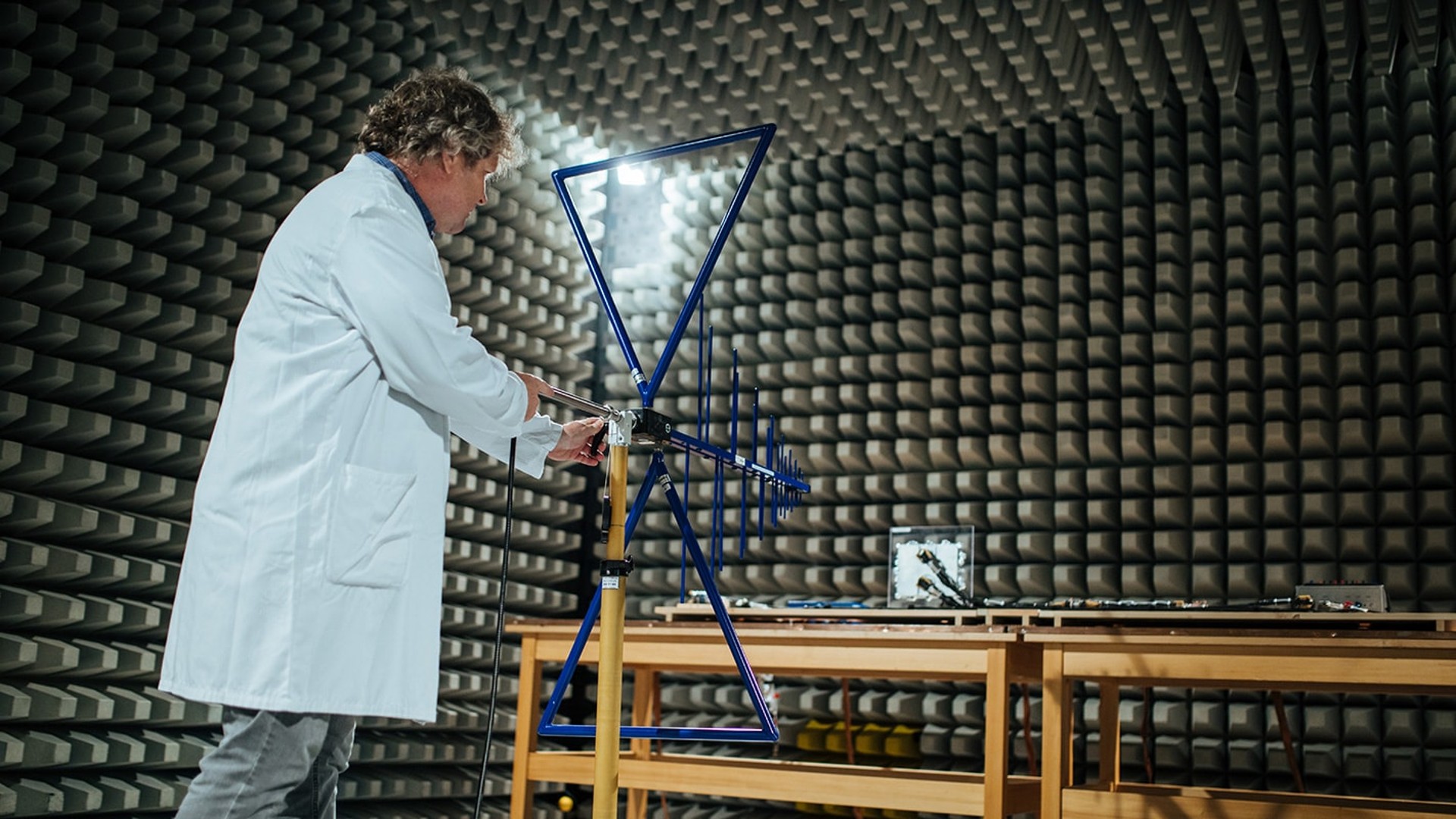
6 Minuten Lesezeit
Elektronik auf dem Prüfstand
Elektrische Komponenten unterliegen während ihrer Lebensdauer einer Vielzahl an Umwelteinflüssen. Mit modernster Prüf- und Messtechnik gewährleisten Experten des Liebherr-Test-Centers für Elektronik in Lindau ihre Leistungsfähigkeit und Sicherheit. Christian Nuber, Leiter des Prüflabors, erläutert im Interview wie die zum Teil sicherheitsrelevante Elektronik getestet wird.
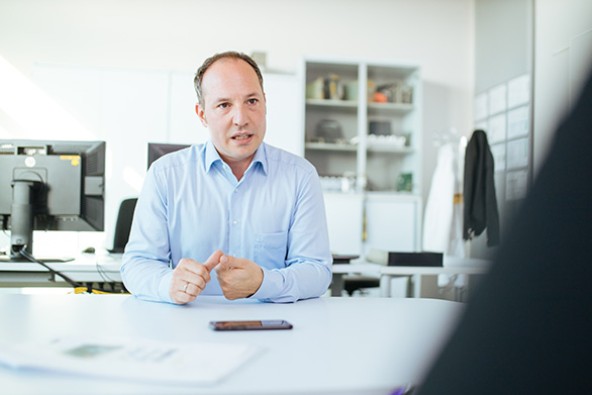
Herr Nuber, was sind die Vorteile eines Liebherr-eigenen Prüflabors für Elektronik?
Die Liebherr-Elektronik GmbH ist das Kompetenzzentrum für Elektronik der Firmengruppe Liebherr. Am Standort entwickeln und produzieren wir elektronische Steuergeräte und Leistungselektronik, die in verschiedenen Liebherr-Produkten und -Technologien zum Einsatz kommen. Diese elektrischen Komponenten müssen auf Herz und Nieren geprüft werden – sowohl während ihrer Entwicklung als auch bei der Zulassung vor der Serienproduktion. Abhängig von ihrem Einsatzort sind die Komponenten verschiedenen Umwelteinflüssen ausgesetzt, die ihre Funktion nicht beeinflussen dürfen. Mit verschiedenen Prüfverfahren können wir die Qualität und Zuverlässigkeit der Komponenten nachweisen. Neben gängigen Umwelteinflüssen lassen sich im Prüflabor auch individuelle Tests nach internationalen Standards durchführen. Seit 2012 bieten wir diese Kompetenzen auch externen Kunden an.
Welche elektronischen Komponenten überprüfen Sie im Test-Center?
Liebherr fertigt Produkte für eine Vielzahl an Branchen: von Baumaschinen und Mining über Verzahntechnik bis hin zu Lösungen für den Bereich Luftfahrt und Verkehrstechnik. Wir testen deshalb verschiedenste Komponenten: von Bedien- und Anzeigegeräten über Steuergeräte bis hin zu Leistungselektroniken, die hochgradig sicherheitsrelevant sind. Der Ausfall eines Steuergeräts, etwa als Teil einer Klimaanlage an Bord eines Flugzeugs, kann verheerende Auswirkungen haben. Regelt das Steuergerät den Kabinendruck nicht korrekt, kann das gesundheitliche Auswirkungen auf alle Passagiere haben – auch wenn die Komponente selbst nur ein kleiner Teil der gesamten Flugzeugarchitektur ist.
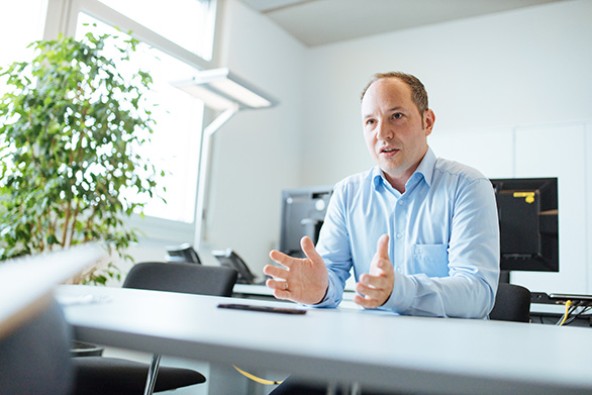
Wie läuft der Test eines elektronischen Bauteils in der Regel ab?
Das ist sehr schwer zu sagen. Immer unterschiedlich. Je nachdem, wo das Bauteil zum Einsatz kommt muss es bestimmte Anforderungen erfüllen. Diese sind festgelegt in einer Vielzahl von nationalen und internationalen Standards und Normen. Die Einhaltung dieser Anforderungen weisen wir dann über verschiedene Testverfahren nach.
Die Anforderungen legen fest welche Umwelteinflüsse, wie etwa bestimmte Temperaturen, Vibrationen oder elektromagnetische Wellen, der Prüfling aushalten muss. Eine Leistungselektronik, die in einem Offshore-Kran verbaut wird, muss etwa einen Test in der Salz-Nebel-Kammer bestehen, die das salzhaltige Klima auf dem Meer simuliert.
Alternativ prüfen wir aber auch, wie eine elektrische Komponente selbst ihre Umwelt beeinflusst. Sendet die elektrische Komponente etwa selbst elektromagnetische Strahlung aus, die möglicherweise andere Geräte stören oder die menschliche Gesundheit nachhaltig beeinträchtigen könnte?
Elektromagnetische Verträglichkeit
In einer EMV-Kammer wird die elektromagnetische Verträglichkeit von Bauteilen getestet. Mit Hilfe einer Antenne werden elektromagnetische Felder erzeugt, um zu prüfen wie die elektrische Komponente darauf reagiert. Zudem kann gemessen werden welche elektromagnetischen Wellen der Prüfling selbst erzeugt. Die Kammer ist elektromagnetisch von der Außenwelt abgeschirmt, um einen Freiraum ohne störende, reflektierende Strahlung zu simulieren.
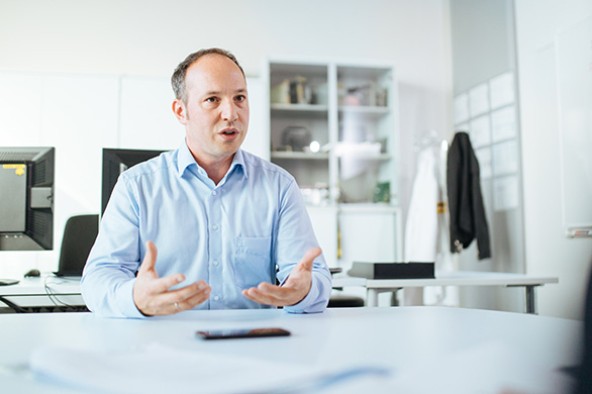
Wie laufen Testverfahren für externe Kunden ab?
Auch das ist sehr unterschiedlich. Wir haben Kunden, etwa aus der Automobilbranche, die die relevanten Normen selbst sehr gut kennen und nur einzelne Tests bei uns durchführen. Andere Kunden unterstützen wir hingegen beim gesamten Zulassungsprozess: von der Auswahl der korrekten Standards und Normen für ihr Produkt, über Tests während der Entwicklungsphase bis zu den finalen Tests vor Serienzulassung. Gerade die Wahl der korrekten Prüfprofile kann je nach Branche sehr anspruchsvoll sein.
Wir sind kein klassisches Prüflabor, sondern bündeln am Standort auch Wissen und Erfahrung in der Entwicklung von Elektronik. Wir verfügen etwa ein Inbetriebnahmelabor, in dem Baugruppen sowohl mechanisch als auch elektrisch bearbeitet werden können. Auf beides können wir zurückgreifen, etwa wenn unsere Kunden nach dem Prüfverfahren kleinere Veränderungen an ihrem Gerät vornehmen möchten. Zudem ist es manchmal schon hilfreich mit einem anderen Entwickler ein Problem zu besprechen, um eine einfache Lösung zu finden. Das ist bei uns möglich.
Beeinflussen aktuelle Megatrends wie Digitalisierung oder Elektromobilität auch die Arbeit im Test-Center?
Ja, natürlich wirken sich diese Entwicklungen auch auf uns aus. Im Rahmen der Digitalisierung ist vor allem das Thema der zunehmenden Vernetzung im Rahmen des Internet der Dinge (IoT) für uns relevant. Die Liebherr-Elektronik GmbH fertigt unter anderem Telematik-Produkte, die natürlich nach neusten Standards qualifiziert werden müssen.
Und auch Elektromobilität ist für uns ein relevantes Thema. Viele unserer Kunden aus dem Bodenseekreis sind in der Automobilbranche tätig. Hier geht es vor allem um Ansteuerelektronik für Batterien mit höherer Leistungsfähigkeit, die erst noch entwickelt und dann entsprechend getestet werden müssen. Aktuell können wir noch keine so großen Elektronikkomponenten an unserem Standort testen. Vor dem Hintergrund dieser Entwicklung werden wir aber eine mögliche Erweiterung des Test-Centers prüfen.