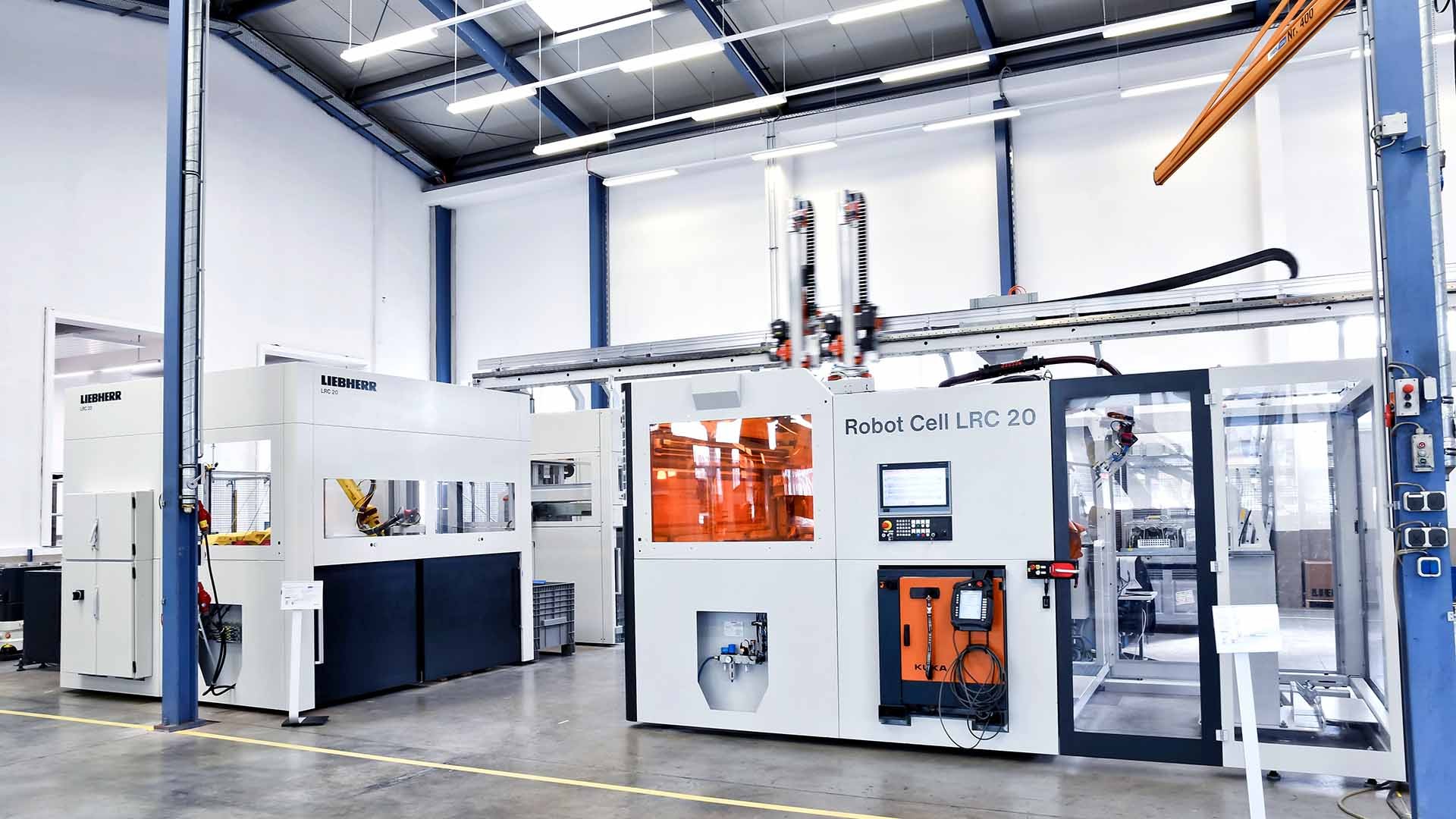
Showroom for the automation of tomorrow
The Kempten Tech Center of Liebherr Automation Systems provides a space for trials on high-quality automation solutions. The current focus is on vision-based robotics, bin picking, and processes in battery pack assembly for e-mobility. The Tech Center is a pillar of Liebherr‘s expertise and innovation potential in the field of automation. Customers benefit from the opportunity to carry out tests using their own workpieces on the equipment at the center.
There is a concentrated atmosphere in the Tech Center. A test setup for developing gripper strategies for a customer is documented at the bin picking station. Next door, the test facility is running various core processes of battery pack assembly for e-mobility are being tested on the facility. Opposite, an innovative solution for plugging battery module connections is being tested.
Bin picking – customer trials
1. Scan:
Testing and selection of a suitable vision system with customer workpiece
2. Simulated removal:
Simulation of a workpiece-specific gripping pro?cess and checking how much the bin has been emptied
3. Real test removal:
Components are gripped in reality by a robot and a workpiece-specific gripper
4. Real test with loading:
Removal and gripping position-dependent deposit placement of the workpieces
Space for exchange and customer trials
The 700 m2 hall quite literally offers a great deal of space for development and innovation. There is even room for large-scale systems. Until recently, the PHS 3000 Allround had been tested here, a variant of Liebherr’s modular pallet handling system for weights of up to three tons. There is also scope for discussion and sharing ideas with customers and within the team. The test hall, customer area and meeting rooms are all under one roof allowing visitors to experience first hand the automation of tomorrow. Customers also have the opportunity to commission or carry out trials with their own workpieces.
We deal with all application areas and can therefore select the optimum system for our customers. Our portfolio includes everything from technology packages for integrators to complete robot cells as plug-and-play solutions.
Complete bin picking solutions
As one of the leading solution providers in the field of random bin picking, Liebherr tests the interaction of the individual components required for the automated removal of workpieces and feeding into the manufacturing line by robots at the Tech Center: software, vision systems, gripping technology and robotics. Where many other suppliers cover individual areas such as camera technology, Liebherr offers complete solutions. “We deal with all application areas and can therefore select the optimum system for our customers,” explains Thomas Mattern, Head of Development for Automation Systems. “Our portfolio includes everything from technology packages for integrators to complete robot cells as plug-and-play solutions.”
But it’s not just the company’s own tests that are running at the bin picking station. Trials and feasibility studies for customers are also carried out here – from part recognition to removal with complete box emptying to position-dependent positioning in the manufacturing line (see info box above). “Every workpiece has different challenges: crank shafts get caught, sheets stick to each other, anti-corrosion film casts shadows or covers parts,” Mattern explains. “We can test all these scenarios really effectively here."
E-mobility: core processes of battery pack assembly
In the field of e-mobility, Liebherr is working on the end-to-end automation of battery pack assembly. The focus here is on the process reliability of the joining, screwing and dosing assembly processes as well as on the material flow and material supply to the assembly equipment. Liebherr tests the automation of these processes in advance as a simulation on a “digital twin” and then demonstrates the process capability on a facility test equipment.
Here, tests are then run on the detection, positional dependency and modular assembly, module connectors and the cover of the battery housing in order to screw them in place with positional accuracy. Another focus is on the dispensing of one- and two-component adhesives and sealants as well as heat-conducting pastes, including process monitoring during dispensing bead detection using 3D vision systems. “This, in combination with robotics, is a highly demanding process in e-mobility,” explains development engineer Jan Pollmann. “We are working on process reliability to pave the way for customers to automate.” Customers can also use this system by request for tests on their own battery packs, therefore benefiting from thehigh-tech infrastructure in Kempten.
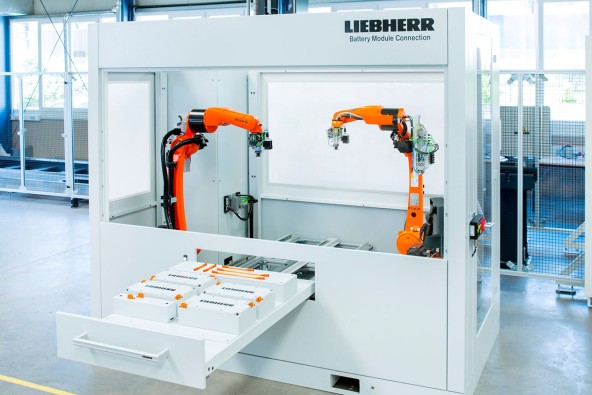
Position-accurate joining of high-voltage plug connections with two cooperating robots
Innovative: automation of flexible plug connections
A unique, innovative technology is being tested at the system over the road – the automated assembly of flexible high-voltage cables with plug connections for battery modules. Two synchronously operating robots with a patented combination gripper join the plug connections in a precise position with the aid of cameras. Interest in these connectors in the industry is growing because, unlike conventional rigid module connectors, they are easier to assemble, safer due to their electrical insulation and more robust in use. This results in additional application possibilities for the automation of plug-in cables in battery packs, which are developed and tested individually for each customer.
Win-win situation
The Tech Center represents Liebherr’s innovation potential in automation. Customers benefit from the extensive expertise of experts, who respond to individual requests and demonstrate and test products and processes inthe test facilities. “Liebherr has therefore created a win-win situation for both sides,” says Thomas Mattern, summarizing the benefits.