Continuous improvement
Our customer-oriented approach enables us to pair experience and innovation in the development process. Our specialists rely on millions of hours of real-life data coming from our machines working in all type of environments and often most extreme conditions of temperature, humidity and altitude, to develop equipment that is efficient, reliable, and easy to operate and maintain.
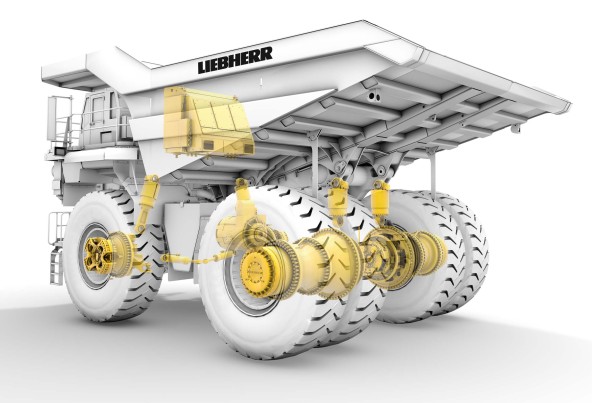
We develop new technologies inhouse to optimize our equipment.
Vertical integration
In house design and manufacturing of our components which are important for safety, performance and reliability.
We continuously develop our equipment to increase its performance, facilitate its maintenance and lower our customers’ operating costs.
Smarter equipment through data
Along with creating bigger, faster, stronger machinery, Liebherr is focused on making equipment smarter. Direct feedback from customers, and data returned from the machines themselves is a constantly updated information pool, with data coming from all over the world.
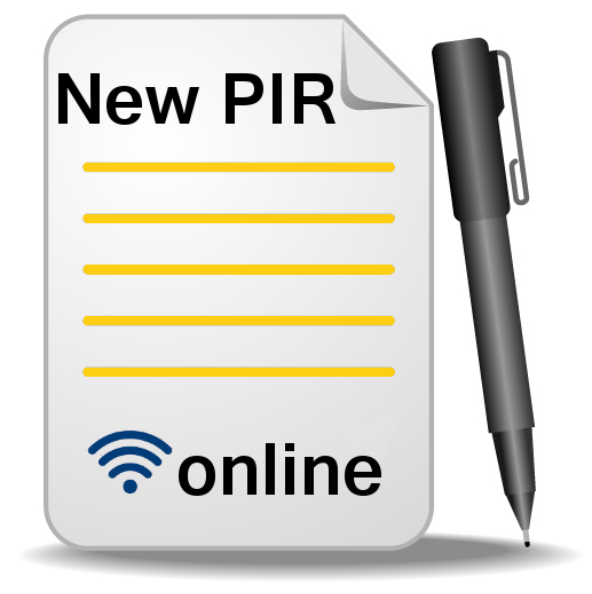
A systematic data collection and analysis process, directly connected to Liebherr mining factories with our customer support and engineering teams dedicated to continuous product improvement. Improvements flow into machine’s series and are proposed as upgrades for machines in operation.
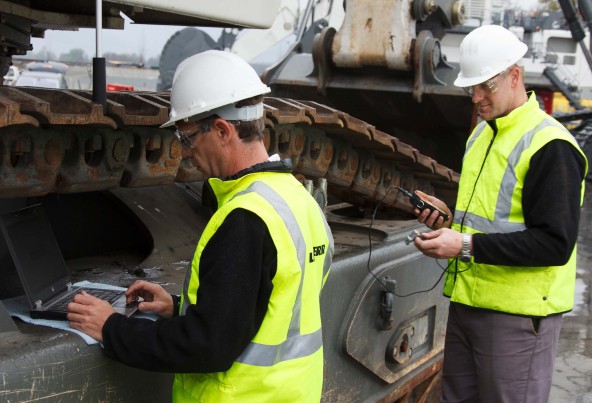
Worldwide machines’ real-life information is available through our interconnected data bases, and are analyzed by our reliability team to assess components’ lifetime and systems’ reliability. Feedback is a direct input to engineering and quality to the continuous product improvement. Information is also used to offer maintenance cost guarantees and availability guarantees in the frame of our Liebherr full Maintenance And Repair Contracts (MARC).
Our affiliates work with a powerful CMMS tool to record all necessary information about machines to better support our Customers. This constitutes a substantial database, and allows :
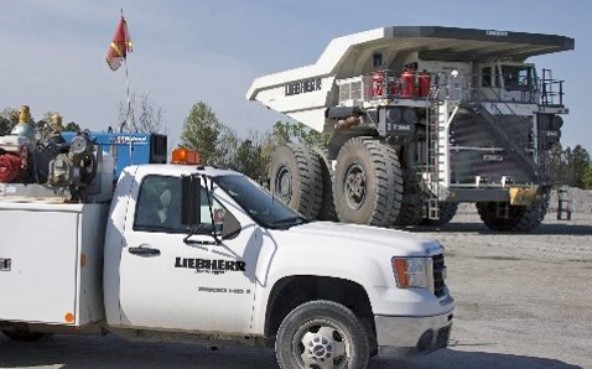
Technical analysis
- Downtime tracking
- Component history
- Equipment history
- Technical data
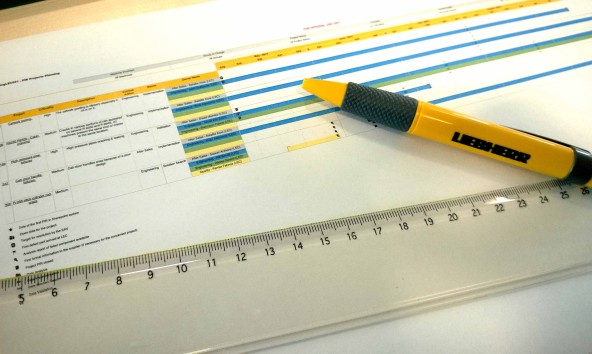
Graphical planning tools
- Equipment scheduler
- Work planning
- Parts forecast
- Component monitoring & failure analysis
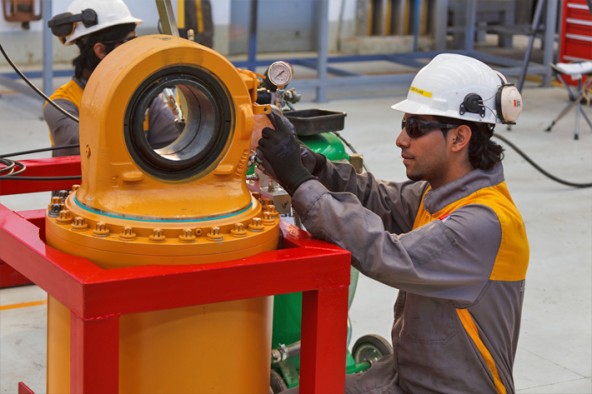
Decision tools
- Cost controlling
- Warranty management
- Work order processing
- Component rebuild management