Im Gespräch mit Stefan Jehle, Vertriebsleiter Automationssysteme: Faszination E-Mobilität
Seit über 30 Jahren ist Stefan Jehle bereits Teil der Liebherr-Verzahntechnik GmbH. Er bringt viel Erfahrung im Bereich Engineering und Planung für Automationssysteme und Fertigungsanlagen mit. Nach langjähriger Arbeit als Gebietsverkaufsleiter, übernahm er 2013 die Leitung des Vertriebs für Automationssysteme. Im Rahmen der Mobilitätswende darf er sich jetzt einer neuen Herausforderung stellen: der E-Mobilität.
Was ihm daran besondere Freude bereitet, warum sich Liebherr auf die Montage von Batteriepacks spezialisiert hat und was die Zukunft bringen wird, haben wir im Interview erfahren.
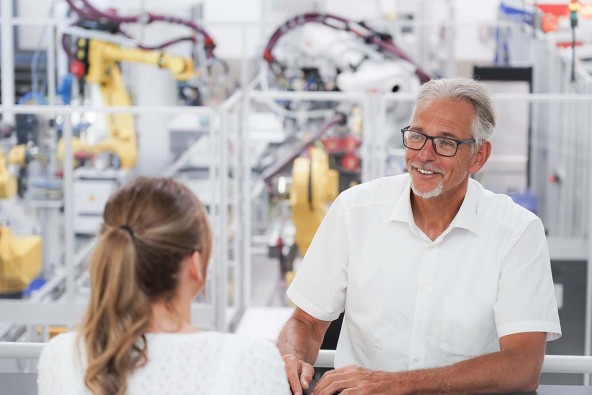
Herr Jehle, Sie haben sich viele Jahre der Automatisierung der Fertigung des Verbrennungsmotors gewidmet. Nun bringt der Umschwung zur E-Mobilität viele Veränderungen mit sich. Wie gehen Sie damit um?
Für mich ist das ganz einfach: Man kann es drehen und wenden wie man will, aber das Thema E-Mobilität ist gesetzt. Das ist keine Wette mehr. Es ist egal, was die persönliche Meinung zu dem Thema ist, oder was für alternative Antriebe in Zukunft noch kommen mögen. Die Weichen sind politisch und wirtschaftlich gestellt und man muss sich auf die Technologie einlassen. Ansonsten lässt man sich große Chancen in einem Milliardenmarkt entgehen.
Was waren also für Liebherr die ersten Schritte in die Welt des elektrischen Motors? Inwieweit können Sie bei der Produktion von Elektroantrieben auf die Erfahrung in der Großserienfertigung vom Verbrenner zurückgreifen und was sind komplett neue Herausforderungen?
Wir beobachten das Thema natürlich schon lange. Vor etwa fünf Jahren haben wir dann in wissenschaftlicher Begleitung und mit der Hilfe von Beratungsunternehmen ein Entwicklungsprojekt gestartet. Wir haben alle Bereiche der E-Mobilität durchleuchtet und diese an unserer Erfahrung, unseren bestehenden Produkten und Möglichkeiten gespiegelt. Wir kamen zu dem Schluss, dass wir die größten Parallelen in der Batteriepackmontage sehen. So ein Pack kann bis zu 1000 kg wiegen. Davon verstehen wir was – wir haben Erfahrung mit dem Transport von schweren Teilen, z.B. aus der LKW-Motorblockfertigung. Alles, was mit Transport und Speichern zu tun hat, konnten wir aus dem bestehenden Portfolio übernehmen: Transportsysteme, Bänder, Ladeportale und Palettenhandhabungssysteme.
Was noch fehlte, waren die Montagetechnologien: Schrauben, Kleben, Fügen und elektrische Messungen. Unser Tech-Center bietet hier den perfekten Raum für unsere Entwicklungsabteilung, um sich mit den neuen Tätigkeitsfeldern zu befassen. An unserer Test- und Versuchsanlage können sich auch unsere Kunden vor Ort von unseren Systemen überzeugen.
Automatisiertes Stecken von Modulverbindern
Steckverbindungen für das elektrische Kontaktieren der Module im Batteriepack konnten bislang nur manuell montiert werden. Zusammen mit KOSTAL Kontakt Systeme GmbH hat Liebherr als erster Hersteller einen Stecker entwickelt, den man automatisch stecken kann. Mehr Informationen finden Sie in diesem Artikel.
Wie kann man sich so eine Montagelinie für Batteriepacks vorstellen?
Die Batterie besteht aus einer Zelle, welche zu einem Modul montiert wird. Ein Modul hat in etwa die Größe einer Autobatterie. Die Module müssen daraufhin in einem sogenannten Pack zusammengefügt werden. In einer Batteriewanne können zwischen 10 und 40 Module montiert werden. Nachdem die Module angeliefert werden, folgen in unserer Linie mehrere Schritte:
- Wärmeleitpaste für die Kühlung der Batterie auftragen
- Installation des Moduls (greifen und verschrauben in der Wanne)
- Elektrisches Kontaktieren der Module
- Deckel verschrauben und kleben
- Dichtheitsprüfungen / End-of-Line Prüfung (EoL)
- Weiterer Transport an Montagestationen bzw. zum Versand
Es gibt noch einen besonderen Prozess – statt Modul ins Pack, gibt es auch „Cell-to-pack“. Hier wird die Zelle direkt ins Pack eingebaut. Man spart sich den Zwischenschritt des Moduls. Für das Verbinden der Zellen haben wir uns einen Partner mit ins Boot geholt: der Sondermaschinenbauer Jonas & Redmann ist Spezialist auf dem Gebiet Zelle und Pack. Mit dem gebündelten Know-how beider Unternehmen, sind wir ein zuverlässiger Partner für Kunden im Bereich Cell-to-pack.
Welche Herausforderungen begegnen Ihnen in Gesprächen mit Ihren Kunden in der Batteriepackmontage und wie gehen Sie damit um?
Zum einen sind das natürlich technische Fragen, die wir mit jedem Kunden klären müssen. Was muss manuell gemacht werden? Wo ergibt Automation Sinn? Das muss für jeden Prozess überlegt werden. Hier gibt es vielfältige Themen, die unsere Kunden beschäftigen. Wir müssen immer für alle Technologien einer Montagelinie gut vorbereitet sein, um dem Kunden eine erstklassige fachliche Beratung leisten zu können.
Ein anderes Thema und eine große Challenge ist unser Einstieg in den relativ neuen Bereich. Beim Verbrenner können wir auf eine lange Liste von Projekten, die wir bereits realisiert haben, zurückgreifen. Bei Montagelinien für Batteriepacks ist das schon etwas schwieriger. Hier spielt unser Tech-Center eine wichtige Rolle. Wenn unsere Kunden uns vor Ort besuchen, können wir unsere Technologie live präsentieren und überzeugen: wir wissen, von was wir sprechen. Durch die Größe unserer Firma können wir natürlich auch die Manpower vorweisen, der es bedarf, um große Montagelinien umzusetzen.
Was ist Ihr persönliches Highlight bei Ihrer bisherigen Arbeit in der E-Mobilität?
Mich als Ingenieur reizt besonders die neue technische Herausforderung. Jede Batterie sieht anders aus. Es gibt kein Patentrezept, wie man eine Batterie zusammenbaut. Man muss den Prozess in jedem Projekt technologisch durchleuchten und den jeweils richtigen Montageschritt auswählen. Natürlich versuchen wir auf standardisierte Baugruppen zurückzugreifen, aus denen wir dann den individuellen Anwendungsfall maßgeschneidert für unsere Kunden zusammensetzen. Aber jedes Projekt ist anders und wir lernen mit jedem etwas Neues dazu.
Wie gefällt es Ihnen, bei Liebherr an diesem Technologiewandel mitzuarbeiten?
Durch unsere Firmenstruktur haben wir kurze Entscheidungswege. Das ist besonders wichtig, wenn man in ein neues Feld einsteigt. Wenn es hier lange dauern würde, bis Entscheidungen getroffen werden können, würde das Produkt nicht ins Rollen kommen. Dank der Größe unseres Konzerns haben wir überhaupt die Möglichkeit und den Atem, Projekte in diesen Dimensionen anzugehen. Unter anderen Umständen hätte man hier sicherlich weniger Spielraum.
Für mich persönlich ist das toll: Ich war 30 Jahre mit dem Verbrenner beschäftigt und habe jetzt noch mal die Möglichkeit bekommen, mich einem neuen Thema und Herausforderung zu stellen.
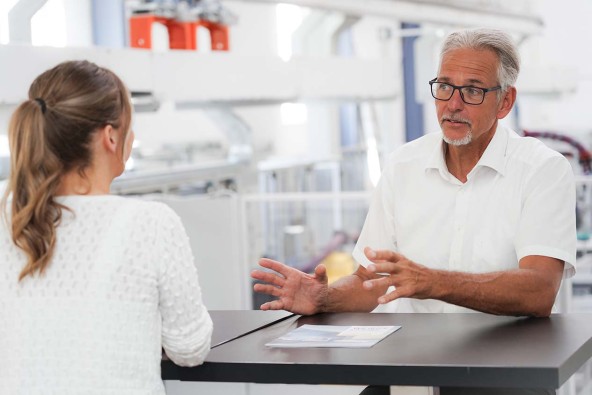
Können Sie uns noch einen kurzen Blick in die Zukunft der Mobilität gewähren?
Wie schon anfangs erwähnt, das Thema E-Mobilität ist gekommen, um zu bleiben. Dennoch denke ich, in Zukunft wird die Welt sehr viel diverser sein. Sie wird nicht wie jetzt nur aus einem Verbrennungsmotor bestehen. Wir werden eine Vielfalt an Antrieben sehen: Elektro mit Batterie, Brennstoffzellen, Wasserstoff.
Wir denken auch schon über die Herstellung der Batterie hinaus: Im Rahmen eines Forschungsprojekts beschäftigen wir uns aktuell, in Zusammenarbeit mit Instituten, auch mit dem Recycling. Man untersucht wie man die Batterie am besten recycelt, um möglichst viel von den Rohstoffen wieder beziehen zu können. Das ist auch ein spannendes Zukunftsthema im Bereich der Automation.