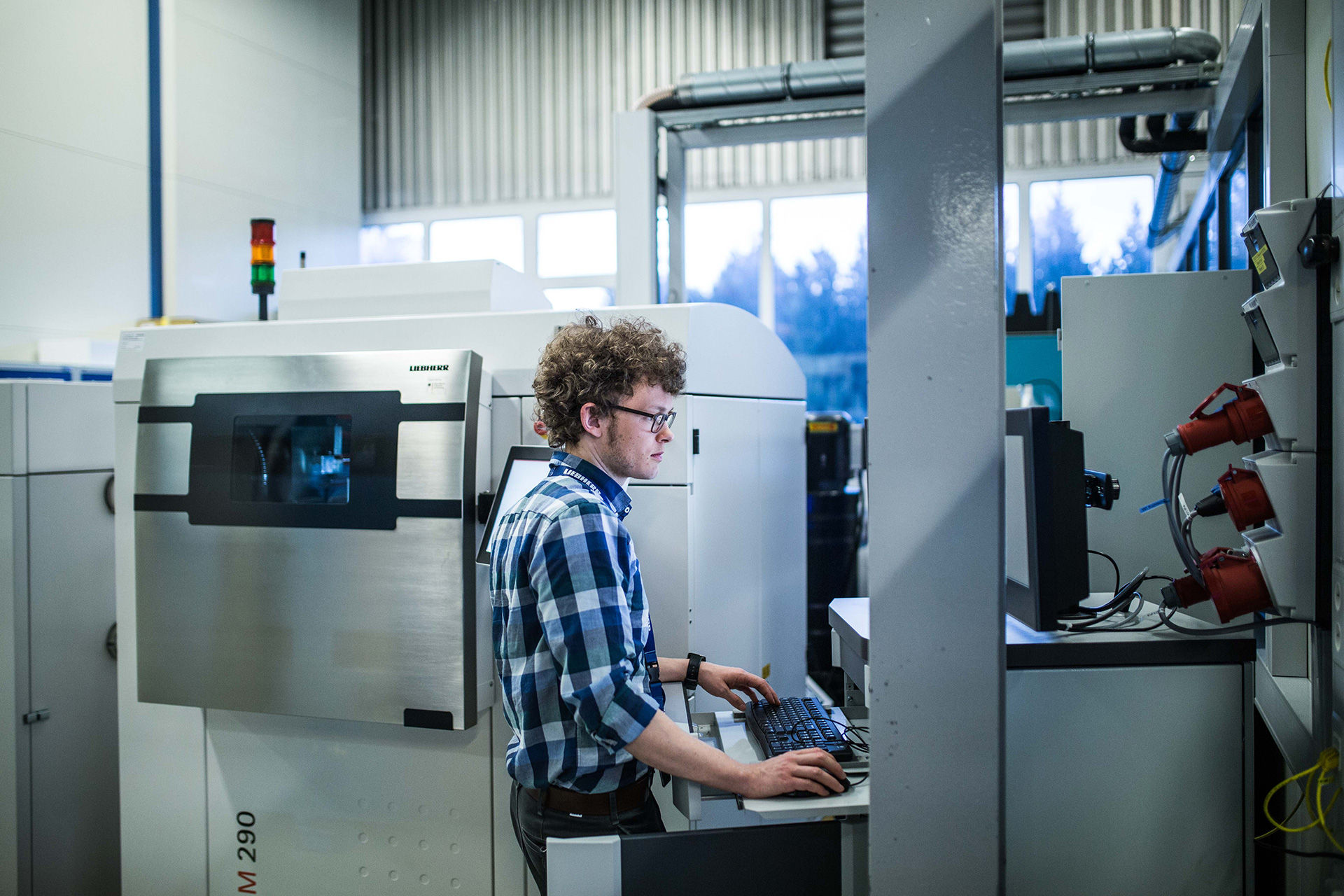
Print & Fly
Der Traum vom Fliegen geht weiter. Heute dreht er sich um das Flugzeug, das komplett aus dem 3D-Drucker kommt. Noch ist es nicht so weit. Doch ein Forscherteam von Liebherr kommt diesem Traum Schritt für Schritt näher.
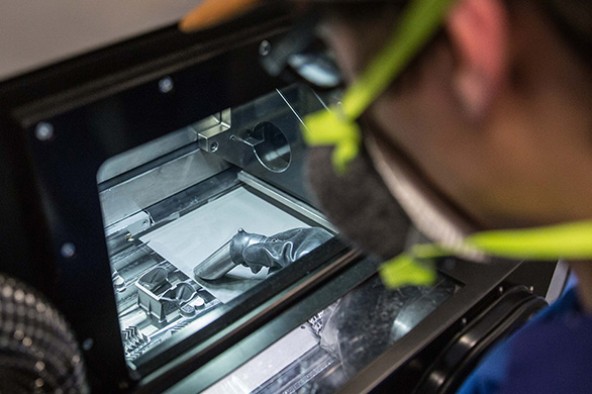
Geschichtet für die Geschichte
„Das hätte ich auch nicht gedacht, wie gut mir mal Staubsaugen gefallen würde“, sagt Adrian Führer und flanscht den Schlauch des Saugers an die Maschine an. Er tippt mit dem Finger auf den Touchscreen. Das Gerät brummt los. Durch das Guckfenster sieht er, wie sich sein Werk aus dem grauen Staub erhebt. „Das ist jedes Mal ein großer Moment, wenn sich das Bauteil in seiner ganzen Pracht zeigt“, sagt er. Der Industriemechaniker betreut bei Liebherr-Aerospace den 3D-Drucker, richtet ihn für die Druckaufträge ein, befüllt ihn mit Titanpulver, bereitet den Laser für das computergesteuerte Schmelzen des Materials vor – und saugt zu guter Letzt das überschüssige Titanpulver auf. „3D-Druck finde ich wahnsinnig spannend. Als ich gefragt wurde, ob ich das Forscherteam unterstützen wollte, musste ich nicht lange überlegen. Ich habe sofort Ja gesagt“, stellt Adrian Führer fest.
Der 3D-Drucker steht im Liebherr-Werk Lindenberg im Übergang zwischen Fertigung, Versand und Montage. Ein von Glaswänden eingefasster Produktionsbereich, in dessen Mittelpunkt die übermannsgroße Druckmaschine mit ihrer Computersteuerung. Ein großer Monitor überträgt „live“ das Geschehen im Drucker. Immer wieder bleiben vorbeilaufende Mitarbeiter und Besucher stehen, um einen Blick auf die Zukunft industrieller Fertigungstechnik zu werfen. Vorn steht ein hochglänzendes Titanbauteil für einen Airbus A320. „Gefördert durch das Bundesministerium für Wirtschaft und Energie“ steht da zu lesen.
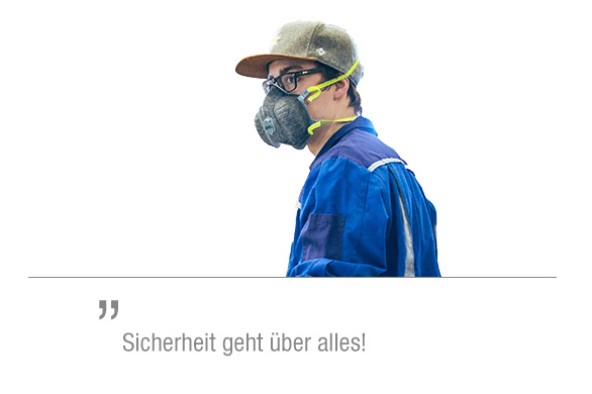
Mit großer Begeisterung berichtet Adrian Führer von seiner Arbeit. „Der Drucker baut ein Werkstück aus endlos vielen, gerade einmal 30 bis 60 Mikrometer dünnen Titanschichten auf“, sagt er. „Der Laser fährt exakt nach Konstruktionsmodellen über den Titanpuder und lässt ihn millimetergenau mit einem grellen Lichtpunkt einschmelzen. So baut sich das Werkstück Schritt für Schritt von unten nach oben auf.“ Für einen Ventilblock mit vielen verwinkelten Leitungen und Röhren, mit dessen Hilfe eine Flugzeuglandeklappe angesteuert werden kann, brauche der Drucker etwa 20 Stunden.
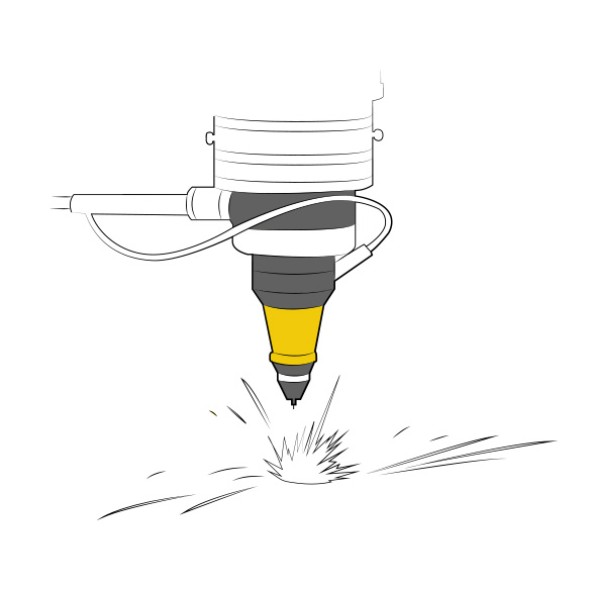
Zukunft 3D-Druck
3D-Druck – die Zukunft aus dem Laser-Schmelzer
Die Additive Fertigung bezeichnet einen Prozess, bei dem auf der Basis von digitalen 3D-Konstruktionsdaten durch das Aufschmelzen von Material schichtweise ein Bauteil aufgebaut wird. Immer häufiger wird der Begriff „3D-Druck“ als Synonym für die Additive Fertigung verwendet. Additive Fertigung beschreibt jedoch besser, dass es sich hier um ein professionelles Produktionsverfahren handelt, das sich deutlich von konventionellen, abtragenden Fertigungsmethoden unterscheidet. Anstatt zum Beispiel ein Werkstück aus einem festen Block herauszufräsen, baut die Additive Fertigung Bauteile Schicht für Schicht aus Werkstoffen auf, die als feines Pulver vorliegen. Als Materialien sind unterschiedliche Metalle, Kunststoffe und Verbundwerkstoffe verfügbar.
Diese Fertigungsmethode findet unter anderem im Rapid Prototyping Verwendung – dem Bau von Anschauungs- und Funktionsprototypen. Produktentwicklung und Markteinführung lassen sich dadurch entscheidend verkürzen. Mittlerweile hält die Additive Fertigung zunehmend Einzug in die Serienfertigung. Sie eröffnet großen OEM-Herstellern aus unterschiedlichsten Industriezweigen die Möglichkeit, sich am Markt zu differenzieren – im Hinblick auf neue Kundennutzen, Kostenreduktionspotenziale oder zum Erreichen von Nachhaltigkeitszielen.
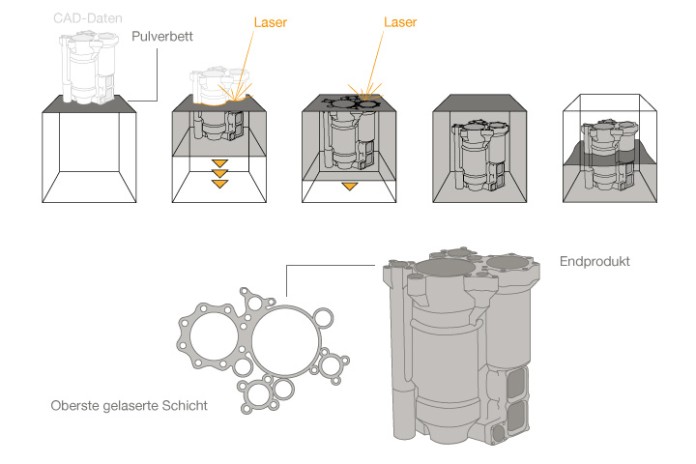
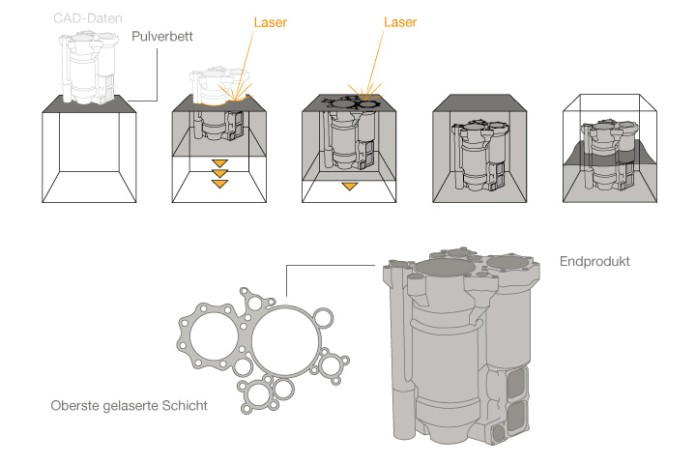
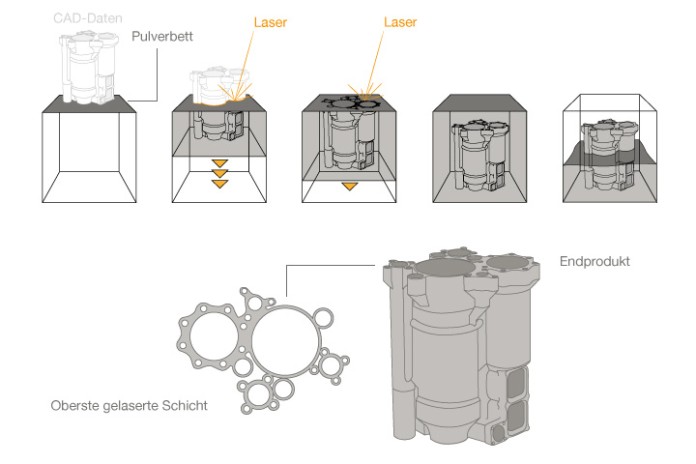
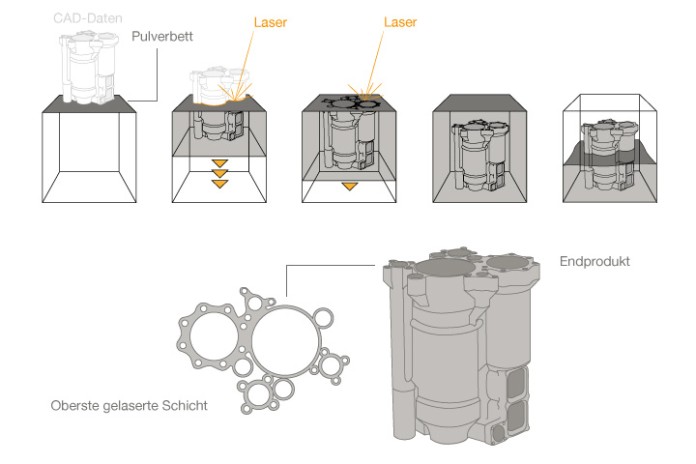
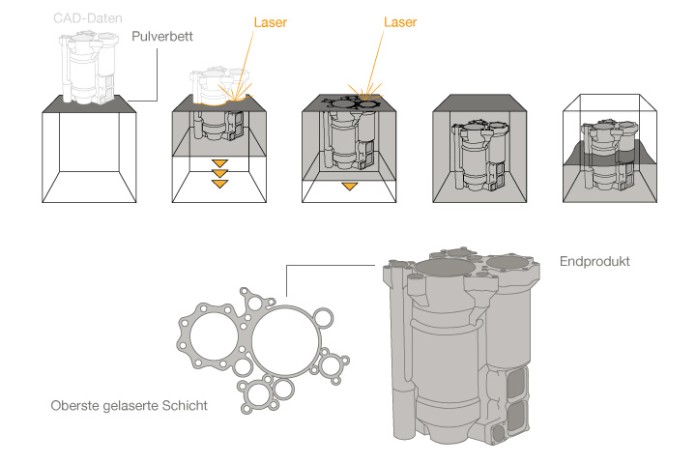
CAD-Daten
Mehr erfahren
Pulver
Mehr erfahren
Absaugen
Mehr erfahren
Laser
Mehr erfahren
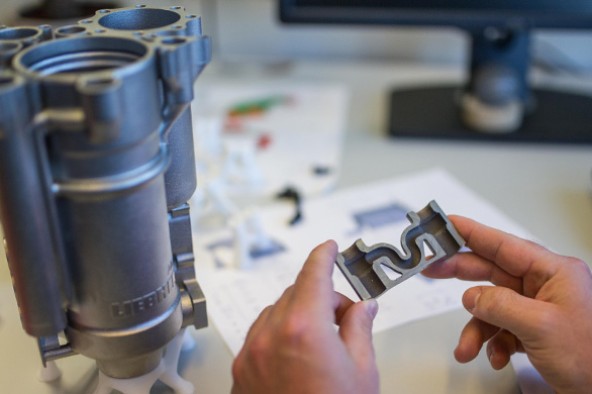
Mit der Evolution im Bunde
Die Rollen am Bürostuhl von Johannes Walter sind eine lohnende Investition. Immer wieder stößt er sich mit einem kräftigen Fußtritt ab und saust die zwei Meter hinüber zu Stefan Hermann. Die beiden sitzen im Büro Rücken an Rücken und haben gerade viel Gesprächsbedarf. Stefan Hermann ist Simulationsingenieur. Auf seinem Bildschirm hat er ein komplexes Strukturgeflecht. „Das hat sich die Evolution ausgedacht“, sagt er. „Die Struktur ist einer Baumwurzel nachempfunden. Sie findet mit ihren Verästelungen immer die richtige Balance zwischen Materialeinsatz, Festigkeit und Versorgung des Baums. Wofür die Evolution Millionen von Jahren gebraucht hat, konnten wir den Rechner nutzen, um nach dem gleichen Optimierungsprinzip daraus eine Leichtbau-Verbindung für ein Fahrwerkbauteil für ein Flugzeugs zu konstruieren“, erklärt Hermann.
Deswegen ist auch Johannes Walter bei ihm vorgefahren. Der Konstrukteur spielt mit dem Simulationsingenieur den kreativen Doppelpass. Walter macht aus Hermanns Berechnung eine Form, die am Ende in das Fahrwerk verbaut wird. Das von ihm aufgebaute Bauteil sieht auf seinem Rechner aus wie ein Halbmond, dessen Oberfläche löchrig ist wie ein Schweizer Käse. „Das spart Material und Gewicht“, sagt Walter, „und nutzt die idealtypisch berechneten Festigkeitsstrukturen.“ So ließe sich im CAD nahezu jede Form darstellen und dann im 3D-Druck hundertprozentig exakt so fertigen, wie sie die Entwickler für die angestrebte Funktion bräuchten.
Wir vermessen und dokumentieren jeden noch so kleinen Schritt im Aufbau des Bauteils. Fehler sind keine Option.
Die beiden Tüftler gehören zum sechsköpfigen Team von Alexander Altmann, dem Leiter des Projekts Additive Manufacturing / Research & Technology, das Liebherr vor sechs Jahren in Lindenberg an den Start gebracht hat. „3D-Druck ist eine über 20 Jahre alte Technologie, die zuletzt einen ungeheuren Aufschwung genommen hat und speziell im Flugzeugbau hochinteressante Perspektiven zeigt“, sagt Altmann. „Kürzlich ist ein Spoiler-Aktuator-Ventilblock, den wir per 3D-Druck hergestellt haben, in einem A380 getestet worden. Die erste 3D-gedruckte Hydraulikkomponente der primären Flugsteuerung, die jemals in einem Airbus zum Einsatz kam! Genauso leistungsfähig wie ein herkömmlich hergestellter Ventilblock, aber um 35 Prozent leichter.“
Nachdem die Anforderungen an Flugzeugbauteile enorm hoch seien, gehe es ihm und seinem Team vor allem darum, die additiven Fertigungsverfahren bis ins letzte Detail zu verstehen und absolut verlässliche Produktionsprozesse aufzusetzen. „Wir vermessen und dokumentieren dazu jeden noch so kleinen Schritt im Aufbau des Bauteils. Fehler sind keine Option. Die Bauteile und ihr Material erlauben nicht den kleinsten Zweifel an der Zuverlässigkeit und Sicherheit.“
Indem Sie auf „AKZEPTIEREN“ klicken, willigen Sie für dieses Video gemäß Art. 6 Abs. 1 lit. a DSGVO in die Datenübermittlung an Google ein. Wenn Sie künftig nicht mehr zu jedem YouTube-Video einzeln einwilligen und diese ohne diesen Blocker laden können möchten, können Sie zusätzlich „YouTube-Videos immer akzeptieren“ auswählen und damit auch für alle weiteren YouTube-Videos, welche Sie zukünftig auf unserer Website noch aufrufen werden, in die jeweils damit verbundenen Datenübermittlungen an Google einwilligen.
Erteilte Einwilligungen können Sie jederzeit mit Wirkung für die Zukunft widerrufen und damit die weitere Übermittlung Ihrer Daten verhindern, indem Sie den entsprechenden Dienst unter „Sonstige Dienste (optional)“ in den Einstellungen abwählen (später auch aufrufbar über die „Datenschutzeinstellungen“ in der Fußzeile unserer Website ).
. Weitere Informationen erhalten Sie in unserer Datenschutzerklärung sowie in der Google-Datenschutzerklärung.Datenschutzerklärung von Google.*Google Ireland Limited, Gordon House, Barrow Street, Dublin 4, Irland; Mutterunternehmen: Google LLC, 1600 Amphitheatre Parkway, Mountain View, CA 94043, USA** Hinweis: Die mit der Datenübermittlung an Google verbundene Datenübermittlung in die USA erfolgt auf Grundlage des Angemessenheitsbeschlusses der Europäischen Kommission vom 10. Juli 2023 (EU-U.S. Data Privacy Framework).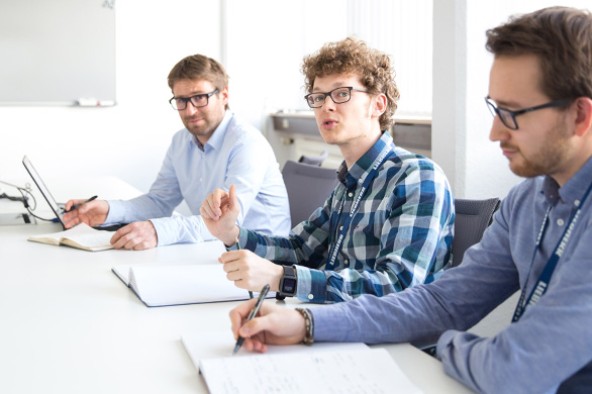
Lust auf Zukunft
Das Team von Alexander Altmann hat sich zum Jour fixe im Konferenzraum versammelt. André Danzig ist erst seit eineinhalb Jahren im Team. Und doch ist der promovierte Physiker eine Art „Urgestein“ der Additiven Fertigung. Bevor er nach Lindenberg kam, hat er über 15 Jahre bei einem 3D-Drucker-Hersteller gearbeitet. Dann wollte er einmal näher die Anwenderseite kennenlernen. „Was sagt uns die Simulation? Wie kriegen wir die Stabilität der Konstruktion hin, wenn wir nicht nur die einzelnen Komponenten drucken, sondern das gesamte Steuerelement und dabei alle Funktionen integrieren?“, will Danzig wissen. Stefan Hermann hat das alles schon berechnet und sich dazu auch bereits mit dem Designer ausgetauscht. „Wir kriegen das auf jeden Fall hin“, sagt Hermann und stellt dem Team die entsprechenden Überlegungen vor.
Indem Sie auf „AKZEPTIEREN“ klicken, willigen Sie für dieses Video gemäß Art. 6 Abs. 1 lit. a DSGVO in die Datenübermittlung an Google ein. Wenn Sie künftig nicht mehr zu jedem YouTube-Video einzeln einwilligen und diese ohne diesen Blocker laden können möchten, können Sie zusätzlich „YouTube-Videos immer akzeptieren“ auswählen und damit auch für alle weiteren YouTube-Videos, welche Sie zukünftig auf unserer Website noch aufrufen werden, in die jeweils damit verbundenen Datenübermittlungen an Google einwilligen.
Erteilte Einwilligungen können Sie jederzeit mit Wirkung für die Zukunft widerrufen und damit die weitere Übermittlung Ihrer Daten verhindern, indem Sie den entsprechenden Dienst unter „Sonstige Dienste (optional)“ in den Einstellungen abwählen (später auch aufrufbar über die „Datenschutzeinstellungen“ in der Fußzeile unserer Website ).
. Weitere Informationen erhalten Sie in unserer Datenschutzerklärung sowie in der Google-Datenschutzerklärung.Datenschutzerklärung von Google.*Google Ireland Limited, Gordon House, Barrow Street, Dublin 4, Irland; Mutterunternehmen: Google LLC, 1600 Amphitheatre Parkway, Mountain View, CA 94043, USA** Hinweis: Die mit der Datenübermittlung an Google verbundene Datenübermittlung in die USA erfolgt auf Grundlage des Angemessenheitsbeschlusses der Europäischen Kommission vom 10. Juli 2023 (EU-U.S. Data Privacy Framework).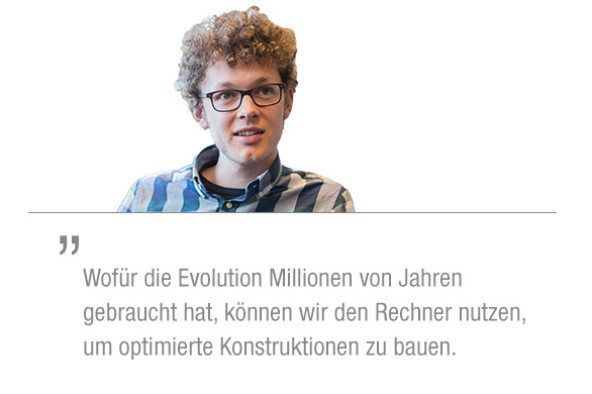
Das gefällt Alexander Altmann: „Der 3D-Druck wird nicht nur Flugzeugkomponenten und ganze Flugzeugstrukturen grundlegend verändern, sondern auch weitere Produkte wie Autos und Spielzeuge. Selbst die Herstellung von Lebensmitteln und medizinischen Implantaten wird möglich sein. Ich bin sicher: Die Auswirkungen in den nächsten 20 Jahren werden gigantisch sein.“