Energieeffizienz?
Nachhaltigkeit, Energie- und Ressourceneffizienz sind auf der Baustelle genauso ein Thema wie auch sonst in unserer Arbeits- und Lebenswelt. Wir haben ja nur diesen einen Planeten. Die gute Nachricht: Die „Local-Zero-Emission“-Baustelle ist machbar. Gerade in dichtbesiedelten Gebieten, wo Lärm- und Abgasemissionen besonders kritisch gesehen werden, weist sie in die richtige Richtung.
Auf welche Erfahrungen können Sie sich dabei stützen?
Wir haben mittlerweile über 45 Kompaktbagger auf elektrischen und kabellosen Antrieb umgerüstet. Ausgangspunkt war der weltweit erste kabellos batteriebetriebene Elektrobagger, den wir gemeinsam mit Studierenden der Maschinenbau- und Elektroingenieurwissenschaften der ETH-Zürich realisiert hatten.
Zusammen mit Liebherr haben Sie vor kurzem im österreichischen Vorarlberg an der Anschlussstelle der A 14 Bludenz-Bürs die erste Local-Zero-Emission-Baustelle im Spezialtiefbau abgeschlossen. Was waren dort die Herausforderungen?
Bludenz-Bürs war für uns ein ideales Testfeld. Die Anschlussstelle ist stark befahren, es kommt dort immer wieder zu Staus und Verkehrsbehinderungen. Zudem hatten wir es mit einem sehr beengten Baufeld zu tun, in dem sich die Bagger, das Bohrgerät und die Mischfahrzeuge auf kleinstem Raum bewegen mussten. Für die Gründungsarbeiten kam dort mit dem LB 16 unplugged von Liebherr das erste akkubetriebene Großdrehbohrgerät der Welt zum Einsatz. In elf Monaten hatten wir das Gerät umgerüstet mit dem Ziel, dass sich keinerlei Einschränkungen in puncto Leistung und Anwendung gegenüber der konventionellen Ausführung ergaben. Hinzu kamen weitere elektrische Bagger und ein Liebherr-Betonmischer vom Typ ETM 905 mit elektrischem Trommelantrieb für die Anlieferung eines Großteils des Betons. Das Ergebnis: so gut wie keine lokalen Abgase und deutlich weniger Lärm.
Ist eine solche vollelektrische Baustelle überall denkbar?
Auf jeden Fall. Grundsätzlich sind wir in der Lage, jede Maschine mit einem Elektroantrieb auszustatten. Wo sonst der Dieselmotor und der Tank untergebracht sind, bauen wir den Elektromotor und eine entsprechend leistungsfähige Batterie oder Supercaps ein. Am einfachsten ist die Umrüstung natürlich, wenn wir vom Hersteller, wie beim LB 16 unplugged, ein entsprechend konfiguriertes Basismodell bekommen, wo wir den fossilen Verbrenner-Antriebsstrang nicht erst ausbauen müssen.
Wo liegen die besonderen Herausforderungen bei der Elektrifizierung?
Die Elektromotoren sind sehr weit entwickelt. Auch bei den Lithium-Ionen-Batterien hat es in den letzten Jahren große Fortschritte gegeben. Unser besonderer Entwicklungsfokus liegt auf dem Batteriemanagement. Die Temperierung der Batterie ist entscheidend für ihre Leistungsfähigkeit. Das ist wie beim Handy. Lässt man es in der prallen Sonne im Auto liegen, meldet sich die Batterie irgendwann ab. Oder im Winter, wenn’s beim Skifahren zu kalt wird und das Handy ausgerechnet kurz vor dem ultimativen Gipfelfoto den Geist aufgibt.
Vor allem unter Einbeziehung der Ausgaben für Energie und Wartung haben die E-Maschinen auf lange Sicht die Nase gegenüber konventionellen Verbrennern vorn.
Wann amortisiert sich ein solcher E-Antrieb?
Eine kabellos elektrisch betriebene Baumaschine bedeutet erst einmal höhere Anschaffungskosten. In der Lifecycle-Perspektive mit einer Betriebsleistung von über 15.000 Stunden amortisieren sich die Kosten jedoch. Vor allem unter Einbeziehung der Ausgaben für Energie und Wartung haben die E-Maschinen auf lange Sicht die Nase gegenüber konventionellen Verbrennern vorn. Hier sind große Einsparpotenziale zu realisieren.
Die CO2-Bilanz von Baumaschinen lässt sich ja nicht allein am Auspuff messen. Wie fällt der gesamte CO2-Fußabdruck aus?
Wie beim Elektroauto müssen wir auch bei der Baumaschine auf das Gesamtbild schauen und neben dem Energieverbrauch auch die Produktion und die Lieferketten in die CO2-Rechnung miteinbeziehen. Der Turnaround tritt nach etwa 60 Prozent der Laufleistung ein, erst dann wird die E-Baumaschine CO2-belastungsneutral. Und das aber auch nur, wenn der Strom aus sauberen, regenerativen Quellen kommt. Wenn das Kohlekraftwerk die Energie für den Elektronantrieb liefert, ist an der Klimafront nichts gewonnen.
Wenn Local Zero Emission auf der Baustelle technologisch bereits möglich ist, wie weit ist es dann noch zur großflächigen Umsetzung?
Das wird nicht von heute auf morgen gehen. Es fehlt derzeit vor allem an den verfügbaren Kapazitäten in den sauberen, regenerativen Energien. Auch die Netze sind noch nicht auf die Belastungen ausgelegt, die mit einem konsequenten Wandel zur E-Mobilität einhergehen. Wenn am Abend alle gleichzeitig ihre E-Mobile und -Baumaschinen laden wollten, gingen im Lande wohl die Lichter aus. Da bleibt also noch viel zu tun.
Und was vor allem?
Die Technologie ist vorhanden. Entscheidende Veränderungen wird es aber wohl erst dann geben, wenn der Gesetzgeber mit entsprechenden Verordnungen und Gesetzen die Leitplanken neu setzt. Wie zum Beispiel in den Niederlanden oder in Norwegen, wo auf Flüssen und innerstädtischen Baustellen fossile Treibstoffe jetzt sukzessive ausgesperrt werden. Die Corona-Krise zeigt übrigens, welche Veränderungen auch in Richtung Nachhaltigkeit schlagartig möglich sind, wenn die Politik sich einig ist.
Unser Projekt mit Liebherr hat gezeigt, dass die Technologie und das Know-how da sind, um die Local-Zero-Emission-Baustelle schon heute mit sehr guten Ergebnissen zu realisieren.
Wie geht es weiter mit der Baustelle der Zukunft?
Unser Projekt mit Liebherr hat gezeigt, dass die Technologie und das Know-how da sind, um die Local-Zero-Emission-Baustelle schon heute mit sehr guten Ergebnissen zu realisieren. Wenn man die Energie- und Emissionsbilanz der Testbaustelle in Bludenz-Bürs auf ein Jahr umrechnet, könnten auf einer Baustelle dieser Größenordnung über den ausschließlichen Einsatz von E-Maschinen zirka 35.000 Liter Diesel eingespart und könnte ein CO2-Ausstoß von mehr als 92 Tonnen vermieden werden. Es würde sich also durchaus lohnen, die technologischen Potenziale rund um die E-Antriebe, Batterien und Brennstoffzellen weiter auszuschöpfen. Mit starken Partnern wie Liebherr sind wir da auf einem guten Weg. Die nächsten Jahre werden noch richtig spannend.
Liebherr freut sich auf die Bauma 2022!
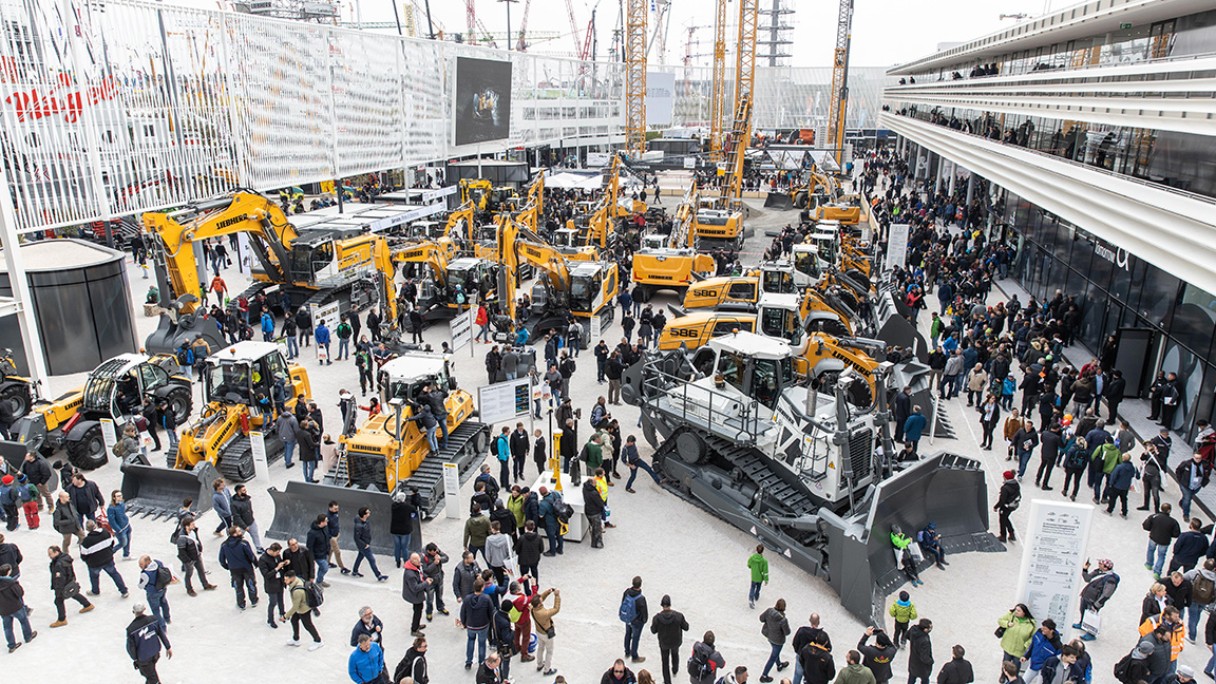
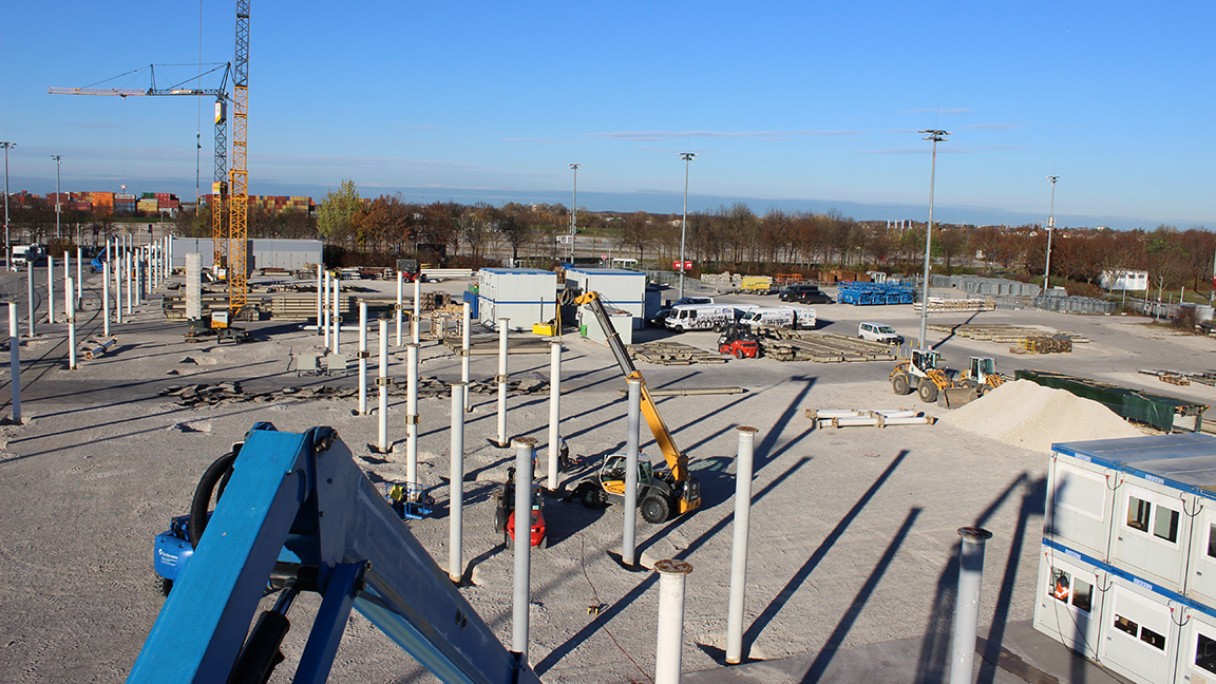