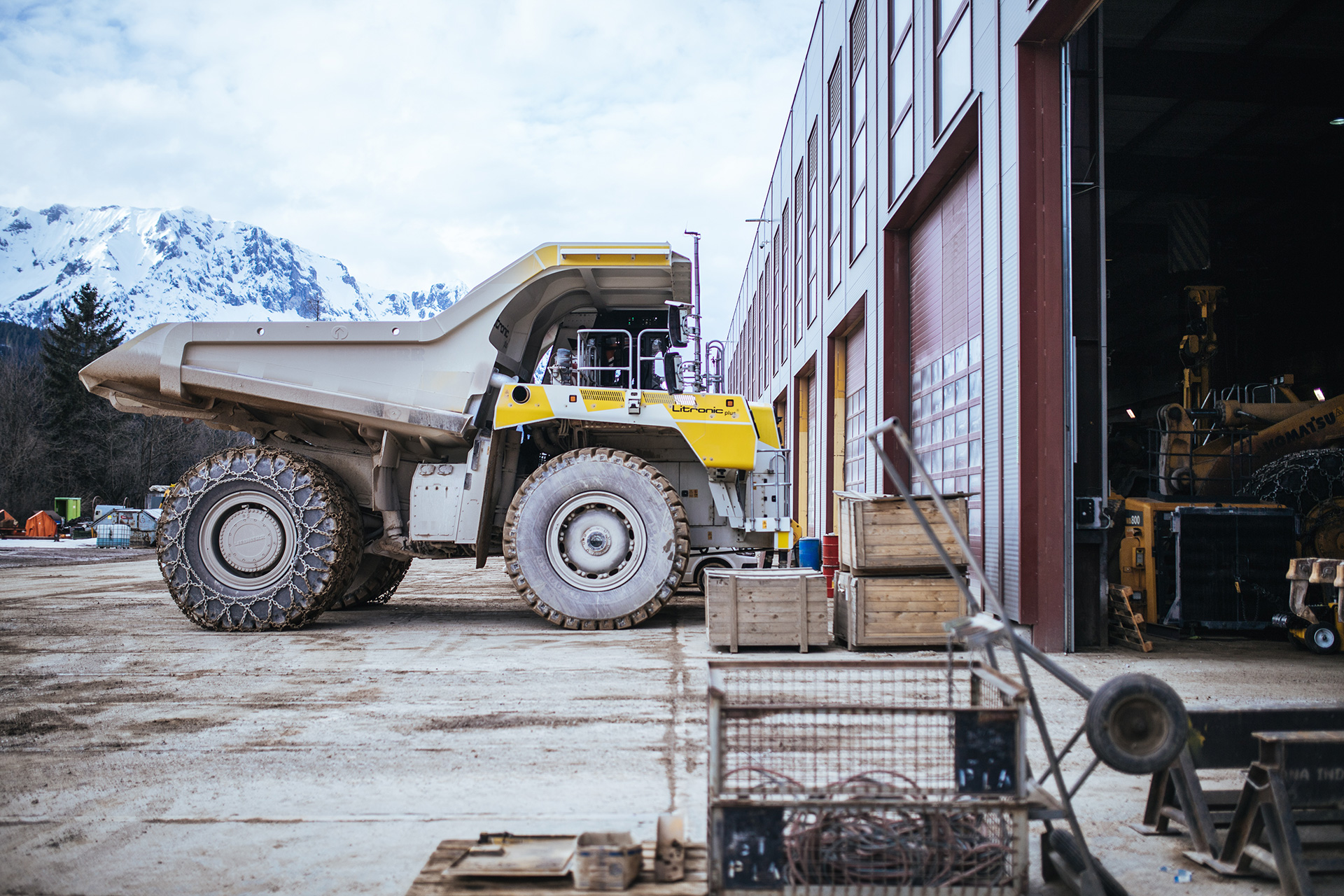
Klicken Sie auf VIDEO FREIGEBEN und folgen Sie den Datenschutzhinweisen.
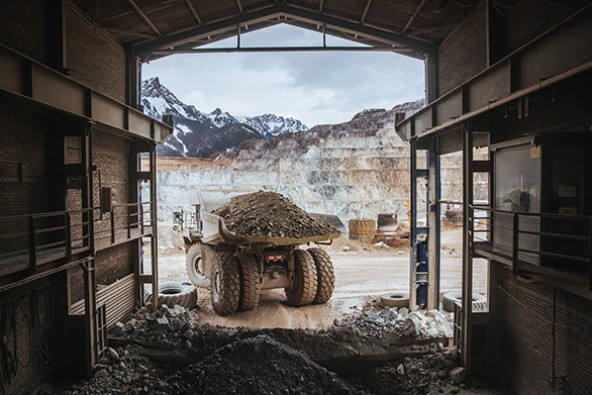
Mit einem Rumms in die Zukunft
„3 - 2 - 1: brenna tuat’s!“, knarzt es aus dem Walkie-Talkie und schon erzittert der Berg. In einer Staubwolke donnern 80.000 Tonnen Gestein herab. Wir sind am Erzberg in der Steiermark, der bedeutendsten Erzlagerstätte der Alpen. In dem größten und modernsten Tagebau Mitteleuropas wird seit mehr als 1.300 Jahren Eisenerz gewonnen.
Zweimal am Tag lässt es der Sprengmeister krachen, damit jedes Jahr 12 Millionen Tonnen des eisenreichen Siderit-Erzes zu drei Millionen Tonnen Feinerz verarbeitet werden können. Für 230 Bergleute der VA Erzberg GmbH heißt dies: alle Hände voll zu tun. In vier Schichten sind sie im Einsatz, rund um die Uhr, das ganze Jahr. Drei Radlader und neun Schwerlastkraftwagen sorgen dabei für den Materialtransport. Seit August letzten Jahres ist ein besonderer Truck hinzugekommen: der T 236 von Liebherr, ein 180 Tonnen-Kraftpaket mit 1.200 PS (895 kW), das für eine Last von bis zu 100 Tonnen ausgelegt ist.
Ich war sehr neugierig auf den dieselelektrischen Antrieb und auf Anhieb restlos begeistert von dem Drehmoment. Die Kraft ist sofort da. Ein tolles Gefühl.
Rund um die Uhr im Einsatz - das ganze Jahr
Am Steuer sitzt Gerhard Bayer. Seit 27 Jahren ist der Fahrer und Fahrertrainer am Erzberg mit unterschiedlichsten Schwerlastwagen unterwegs, kennt das Gelände und dessen Anforderungen an Fahrzeuge wie seine Westentasche. Mit seiner Erfahrung und seiner Fähigkeit, nicht nur in das Fahrzeug hineinzuspüren, sondern auch Auffälligkeiten im Betrieb in verständliche Worte fassen zu können, ist er ein geradezu idealer Testfahrer und kongenialer Partner für Laurent Fricker. Der Service-Techniker von Liebherr ist mit seinem Laptop immer mit an Bord, verbindet sich dann mit der komplexen Fahrzeug-Elektronik, misst und dokumentiert alle Maschinen- und Fahrdaten. Und davon gibt es reichlich.
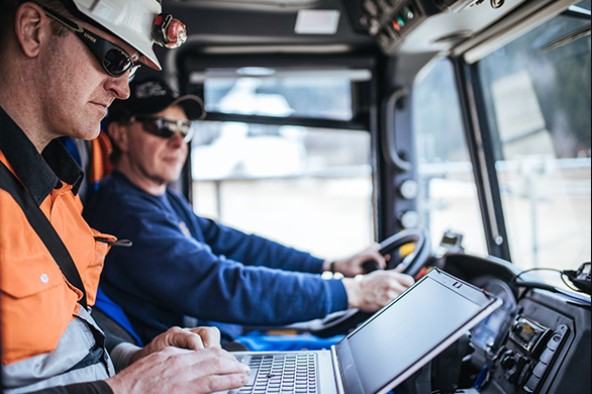
Bergwerk als Testlabor
„Der T 236 ist eine Weltneuheit. Noch nie zuvor war in dieser Fahrzeugklasse ein Truck mit dieselelektrischem Antrieb unterwegs“, sagt Fricker. Die Hinterachse des 100-Tonnen-Muldenkippers wird von einem Elektromotor angetrieben, dessen Generator seine Energie von einem Dieselmotor bezieht. „Jetzt muss sich das Konzept im Bergbaualltag unter extremen klimatischen Bedingungen beweisen“, erklärt Fricker. Jeder Tag Fahrpraxis mache dabei die innovative Technologie ein Stück besser. Nach der Schicht hat Fricker deswegen auch noch nicht Feierabend. An seinem Laptop wertet er die Fahrzeugdaten des Tages aus und schickt sie über eine Datenleitung nach Frankreich. In der Entwicklungsabteilung der Liebherr-Mining Equipment Colmar SAS werden sie schon sehnsüchtig erwartet.
Indem Sie auf „AKZEPTIEREN“ klicken, willigen Sie für dieses Video gemäß Art. 6 Abs. 1 lit. a DSGVO in die Datenübermittlung an Google ein. Wenn Sie künftig nicht mehr zu jedem YouTube-Video einzeln einwilligen und diese ohne diesen Blocker laden können möchten, können Sie zusätzlich „YouTube-Videos immer akzeptieren“ auswählen und damit auch für alle weiteren YouTube-Videos, welche Sie zukünftig auf unserer Website noch aufrufen werden, in die jeweils damit verbundenen Datenübermittlungen an Google einwilligen.
Erteilte Einwilligungen können Sie jederzeit mit Wirkung für die Zukunft widerrufen und damit die weitere Übermittlung Ihrer Daten verhindern, indem Sie den entsprechenden Dienst unter „Sonstige Dienste (optional)“ in den Einstellungen abwählen (später auch aufrufbar über die „Datenschutzeinstellungen“ in der Fußzeile unserer Website ).
. Weitere Informationen erhalten Sie in unserer Datenschutzerklärung sowie in der Google-Datenschutzerklärung.Datenschutzerklärung von Google.*Google Ireland Limited, Gordon House, Barrow Street, Dublin 4, Irland; Mutterunternehmen: Google LLC, 1600 Amphitheatre Parkway, Mountain View, CA 94043, USA** Hinweis: Die mit der Datenübermittlung an Google verbundene Datenübermittlung in die USA erfolgt auf Grundlage des Angemessenheitsbeschlusses der Europäischen Kommission vom 10. Juli 2023 (EU-U.S. Data Privacy Framework).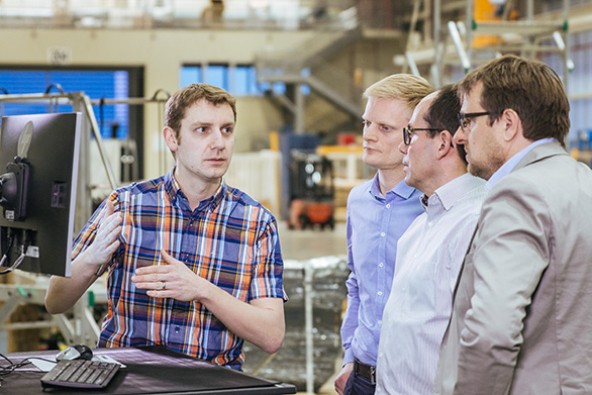
Das 100-Tonnen-Start-up
„Wir wollen einen Truck bauen. Das war Ende 2013 eine klare Ansage“, erinnert sich Dr. Burkhard Richthammer. Der Geschäftsführer Entwicklung und Konstruktion bei Liebherr-Mining Equipment Colmar hatte den Auftrag, ein vollkommen neues Fahrzeug in der mittleren Kategorie der Schwerlastkraftwagen zu entwickeln. Die am häufigsten verwendete Maschine in Bergwerken und großen Steinbrüchen fehlte bis dato im Mining-Angebot von Liebherr und sollte das Portfolio rund um die erfolgreichen Mining-Bagger und -Raupen für diesen Kundenkreis vervollständigen.
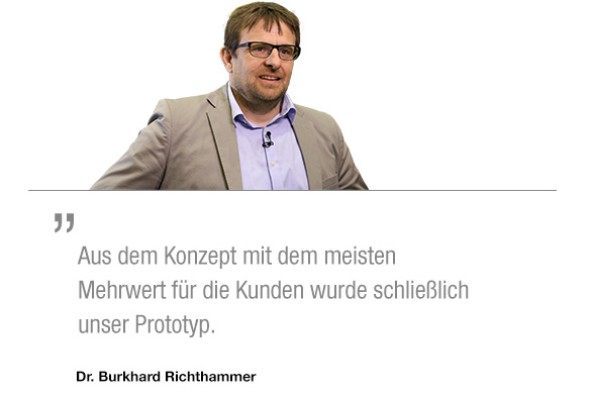
Erst mal zu den Kunden
„Anfangs war ich allein mit einem weißen Blatt Papier, einem Laptop und einem Telefon. Ich war ein Ein-Mann-Start-up“, berichtet Dr. Richthammer. Der erste Weg des gelernten Bergbauingenieurs, der im Vertrieb und Produktmanagement von Großbaggern zu Hause ist, habe zu den Kunden geführt um sie zu fragen, was sie wirklich richtig gut gebrauchen könnten.
Gleichzeitig formierte Dr. Richthammer ein kleines, feines Team aus Ingenieuren, Service- und Vertriebsleuten, die Hand in Hand mit bergbauerfahrenen Mining-Kollegen von Liebherr aus den USA, Südafrika und Australien zusammenarbeiteten. „Bei der Auslegung und dem Lastenmanagement des neuen Trucks sind so von Anfang an erfahrene Praktiker eingebunden gewesen. „Das Ziel: eine Entwicklung so nah wie möglich an den Bedürfnissen der Kunden“, so Dr. Richthammer.
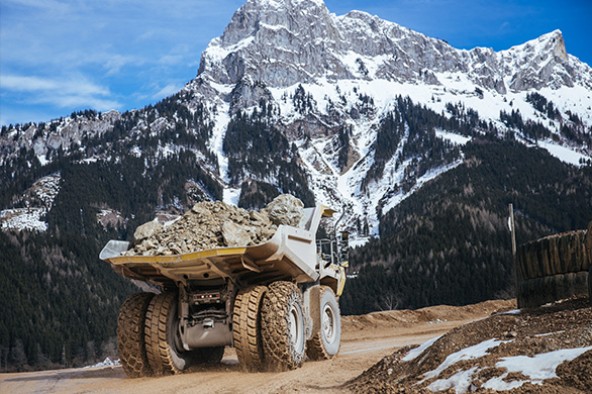
Einfach drauflosdenken
Für Kai Kugelstadt, den Technik-Leiter der Liebherr-Mannschaft, liegt im Start-up-Charakter der T 236-Entwicklung die besondere Herausforderung, aber auch der große Reiz der Aufgabe: „Wir hatten bei der Entwicklung dieses speziellen Mining-Truck-Typs nichts – es gab keinen Maßstab, kein Vorgängermodell, keine Produktionserfahrung – wir konnten einfach frei drauflosdenken, alles infrage stellen und ein neues, eigenes Konzept für diese Tonnagenklasse entwickeln. Und vor allem konnten wir dabei auf das komplette Produkt- und Leistungsportfolio von Liebherr zurückgreifen – insbesondere auf über zehn Jahre Erfahrungen rund um vertikal integrierte Elektroantriebstechnologien“, erklärt Kugelstadt.
Die Vorteile des nun realisierten neuen dieselelektrischen Antriebs dürften vor allem den Nutzern angenehm in den Ohren klingeln: konstante Kraftübertragung auf die Hinterachse – und das bei allen Fahrbedingungen - weniger Verschleiß, längere Lebensdauer, längere Wartungszyklen und damit günstigere Wartungskosten sowie eine bessere Gesamtkostenbilanz (Total Cost of Ownership, kurz TCO).
Indem Sie auf „AKZEPTIEREN“ klicken, willigen Sie für dieses Video gemäß Art. 6 Abs. 1 lit. a DSGVO in die Datenübermittlung an Google ein. Wenn Sie künftig nicht mehr zu jedem YouTube-Video einzeln einwilligen und diese ohne diesen Blocker laden können möchten, können Sie zusätzlich „YouTube-Videos immer akzeptieren“ auswählen und damit auch für alle weiteren YouTube-Videos, welche Sie zukünftig auf unserer Website noch aufrufen werden, in die jeweils damit verbundenen Datenübermittlungen an Google einwilligen.
Erteilte Einwilligungen können Sie jederzeit mit Wirkung für die Zukunft widerrufen und damit die weitere Übermittlung Ihrer Daten verhindern, indem Sie den entsprechenden Dienst unter „Sonstige Dienste (optional)“ in den Einstellungen abwählen (später auch aufrufbar über die „Datenschutzeinstellungen“ in der Fußzeile unserer Website ).
. Weitere Informationen erhalten Sie in unserer Datenschutzerklärung sowie in der Google-Datenschutzerklärung.Datenschutzerklärung von Google.*Google Ireland Limited, Gordon House, Barrow Street, Dublin 4, Irland; Mutterunternehmen: Google LLC, 1600 Amphitheatre Parkway, Mountain View, CA 94043, USA** Hinweis: Die mit der Datenübermittlung an Google verbundene Datenübermittlung in die USA erfolgt auf Grundlage des Angemessenheitsbeschlusses der Europäischen Kommission vom 10. Juli 2023 (EU-U.S. Data Privacy Framework).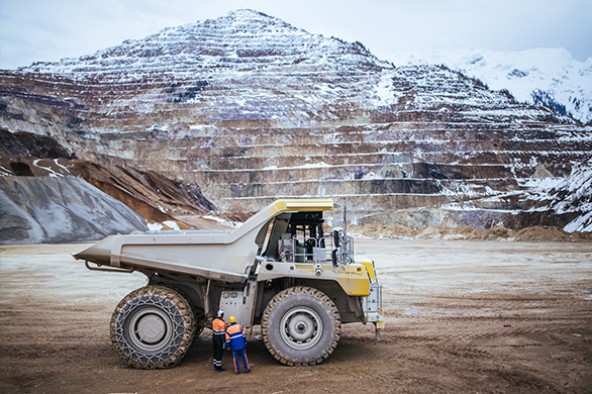
Unter härtesten Bedingungen
„Der T 236 ist auf ein Maximum an Leistung auch unter den härtesten Einsatzbedingungen ausgelegt“, betont Dr. Burkhard Richthammer. Der auf ein Jahr angelegte Test im Praxiseinsatz am Erzberg diene nun der finalen Feinabstimmung des Fahrzeugs, bevor es 2019 in Serienproduktion gehe. „Das ist bestes Live-Engineering gemeinsam mit unseren Kunden. Daraus ergeben sich immer weitere neue Perspektiven.“
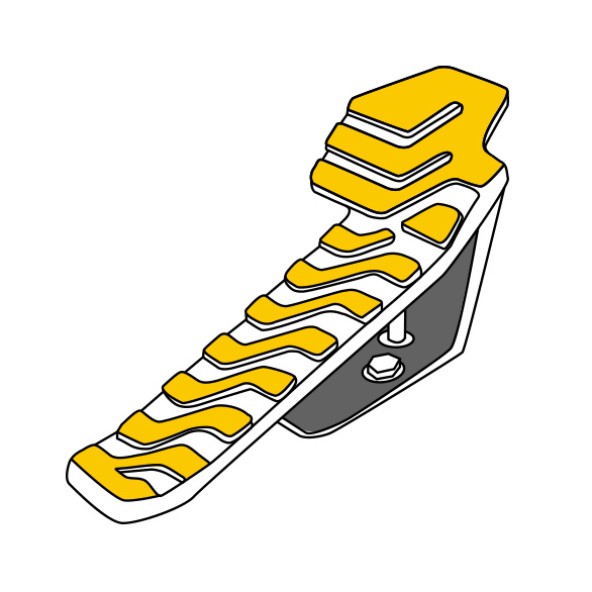
Technik-Know-how: dieselelektrischer Antrieb
Wenn sich am Berganstieg die Neigung ändert, müssen mechanisch angetriebene Schwerlastkraftwagen schalten. Bei diesem Lastwechsel wirken hohe Kräfte auf die Antriebsräder. Auf Schotterstrecken sind dann oft ruckelige Unebenheiten, sogenannte Schalthügel, die Folge, die eine gleichmäßige Auffahrt dann zusätzlich erschweren und den Treibstoffverbrauch in die Höhe treiben.
Auf Basis der von Liebherr entwickelten Litronic Plus Generation 2 kommt der dieselelektrische Antrieb des T 236 ohne Schaltvorgänge aus und zieht bei konstanter Drehzahl seine Last aufwärts.
Das Antriebskonzept im Detail

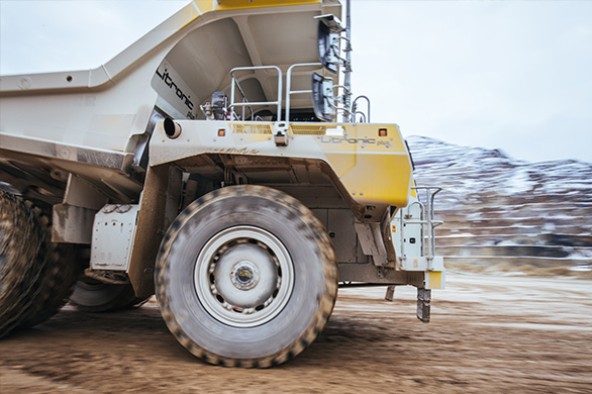
Hohes Anfahrtsdrehmoment
Bei den Testfahrten am Erzberg überzeugte der T 236 die Testfahrer durch das hohe Anfahrtsdrehmoment und eine gute kontinuierliche Leistungsübertragung. Der Truck erweist sich damit als unempfindlich hinsichtlich der Fahrgeschwindigkeit bei Steigungs- und Nutzlastschwankungen.
Bei Bremsvorgängen „stützt“ sich der Truck auf dem Elektromotor ab. Der Generator wird bei der Active-Front-Technologie im Verzögerungsmodus als Motor benutzt, um den Verbrennungsmotor anzutreiben. Das Antriebssystem arbeitet dann mit einer kontrollierten Motordrehzahl nahezu ohne Kraftstoffverbrauch und kann niemals überdrehen. Ölgekühlte Lammellenbremsen erlauben zudem ein gleichzeitiges, besonders zuverlässiges und kontinuierliches Verzögern mit der Vorder- und Hinterachse.
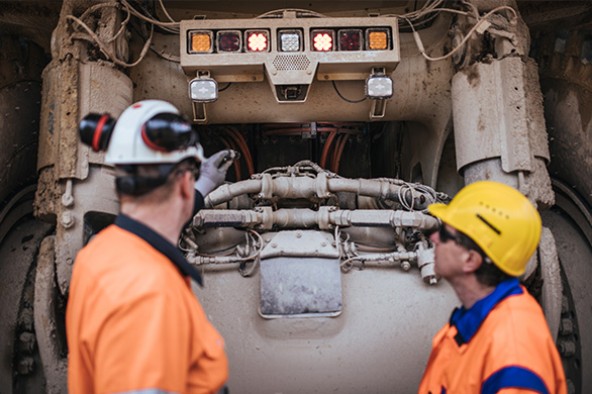
Wartungsfreundliches Konzept
Der dieselelektrische Antrieb arbeitet mit einer Niederspannung von 690 VAC (Wechselstrom) und 900 VDC (Gleichstrom). Dies ermöglicht es auch regulären Technikern ohne spezielle Starkstrom-Qualifikationen vor Ort Systemwartungen durchzuführen. Das erhöht die Arbeitsplatzsicherheit und spart Wartungskosten.
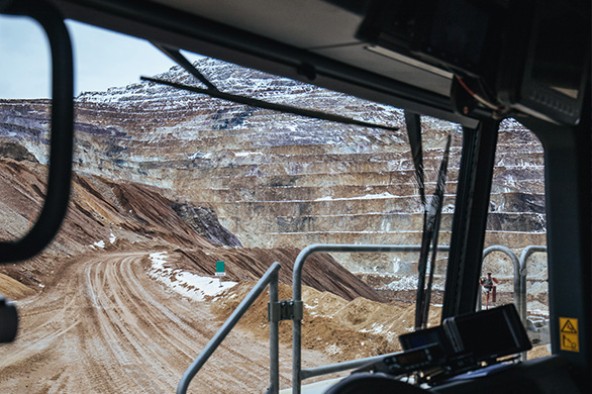
Vollgas im Idealbereich
Sechs Kilometer steil bergauf. Die Fahrt auf der Rampe in den „Sturz“, wo das nichtverwertbare „taube“ Material abgekippt wird, verlangt den vollbeladenen Trucks alles ab. Für Gerhard Bayer und seinen Co-Piloten Laurent Fricker heißt dies zehn bis 12 Minuten Vollgas. Alle Systeme auf Maximum. Wo die konventionellen dieselmechanischen Schwerlaster immer wieder schalten müssen und die Drehzahl des Motors rauf und runter schnellt, zieht der T 236 gleichmäßig durch. „Ich kann die ganze Strecke am idealen Drehzahlpunkt um die 1.800 Umdrehungen fahren. Da ruckt und rumpelt nichts, da gibt es kein Aufheulen des Motors, es fährt sich einfach vollkommen komfortabel“, freut sich Gerhard Bayer.
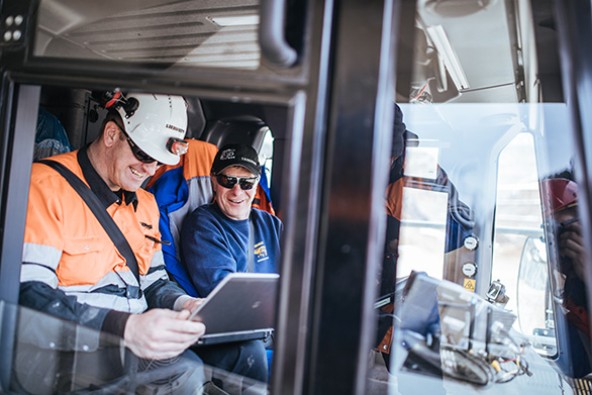
Alles im Visier
Mit der neuen Maschine alle anfallenden Transportarbeiten des Erzbergalltags zu übernehmen, gefällt Gerhard Bayer. Aber mindestens genauso gefällt ihm seine Rolle als Testfahrer. „Mit Laurent nehme ich alles ins Visier: nicht nur den Antrieb, sondern auch die Kabine und ihre Ausstattung bis hin zum Federungskonzept. Gemeinsam arbeiten wir mit den Entwicklern in Colmar daran, den T 236 immer wieder ein bisschen besser zu machen.“ Jedes Mal wenn Laurent Fricker eine neue Software aus Colmar aufspiele, ändere sich das Fahrverhalten. „Das ist immer sehr spannend“, sagt Bayer.
Aufmerksam verfolgt auch Josef Pappenreiter die Fortschritte bei der Mining-Truck-Entwicklung. Der Geschäftsführer Technik der VA Erzberg GmbH verbindet mit dem dieselelektrischen Antrieb große Erwartungen an das Leistungsvermögen, die Effizienz und die Wirtschaftlichkeit solcher Mining-Fahrzeugkonzepte. „Im Bergbau ist eine gute Performance und eine problemlose Verfügbarkeit der Transportmittel ein wesentlicher Erfolgsfaktor im Wettbewerb. Wir wollen deshalb bei der Technologie immer ganz vorne dabei sein“, sagt Pappenreiter.
Indem Sie auf „AKZEPTIEREN“ klicken, willigen Sie für dieses Video gemäß Art. 6 Abs. 1 lit. a DSGVO in die Datenübermittlung an Google ein. Wenn Sie künftig nicht mehr zu jedem YouTube-Video einzeln einwilligen und diese ohne diesen Blocker laden können möchten, können Sie zusätzlich „YouTube-Videos immer akzeptieren“ auswählen und damit auch für alle weiteren YouTube-Videos, welche Sie zukünftig auf unserer Website noch aufrufen werden, in die jeweils damit verbundenen Datenübermittlungen an Google einwilligen.
Erteilte Einwilligungen können Sie jederzeit mit Wirkung für die Zukunft widerrufen und damit die weitere Übermittlung Ihrer Daten verhindern, indem Sie den entsprechenden Dienst unter „Sonstige Dienste (optional)“ in den Einstellungen abwählen (später auch aufrufbar über die „Datenschutzeinstellungen“ in der Fußzeile unserer Website ).
. Weitere Informationen erhalten Sie in unserer Datenschutzerklärung sowie in der Google-Datenschutzerklärung.Datenschutzerklärung von Google.*Google Ireland Limited, Gordon House, Barrow Street, Dublin 4, Irland; Mutterunternehmen: Google LLC, 1600 Amphitheatre Parkway, Mountain View, CA 94043, USA** Hinweis: Die mit der Datenübermittlung an Google verbundene Datenübermittlung in die USA erfolgt auf Grundlage des Angemessenheitsbeschlusses der Europäischen Kommission vom 10. Juli 2023 (EU-U.S. Data Privacy Framework).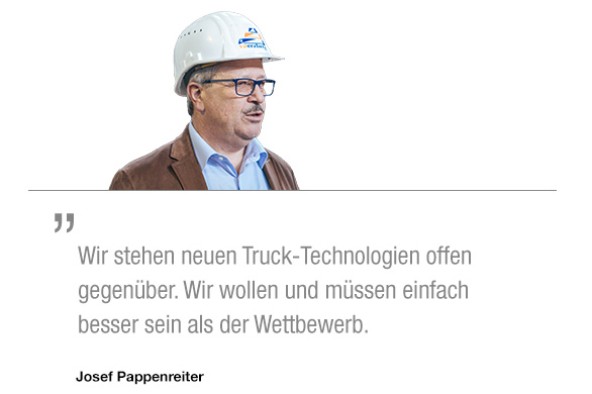
Immer weiter forschen
Deshalb habe man gemeinsam mit Liebherr bei den dieselelektrischen Antrieben in der 100-Tonnen-Klasse auch gerne technologisches Neuland betreten. Von dort soll es aber für die VA Erzberg GmbH noch weitergehen. „Wir sind bereits dabei, gemeinsam mit Liebherr die Elektrifizierung der Antriebe weiterzudenken“, kündigt Pappenreiter an. „Schon jetzt zeigt sich: Dieser Weg lohnt sich. Die Leistung der Fahrzeuge steigt, die Kosten bei der Energie und der Instandhaltung sinken und die Umwelt wird geschont. Das nenne ich im besten Sinne Win-win.“