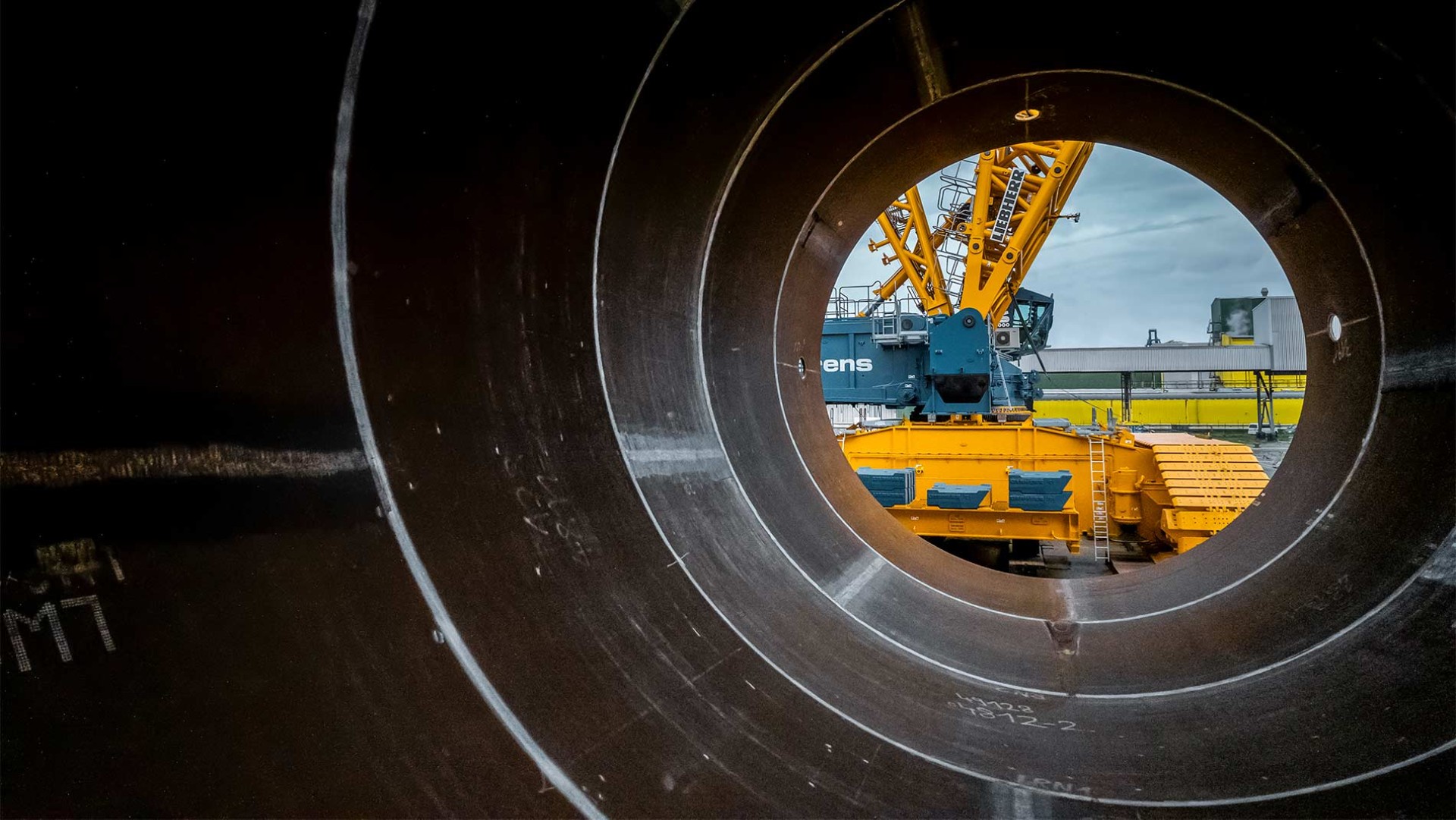
9 minutes - magazine 02 | 2023
Big pipe
To drive forward the energy transition, huge wind turbines are needed at sea to harvest powerful sea winds and supply green electricity for the mainland. The dimensions of modern offshore wind turbines are now enormous. So are the challenges for handling their gigantic components.
Début for the LR 12500-1.0
A Liebherr LR 12500-1.0 crawler crane has recently been doing a job in the port of Rostock that makes this very clear. In its first deployment, the crane with a completely new design lifts foundation pillars measuring almost 90 metres into the water. It is supported in handling these 1,360 tonne monopiles by a Liebherr LR 1800-1.0 crawler crane.
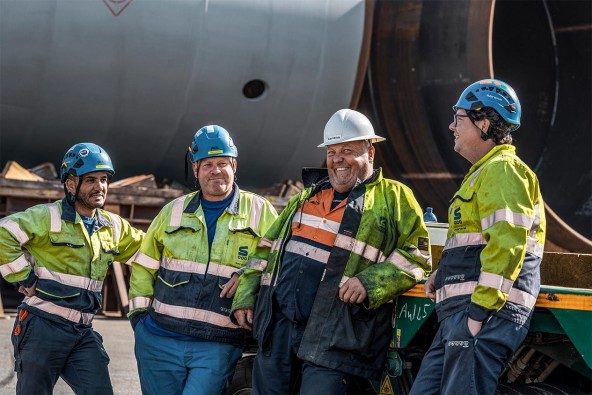
Relaxed, the Sarens team waits for the next monopile to be put into the water. From right to left: Willem Ditmer, who is in charge of the crane deployment in Rostock, Fred Kloek, Thierry de Cree, and Rachid Al Houss.
Around 30 kilometres north-east of Rügen, a German island in the Baltic Sea, Dutch company Van Oord is currently building the foundations for the “Baltic Eagle” offshore wind farm. Van Oord is a specialist in constructing offshore wind farms. 50 wind turbines with a total capacity of 476 megawatts are to supply electricity for 475,000 households from the end of 2024, according to the operator Iberdrola, a Spanish energy provider. But thereʼs still a lot of hard work to do before that can happen. At sea and on land. Two of our state-of-the-art crawler cranes are operating at full power during port handling on the Baltic coast. This large-scale deployment is also the première of our brand new LR 12500-1.0.
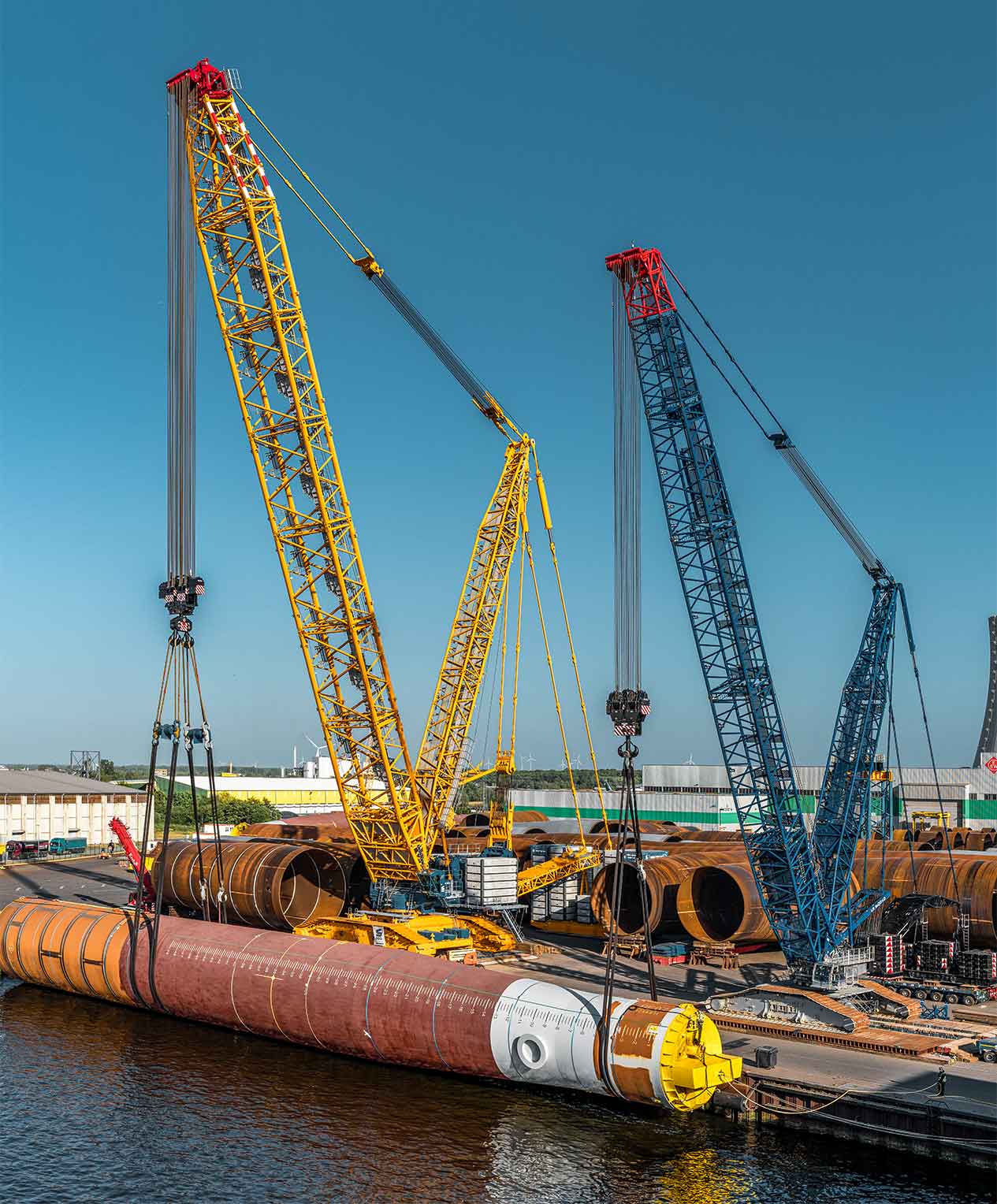
The innovative slewing platform design of the LR 12500-1.0 with its 7.5 metre wide HighPerformanceBoom.
If you travel to the industrial port of the coastal city of Rostock, it is easy to locate the area with the two large crawler cranes. The coloured lattice booms of the two machines rise steeply into the sky and point the way. Orientation becomes much more difficult when in the actual port area. The view is obscured by steel pipes as high as houses, stacked close together. You have to bend your knees a bit to spot the bright yellow crawler carriers of the LR 12500-1.0 underneath the jacked-up cylinders and determine your way forward. When you stand in front of the towering machine, your gaze inevitably wanders to the impressively wide lattice boom. This 7.5 metre wide HighPerformanceBoom and its unusual mounting on the slewing platform immediately catch the eye.
Less than 500 metres from the cranes, in the direct vicinity of the “Rostock Port”, is where the piles are being manufactured. These will be driven into the seabed at sea and will later support the offshore turbines. The monopiles float on their way to the construction site in the sea. They will be towed by a tug over a distance of 85 nautical miles to the “Baltic Eagle” construction site. Our cranes are ready at the port basin to place the pipes in the water beforehand.
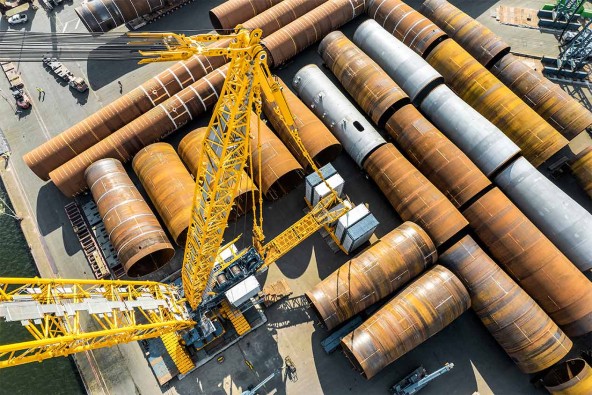
The crawler crane had to be set up in the middle of many steel pipes in Rostock port.
This job is being executed by the Belgian heavy lifting giant Sarens group. The Belgians, active in over 70 countries, specialise in crane rental, heavy lifting and engineered transport of some of the heaviest loads worldwide. Sarens had the first LR 12500-1.0 delivered directly to Rostock from the factory in Ehingen. “With the support of Liebherrʼs fitters, we finished assembling our new crawler crane here after three weeks,” says Willem Dittmer, project manager for Sarens, who is spearheading the challenging operation. “And this despite the fact that we had to set up the crane quite awkwardly between the pipes stored here.” A lot of effort was made to protect the subsoil. A plateau over one metre high supports the 2,500 tonne crane. On a thick layer of sand, Bongossi timbers and load distribution plates form the base for the massive crawler carriers.
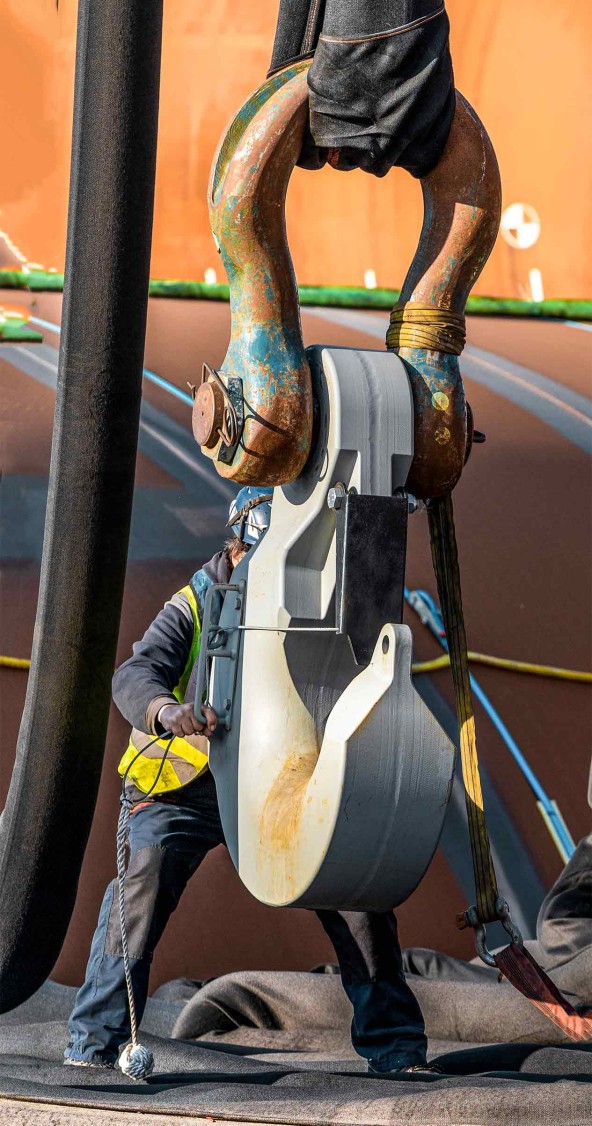
Impressing dimensions
“Giant strength with less dead weight”
The completely redesigned structure of the crawler crane with its wide lattice boom, which transfers the forces into the slewing platform with considerable stability, impresses the knowledgeable project manager after the first smoothly completed lifts. The transport and set-up time also received a positive response. “The completely new transport solutions of the LR 12500-1.0 with the folding mechanism of the lattice type sections and the split slewing platform are simply fantastic. We have fewer transport units and are faster in setting up the crane,” Dittmer says. “And it has giant strength with less dead weight. Unbelievable.”
These huge forces are then called upon when the nine metre thick monopiles are lifted into the port basin. Together with an LR 1800-1.0 from the crane rental company MAXIKraft, a gross load of almost 1,600 tonnes has to be moved. At a distance of about 50 metres, the two innovative models from the Ehingen-based crawler crane production stand next to each other, ready to lift. This direct comparison underlines the dimensions of the LR 12500-1.0 with its massive boom and the hook block with the double hook for holding the hoists. On a side note, this specimen alone – which was probably the most photographed specimen at the last Bauma trade fair in Munich – has an impressive dead weight of 70 tonnes. These two hooks carry the lionʼs share of the load during the hoists of the monopiles. The LR 12500-1.0 has to handle a gross weight of 1,245 tonnes. 350 tonnes remain for the smaller crawler crane, which acts as a kind of support leg in the tandem lift. Only the LR 1800-1.0 can also perform swivel movements, should such movements be necessary.
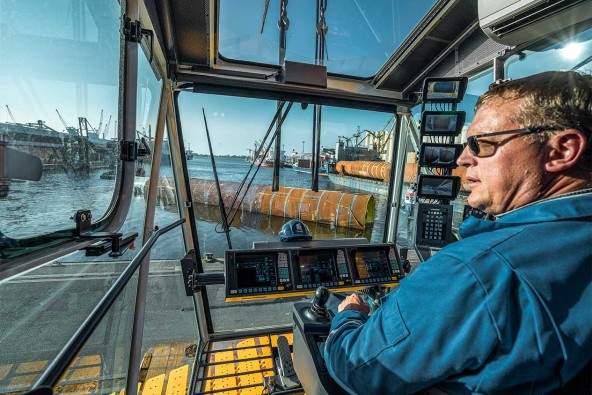
Robert Pawlowski looks out of his cabin at the floating monopile after his work is done.
“Iʼm happy with the crane.”
In his huge cabin on the LR 12500-1.0, Robert Pawlowski waits and checks the displays on the numerous monitors again. He and his powerful machine are ready to go. At a height of seven metres, the crane driver has the best possible view of the action. “Working with this modern crawler crane makes me really happy,” he remarks enthusiastically. “The perfect lighting and the many cameras do of course provide valuable support for us crane drivers. The numerous ladders and platforms enable us to work and set up easily and safely. I think the ergonomics of the crane are very well thought out. One truly impressive aspect is the completely new transport and assembly solution for the lattice boom sections. As is the incredible rigidity and stability of the boom.”
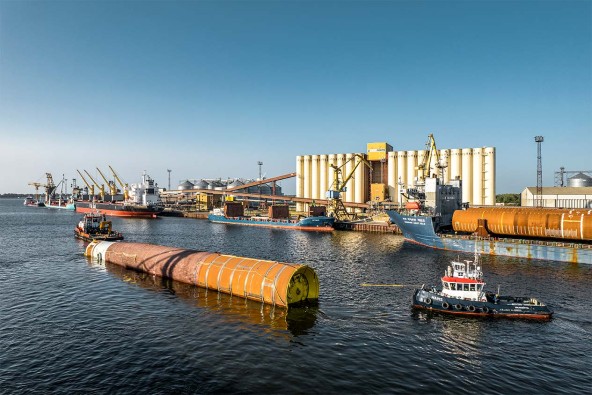
So here we go. A tug tows the floating monopile into the Baltic Sea. The 85 nautical mile journey to the offshore construction site takes 15 hours.
Suddenly the man in the cabin chair pauses. He concentrates on what is happening on the ground. The next monopile is being moved directly in front of the two cranes on 30 double axle lines with SPMT modules. A team of six specialists is already waiting with gigantic-looking slings. Thick, sheathed steel cables. Man-sized shackles. Everythingʼs a bit more powerful than usual. Pawlowski lowers the huge hook block so that the team can start their work. After a little more than an hour, everything is in place and the load is securely attached. Robert Pawlowski and his colleague in the crane next door receive the lift command via the radio.
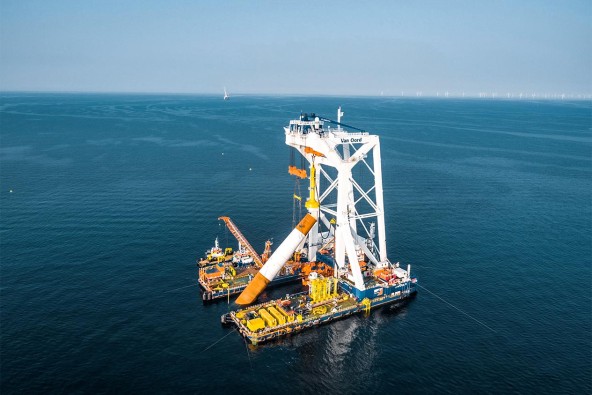
The Heavy Lift Vessel “Svanen” places the giant pile in a vertical position and piles it into the seabed. © Van Oord
After the load is picked up, things move unexpectedly quickly. The heavy-duty modules under the monopile are steered out of the danger zone and the cranes begin to tilt their lattice booms – barely visible. This process of increasing the radius and then setting the huge pipe into the deep port basin is a matter of just a few minutes. The crawler cranes increase their distance from their common load by twelve metres before the steel pile, which is closed at its ends, is lowered and placed in the water. A waiting tug takes over from there and gently pulls the floating pile into driving position. The sea voyage to the “Baltic Eagle” offshore wind farm can begin.
This article was published in the UpLoad magazine 02 | 2023.