Building with concrete modules made easy
The first PPVC structure built exclusively of concrete on the island has been built in Singapore. Lots of heavy prefabricated concrete parts had to be hoisted for this purpose. Building contractor Dragages Singapore used two Liebherr flagships for this purpose – two 1000 EC-H 40 Litronics.
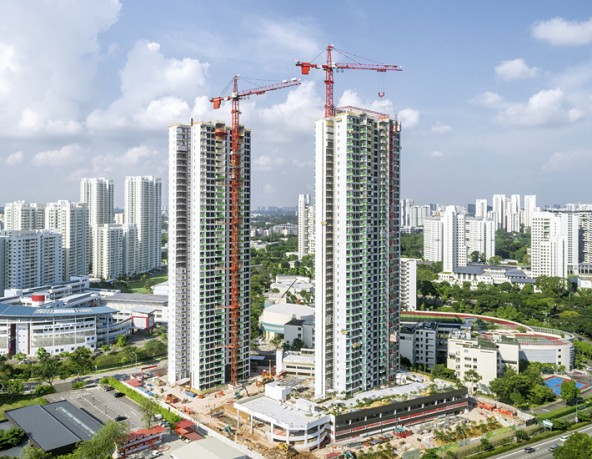
The main customer used the two high-top cranes to install the 40-floor “The Clement Canopy” – an apartment construction project using the first version of the PPVC system (prefabricated prefinished volumetric construction) to be made entirely of concrete. Even though this method of construction has already been used in other countries, this is the highest building project in the world to use this process.
The most powerful crane in Singapore delivered
Kevin Lai, Senior Methods Manager for “The Clement Canopy”, explains: “The Clement Canopy is our first project for which the modules are made entirely of concrete and are very heavy – the heaviest module weighs 29 tonnes.” With a maximum lifting capacity of 40 tonnes, the two Liebherr tower cranes are the most powerful ever to have been imported into Singapore. They are ideal for hoisting heavy prefabricated concrete components like these.
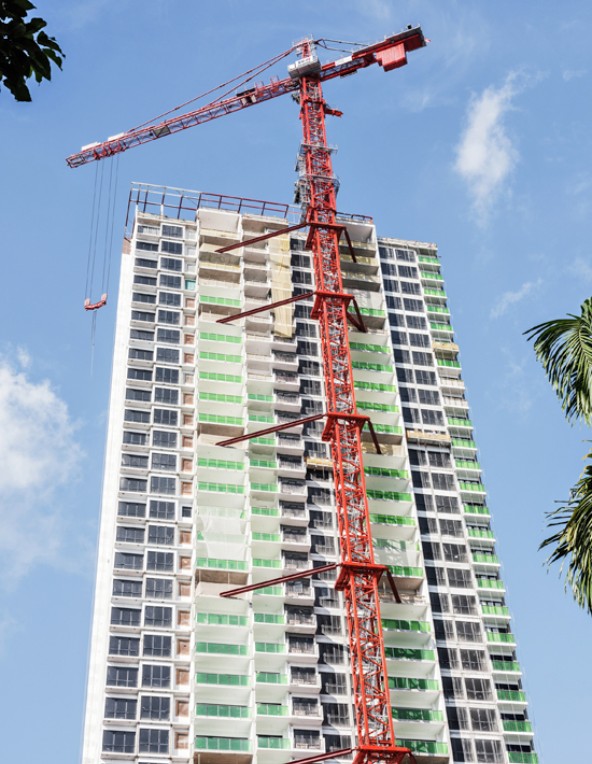
Building specifications imposed by the government and customer requirements satisfied
At the end of 2014, Singapore awarded PPVC construction orders for selected regions and monitored the application of this system very closely since its objective was to use this building method to improve productivity on sites. Dragages Singapore was awarded the order to work on “The Clement Canopy” project by United Venture Development. The project consists of two towers, comprising 505 apartments with a total floor area of 46,000 square metres. Under the regulations of the Singapore government, 65 percent of the construction above ground had to be built of reinforced concrete PPVC modules.
Kevin Lai explains that Dragages worked with ADDP Architects during the planning phase to improve the layout, divide the residential units into modules and ensure that one tower crane could be used to build each block. It was calculated that the heaviest module would weigh 29 tonnes whilst the lightest would be just 17 tonnes. Dragages then checked the crane market to find suitable products.
Decision made in favour of the Liebherr full package
As a result of previous jobs in Singapore and Hong Kong, the company is familiar with Liebherr cranes and reduced its selection to three crane manufacturers by means of an exclusion process. Ultimately, the main reasons for choosing Liebherr included lifting capacity, reliability, customer service in Singapore, technical support from the Tower Crane Solutions Department and an attractive quotation package.
Another advantage was the size of the tower crane elements: “The size of the tower sections of 2.4 x 2.4 metres made transport easier without increasing costs and also reduced the space requirement on the site. We will certainly consider using these cranes again in the future if we receive similar orders”, says Kevin Lai.
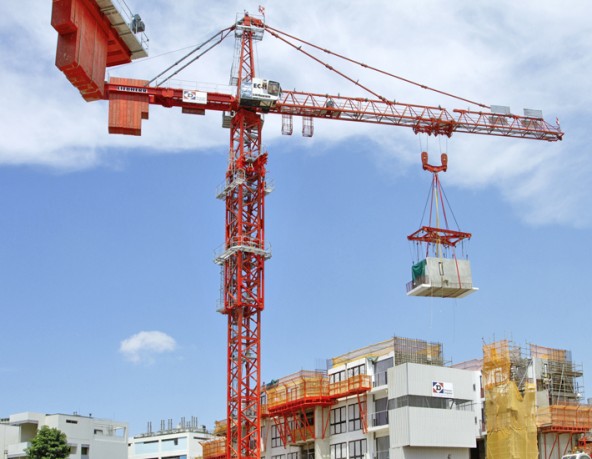
Customers supported during the construction process
Liebherr compiled all the documents which were required to ensure a smooth acceptance procedure of the two flagship cranes. The cranes then finally arrived in December and January and were erected within four days.
“The modules have to be positioned to an accuracy of two millimetres as any larger discrepancies could adversely affect the alignment of the entire building”, says Seng Swear Wern, Civil Production Manager for the project. To ensure that this is possible, the Liebherr tower cranes feature Micromove fine positioning mode. The crane operators are Dragages personnel and received the appropriate training from Liebherr-Singapore Pte Ltd.
With a jib length of 35 metres, both cranes were able to operate from a fixed position outside the two towers and grew as the structure rose as they were connected to a non-modular element of the building. In total 1866 modules had to be installed. The two Liebherr flagship cranes operated for more than a year and proved their fantastic capacity and reliability.