Genauer gesagt sind es sogar zwei Mini-Maschinen, die im Ausbildungszentrum der Liebherr-Verzahntechnik GmbH gefertigt wurden. Mit einer Kantenlänge von jeweils etwa einem Meter und einem Gewicht von ca. 250 Kilogramm haben sie zwar nicht gerade Handtaschenformat, dafür kann man aber echte Kunststoffzahnräder auf ihnen wälzfräsen und sogar komplett bearbeiten – gesteuert von der LHGearTec-Software. „Die Anregung stammte ursprünglich aus der Entwicklungsabteilung“, erzählt Ausbildungsleiter Matthias Fendt. „Dort wünschte man sich ein handliches Maschinenmodell, um Achsbewegungen und Kinematiken besser veranschaulichen zu können. Daraus folgte die Idee, eine solche Maschine im Ausbildungszentrum bauen zu lassen, denn wir sind immer auf der Suche nach möglichst praxisnahen und interdisziplinären Projekten.“
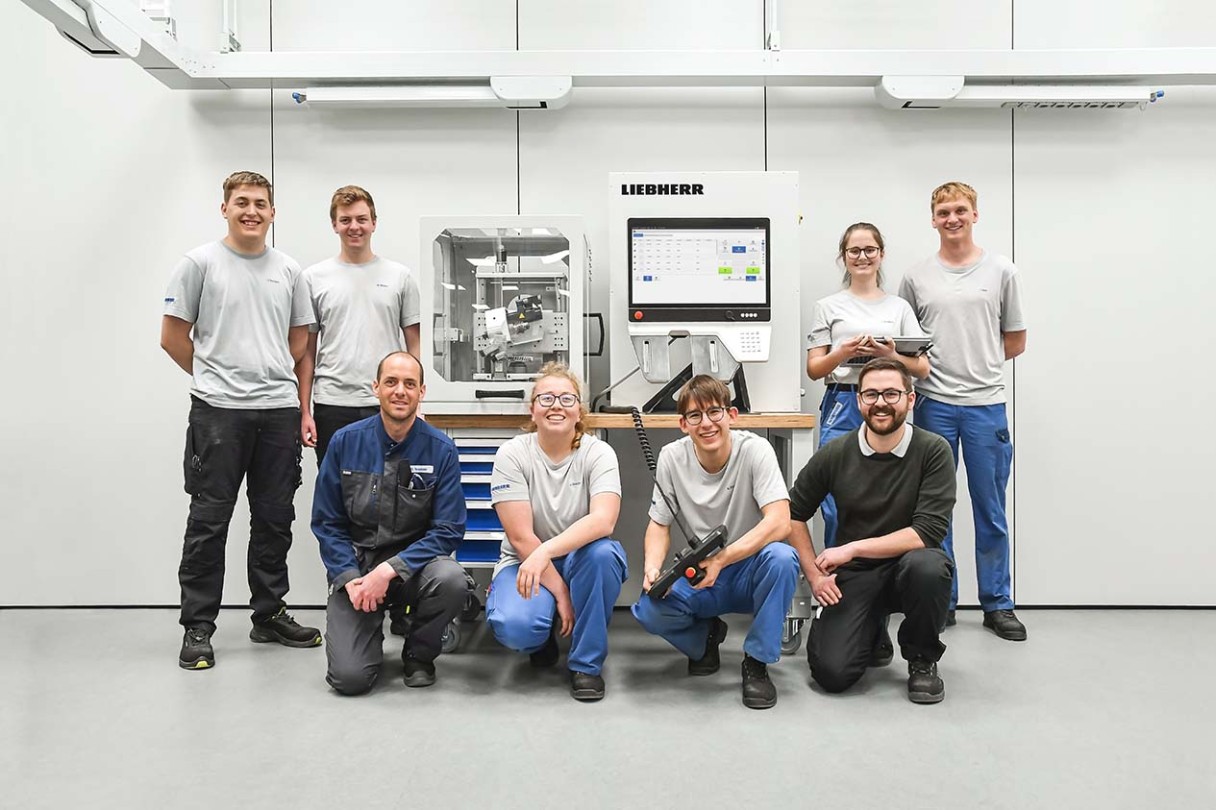
Challenge geschafft! Die Industriemechanik-Azubis und Ausbilder mit der selbst gebauten Miniatur-Fräsmaschine
Modell-Maschine zur Veranschaulichung
Auch die Azubis profitieren von der Modell-Maschine. „Am Anfang der Ausbildung kommen die Azubis noch nicht so intensiv mit den verschiedenen Verzahnungstechnologien in Kontakt“, so Fendt weiter. „Daher sind gerade bei mehreren Maschinenachsen die Achsbewegungen manchmal schwierig zu veranschaulichen. Mit den Modell-Maschinen lässt sich vieles gut demonstrieren.“ Auch wenn die Miniatur-Maschinen keine Eins-zu-eins-Kopie der „echten“ Maschinen sind, sind sie auf ihre wesentlichen Funktionen reduziert und damit einfacher und variabler zu Ausbildungs- und Simulationszwecken zu nutzen. Daher spielt es auch keine Rolle, dass die fertigen Zahnräder aus Kunststoff sind. Es geht um die Vermittlung von Grundlagen. „Und so können wir das Verständnis unserer Produkte noch frühzeitiger und stärker in die Ausbildung integrieren“, erläutert Fendt.
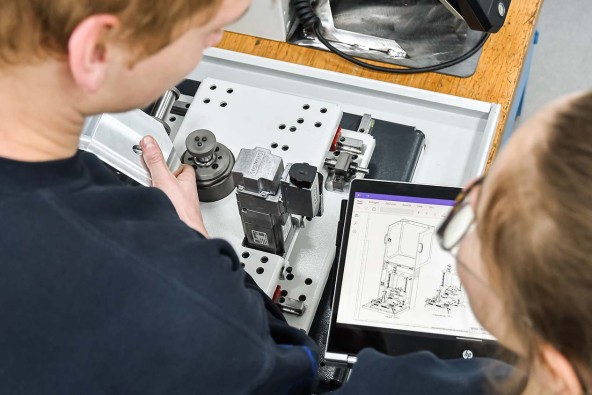
Selbstständig und interdisziplinär
Liebherr legt schon während der Ausbildung großen Wert auf Selbstständigkeit und Interdisziplinarität. Das Projekt war in der gemeinsamen Verantwortung der Azubis in den Ausbildungsberufen Industriemechanik, Produktdesign, Elektronik und dem Verbundstudium. „Die Planung haben wir weitgehend den Azubis überlassen. Bei der Konstruktion und dem Bau des Prototypen waren sie mit der ein oder anderen Herausforderung konfrontiert. Wir Ausbilder waren zwar als Lerncoaches immer im Hintergrund, aber die Azubis haben sich eigenverantwortlich organisiert und immer eine passende Lösung gefunden“, berichtet Fendt stolz. Großer Wert wird in der Ausbildung auch auf den handwerklichen Aspekt gelegt – alles, was nicht zugekauft werden musste, stellten die Azubis selbst her.
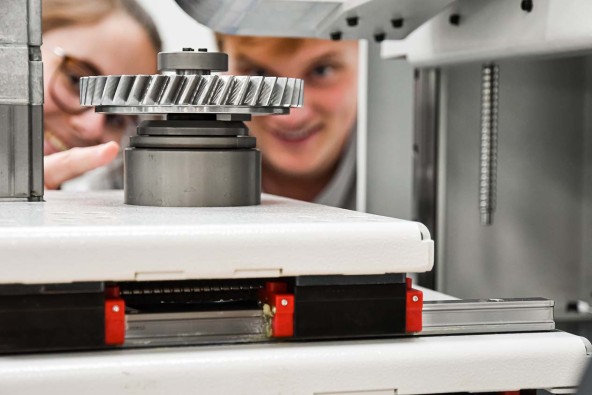
„Manchmal zum Haareraufen, aber sehr lehrreich“
Und was sagen die Azubis selbst? Alle empfanden das Teamwork in einem realen Projekt und den Blick über den Tellerrand als bereichernd. „Hier konnte man sich richtig einbringen und Dinge ausprobieren“, erzählt Industriemechanik-Azubi Michael Weixler. „Es war eine echte Herausforderung, eine Neukonstruktion umzusetzen und in der Entwicklung Dinge zu planen, die dann in der Realität erstmal nicht funktionierten. Manchmal haben wir uns wirklich die Haare gerauft“, erinnert sich Rebekka Dietrich, ebenfalls Industriemechanik-Azubi. „Aber es war eines der besten Projekte und hat uns viel gebracht. Wir haben richtig viel gelernt, weil wir nicht wegen jeder Kleinigkeit den Ausbilder fragen mussten und trotzdem immer Rückhalt hatten.“ So ist der gesamte Verzahnungsprozess für die Azubis um einiges greifbarer geworden. Und nicht nur das mechanische Verständnis ist gewachsen, sondern auch das Bewusstsein, wie wichtig Kooperation und Zusammenarbeit zwischen den Fachrichtungen sind.