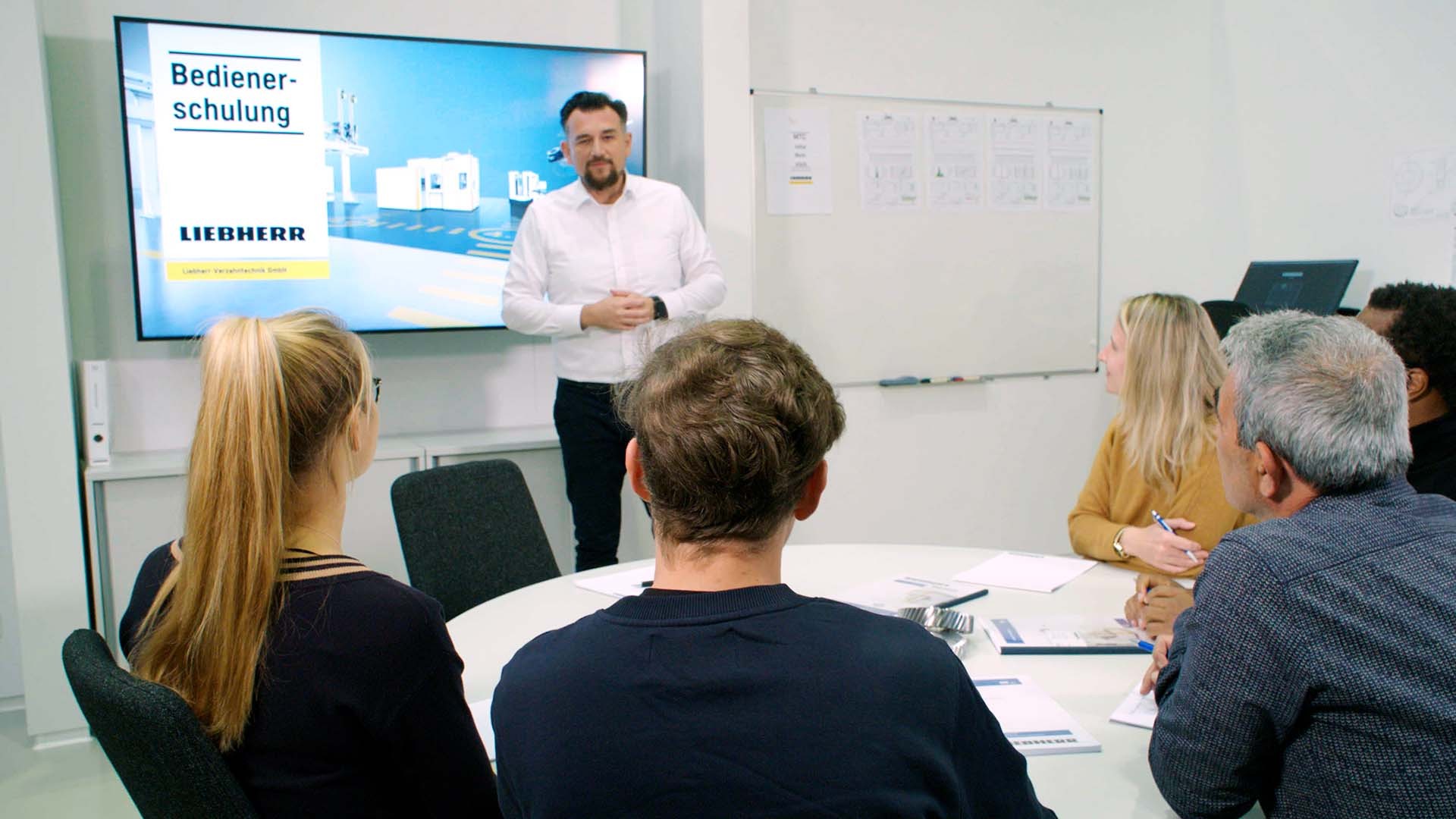
Exploiting the full potential of Liebherr machines
As in all industries, gear cutting specialists have to keep up with the latest technological developments. At the Machine Training Center (MTC) in Kempten, Liebherr experts teach the necessary know-how on site or online: professional and practical training courses on operation and maintenance help participants get the most out of their Liebherr machines.
The five men and women are concentrating on the large monitor in the training room. It is showing the machining area of the gear cutting machine where chips are flying as a first part is being manufactured. Beforehand, the participants carried out a joint machining area and operator-side collision analysis with Training in small groups Concentrated work at the simulator stations Cameras enable deep insights into the machining chamber regard to chamfering parallel to the cycle time. Afterwards, the group splits up. Half of them parameterize the tool and workpiece files for the machine setup on the simulator, while the others set up the machine in manual mode. The trainer is always on hand with help and advice.
The teams now watch each others’ actions and routines via the cameras inside the machine. Next, the gear produced is cleaned and measured on the adjacent measuring machine. The measuring protocol is projected onto the large screen. This allows everyone to discuss the necessary corrections together and adjust the parameters. The corrected measurement data is then transmitted to the gear cutting machine via the general data exchange (GDE) interface and displayed there.
Professional and practical
This pleasant learning environment is at the Machine Training Center (MTC) of Liebherr-Verzahntechnik GmbH in Kempten. The new, bright training rooms are equipped with the latest technology the world of gear making has to offer: an LC 280 gear cutting machine with ChamferCut device, an LGG 280 gear grinding machine and a WGT measuring machine. Here, the participants find out in detail what the machines can do, so that later they can fully and efficiently exploit that potential – and they do this by manufacturing real workpieces. After completing the training, they receive a certificate. If any questions arise when they return to their day-to-day work, they can ask the service team for advice.
State-of-the-art media technology
The media technology at the site is state-of-the-art. Up to eight cameras transmit images from different perspectives inside the machine to large monitors. Even the smallest components of the machine electronics can be easily seen by all participants using the visualizer. Various scenarios can be tested on simulators without the risk of damaging an expensive machine. “The simulators take away the fear of breaking something. Everyone is then much more relaxed when they actually come to use the machine,” says Markus Bahsler, Head of the Liebherr Academy. “The training teaches them to use the ideal parameters.”
The participants don‘t just look over the trainer’s shoulder, they practice on real workpieces themselves. As you can see, real chips are flying here!
Training courses for mechanics and electricians
Liebherr also offers individual, modular and topical training on the maintenance of the mechanical and electrical systems. The mechanical training courses focus on troubleshooting and geometric testing of the machine axes, and on carrying out the necessary adjustments so that the machine can produce with the highest quality. They also include analysis of the fluid diagram and cooling systems as well as replacement of specific drive components and wear parts. The electrical training courses focus on data backup, the PLC program structure and cycle diagnostics, adjustment of measuring systems as well as advanced troubleshooting and fault elimination. The company’s own personnel are trained this way to correctly analyze and repair the machine.
Live Online Training (LOT)
The practical handling of the machines is best learned on site. However, thanks to the Academy’s modern media technology, subjects such as programming can also be easily taught in online training courses (details can be found in “Liebherr Academy goes digital”). “Our camera technology for live online training conveys images and situations that you can otherwise only experience live – and in some cases it’s even better,” says Bahsler. In the online format, for example, flexible, user-defined dressing of grinding worms with single or multiple starts can be practiced using a form disc with point or line contact. Didactic elements maintain the attention of the participants and ensure that what they have learned remains firmly anchored. The live online training is ideal for anyone who is experienced and familiar with operating the machine. Participation is possible practically anywhere in the world, thus saving travel time and costs.
Getting the best out of the machines
Small groups of no more than six people and the latest media technology ensure that the training is as effective as possible. “At the MTC, the participants are not distracted by day-to-day business and can concentrate fully on the subject at hand,” explains Bahsler. “And they don’t just look over the trainer’s shoulder, they practice on real workpieces themselves. As you can see, real chips are flying here!”. Businesses benefit from increased process reliability and efficiency. If the operating personnel can get the best out of the Liebherr machines, productivity can be increased and there are fewer downtimes and disruptions.
Find out more here: Machine Training Center