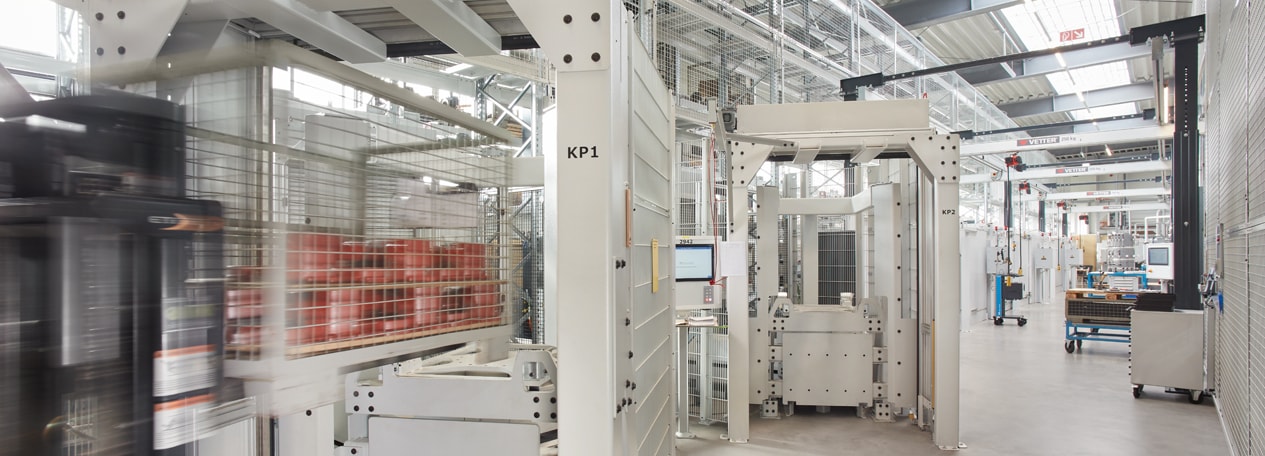
Weg vom täglichen Rüsten
Wie stelle ich in meiner Fertigung die größtmögliche Produktivität sicher? Welche Automatisierung ist für meine hohe Teilevielfalt sinnvoll und welcher Partner setzt meine Pläne nach meinen Wünschen zuverlässig um? Jedes produzierende Unternehmen stellt sich solche und ähnliche Fragen, wenn es um die Steigerung der Produktivität geht. Die im westfälischen Dülmen beheimatete Kordel Antriebstechnik GmbH hat für ihre Getriebefertigung mit einem Palettenhandhabungssystem von Liebherr mit einigen individuellen Anpassungen die richtige Antwort gefunden.
Zum Angebot von Kordel gehören Getriebe für Flurförderfahrzeuge, Getriebe für Landmaschinen, etwa für Erntevorsätze in Maishäckslern und Mähdreschern, sowie Getriebe für Baumaschinen, zum Beispiel für Straßenfräser und -fertiger im Straßenbau. Kordel ist einer von wenigen Getriebelieferanten, die eine hohe Fertigungstiefe haben, um vom Rohling bis zum fertigen Getriebeteil jeden Arbeitsgang abzudecken – inklusive Härten und Nitrieren bis hin zur Montage. Insgesamt fertigt das Unternehmen etwa 325.000 Getriebe im Jahr.
Die Grundüberlegung lautete, das tägliche Rüsten, das an Stand-Alone-Maschinen erforderlich ist, durch automatisierte Abläufe zu ersetzen. Johannes Kordel, einer der Geschäftsführer und bei Kordel für die technische Leitung zuständig, ist bereits seit 35 Jahren im Unternehmen tätig. Gemeinsam mit seinem Team hat er sich für sein großes Automatisierungsprojekt gründlich auf dem Markt umgesehen. Um die Automatisierung erfolgreich zu planen, ist es wichtig, alle Gegebenheiten zu kennen und die Anforderungen gegeneinander abzuwägen.
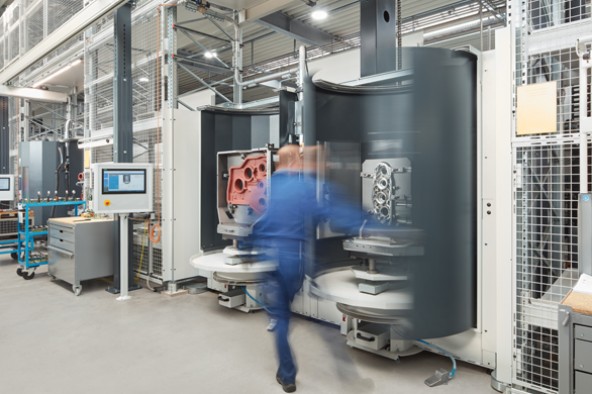
Nah beieinanderliegende Rüstplätze erlauben schnelles Handeln
Präzise definierte Anforderungen
„Hauptzeitparallel“ ist und bleibt das große Stichwort, wenn es um die optimale Auslastung von Werkzeugmaschinen geht. Wenn alle Vorgänge, die nicht unmittelbar zur eigentlichen Bearbeitung gehören, an anderer Stelle gleichzeitig stattfinden und alle Teile rechtzeitig an die nächste Station gebracht werden, ist die Maschine optimal ausgelastet und teure Stillstände bleiben die Ausnahme. Neben dem Preis und der Qualität ist die Termintreue die dritte Säule, die Lieferanten gewährleisten müssen, um sich im Wettbewerb zu behaupten.
Vor vier Jahren begannen die Planungen, die Fertigung in Dülmen ebenso wie am zweiten Produktionsstandort in Jawor, Polen, mit automatisierten Anlagen zu modernisieren. Für neue Bearbeitungszentren, auf denen Getriebeteile aus Guss und Aluminium gebohrt und gefräst werden, entstand eine automatisierte Materialversorgung vom Lager zur Maschine und wieder zurück. Zwei Anlagen mit je zwei Strängen des PHS 1500 Pro bedeuteten den bisher größten Einzelauftrag für die Palettenhandhabungssysteme bei Liebherr.
In der Projektierung wurden zunächst alle Abläufe betrachtet und anschließend für jeden einzelnen Schritt entschieden, ob er künftig automatisiert oder händisch ausgeführt werden soll. „Es sieht bei uns an manchen Stellen anders aus als in anderen Firmen, aber wir haben uns an allen Stellen für die jeweils am passendsten scheinende Arbeitsweise entschieden“, beschreiben die für die Programmierung, den Vorrichtungsbau und die Zerspanung verantwortlichen Meister Peter Hörsting und Dirk Strotmann rückblickend das Projekt. Während die Minimierung der Rüstzeiten, die zuvor etwa ein Drittel der Maschinenzeit beanspruchten, das Hauptargument für die Automatisierung in Dülmen war, bestimmte in Jawor der Fachkräftemangel die Entscheidung.
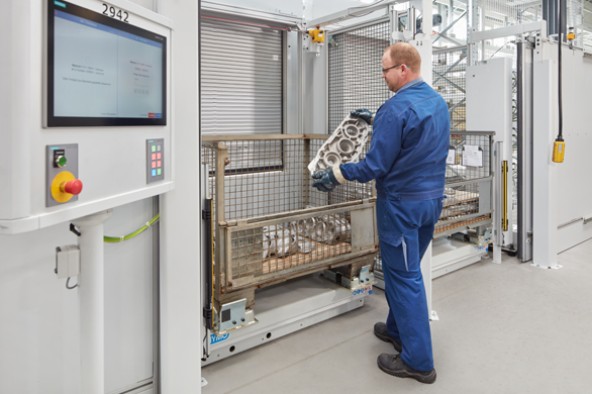
Entnahme des Rohteils aus dem Materiallagersystem zum Aufspannen auf den gegenüberliegenden Rüstplatz. Der Hubtisch unter der Gitterbox ist für die Entnahme abgesenkt
Mit zwei Strängen zur individuellen Lösung
Da Kordel mit ca. 25.000 Eigenfertigungsteilen eine große Teile vielfalt anbietet, muss die Materialversorgung hierauf abgestimmt sein. Die Abläufe sind bestimmt durch die Losgrößen von typischerweise fünf bis 30 Teilen pro Auftrag. Entsprechend ist die Materialbeschaffung ein sensibler Punkt: Das Shuttle, das die Rohteile zur Maschine bringt, darf nicht zum Engpass werden. „Das Bearbeitungszentrum ist die teuerste Komponente, sie muss immer laufen und darf nie auf die angeschlossenen Systeme warten“, fasst Kordel die wichtigste Vorgabe zusammen. Schnell war klar, dass dies bei der geforderten Taktfrequenz mit einem einzigen System nicht zu machen war. Deshalb besteht die Anlage jetzt aus zwei Strängen, einem Materiallagersystem und einem Fertigungssystem mit je einem Regalbediengerät. Die zwei Systeme kommunizieren permanent über die gemeinsame Leitsteuerung miteinander. Als die Idee für die Architektur mit zwei Strängen stand, erfolgte die Berechnung, wie viele Maschinen über ein solches System zu bedienen wären. Im Ergebnis sind die PHS heute für bis zu sechs Maschinen ausgelegt. An beiden Standorten stehen aktuell bereits je fünf baugleiche Bearbeitungszentren.
Die Stränge sind parallel angeordnet, sodass die Wege zwischen beiden Seiten möglichst kurzgehalten sind. Um eine hohe Frequenz und kurze Taktzeiten zu halten, müssen die Abläufe an allen Übergabepunkten reibungslos sein. Auf der Materialseite gibt es zwei Be- und Entladestationen für Gabelstapler und acht für die händische Entnahme. Fährt ein bearbeitetes Gehäuse aus der Maschine über Regalbediengerät 1 in eine Rüststation des Fertigungssystems, wird aus dem Materiallagersystem je eine Gitterbox für die Fertigteile, wie auch eine Gitterbox mit Rohteilen über Regalbediengerät 2 ausgeschleust. Es ist erforderlich, dass alle benötigten Werkzeuge hinterlegt und bevorratet sind. Wenige, sehr spezielle Messmittel, sind nicht an allen Bearbeitungsstationen vorgesehen, die Mehrzahl der Werkstücke soll allerdings an allen Stationen zu bearbeiten sein. Neben den sechs Rüstplätzen auf der Maschinenseite, von denen je zwei nebeneinander liegen und von insgesamt drei Mitarbeitern bedient werden, gibt es einen separaten Platz für kompliziertere Artikel, neue Vorrichtungen oder Problemfälle, damit die Mitarbeiter an den Doppel-Stationen ungestört weiterarbeiten können. Die Maschine arbeitet den Auftrag ab und bringt die Vorrichtung wieder zurück. Jedes Bauteil hat ein eigenes Hebezeug, das rechtzeitig bereitgestellt werden muss. Auch diese werkstückspezifischen Zubehörteile gehören zu einer gelungenen Automatisierung.
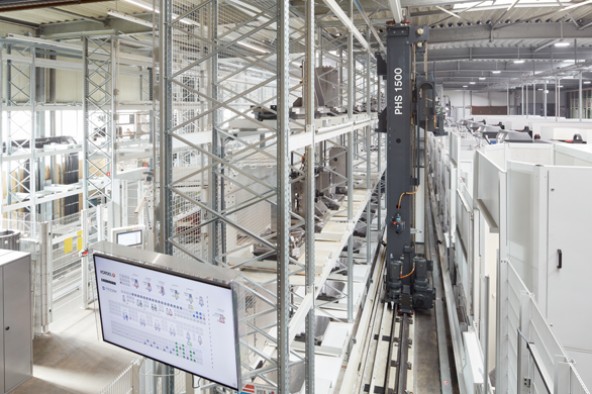
Befüllen des Materiallagersystems mit neuen Rohlingen
Nicht von der Stange
Die Einzigartigkeit des Systems ist allein schon durch die parallel angeordneten Regalstränge des Materiallagers und des flexiblen Fertigungssystems mit gemeinsamer Leitsteuerung gegeben. Darüber hinaus wurden auf Wunsch von Kordel Hubtische zur Absenkung auf der Entnahmeseite des Bevorratungsstrangs installiert. Die Gitterboxen auf normaler Höhe des Regalbediengeräts sind für die händische Entnahme zu hoch. In hoher Position übernimmt der Tisch die Box aus dem Gerät und fährt dann herunter, sodass der Bediener das Bauteil bequem herausnehmen und auf der Rüstpalette im Bearbeitungsstrang einspannen kann. Die Tische wurden ebenfalls von Liebherr geliefert, gehören aber nicht standardmäßig zum PHS. Johannes Kordel urteilt: „Die technische Ausführung der mechanischen Teile hat uns gefallen, ebenso das saubere Umfeld. Das Erscheinungsbild erfüllt unsere Anforderungen und die unserer Kunden, die regelmäßig zu Audits bei uns im Haus sind.“
Wir haben unsere Vorstellungen formuliert und daraus ist ein System entstanden, das genau zu unserer Situation passt. Bei anderen Firmen, die nur eine Katalogbestellung zulassen, ist dies so nicht möglich.
Die Zusammenarbeit
Neben der technischen Kompetenz, die Liebherr schon mit einer Verzahnmaschine in der Getriebefertigung bei Kordel unter Beweis stellen konnte, gaben auch die Kommunikation und die Flexibilität von Liebherr den Ausschlag für die erneute Zusammenarbeit beim Automatisierungsprojekt. „Der erste Termin mit allen Ansprechpartnern kam sehr kurzfristig, innerhalb von 14 Tagen, zustande. An diesem Termin konnten zunächst alle unsere Fragen beantwortet werden. Dies hat uns für die Projektierung von Anfang an ein gutes Gefühl gegeben“, erinnert sich Johannes Kordel an den Beginn der Planung. Besonders gut hat ihm gefallen, dass Liebherr zugehört hat. „Wir haben unsere Vorstellungen formuliert und daraus ist ein System entstanden, das genau zu unserer Situation passt. Bei anderen Firmen, die nur eine Katalogbestellung zulassen, ist dies so nicht möglich.“ Nachdem die Entscheidung für das PHS 1500 Pro gefallen war, wurden im regelmäßigen, oft täglichen Austausch, alle Details besprochen und individuell gelöst. Die auch für Liebherr neue Architektur mit zwei Strängen und die verschiedenen Anpassungen machten das Projekt für beide Seiten zu einer spannenden Erfahrung. Die Stärke von Liebherr liegt in der flexiblen Umsetzung individueller Kundenwünsche. So übernimmt Liebherr auch die Anbindung an vorhandene Fertigungssysteme und passt die Schnittstellen an. Bei Kordel kommunizieren alle Elemente der neuen Fertigungsstraße über den bereits vorhandenen Leitrechner der Berliner Firma PROCAM Steuerungstechnik.
Knut Jendrok, Gebietsverkaufsleiter für Palettenhandhabungssysteme bei Liebherr, betont: „Die konkreten Fragestellungen, die Kordel in die Planung einbrachte, sind nicht selbstverständlich. Dass ein Kunde seine Anforderungen so genau und an die Gegebenheiten angepasst formuliert, ist äußerst hilfreich. So arbeitet man sich gut gegenseitig zu und es wird ein produktives Miteinander.“
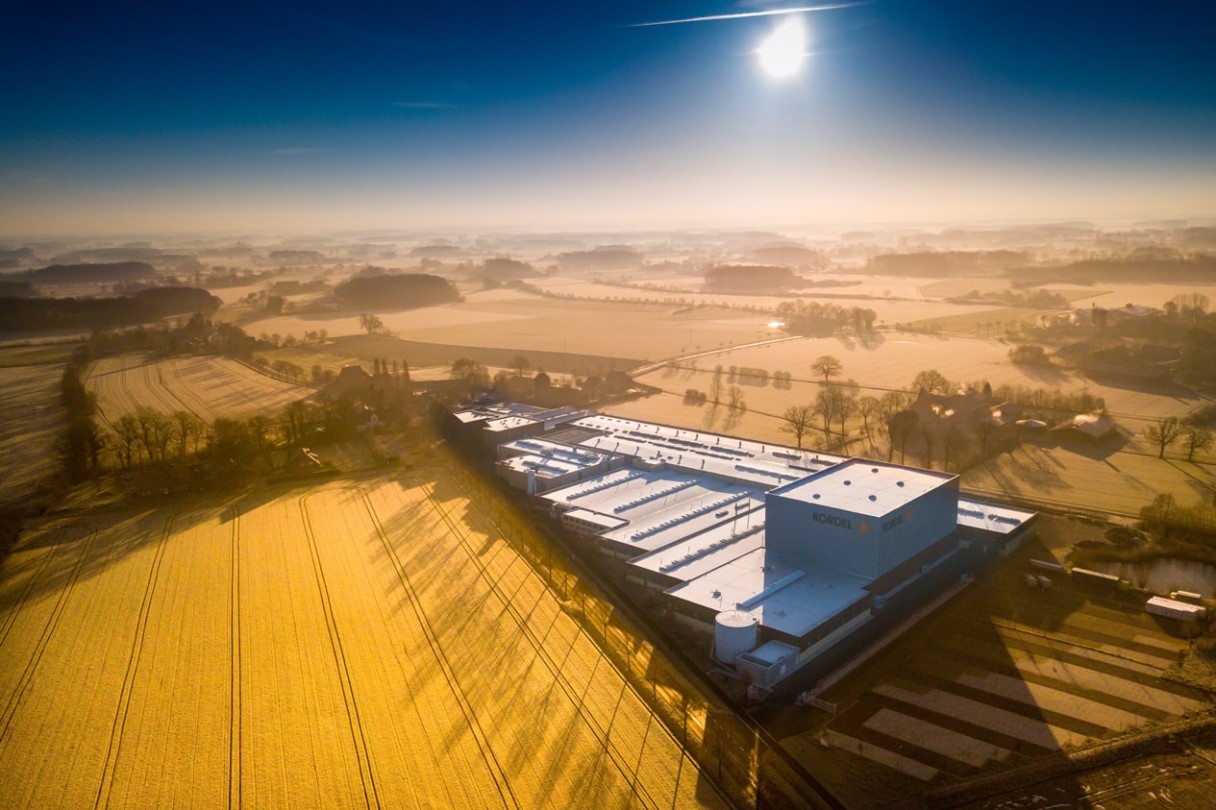
Das Werk der Kordel Antriebstechnik GmbH in Dülmen-Rödder
Kordel Antriebstechnik GmbH
Branche: Getriebefertigung für Flurförderzeuge, Landmaschinen, Baumaschinen
Firmengröße: 950 Mitarbeiter
Gegründet: 1879 als Schmiede
Unternehmenszentrale:Dülmen, Deutschland
Standorte: Dülmen-Rödder, Dülmen-Dernekamp, Jawor (Polen)
Umsatz: Circa 140 Mio. Euro / Jahr
Website: www.kordel.de