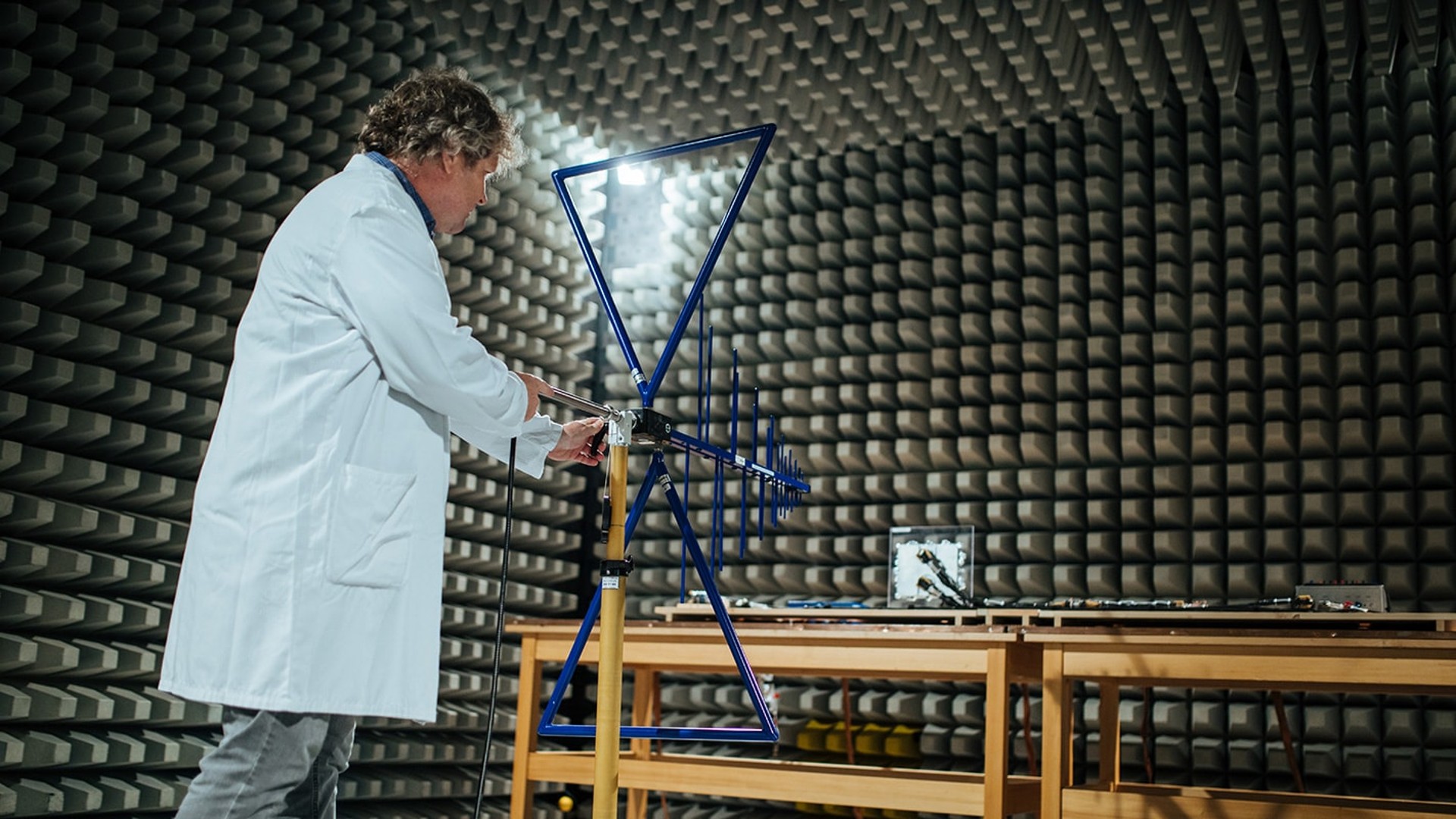
6 minutes reading time
Electronics on the test bench
Over the course of their lifespan, electrical parts are exposed to a wide range of external influences. The experts at the Liebherr Test Centre for Electronics in Lindau, Germany use state-of-the-art testing and monitoring equipment to guarantee optimal performance and safety. We interviewed Christian Nuber, the head of the testing lab, to find out more about how electronic parts, some of which are safety-related, are put to the test.
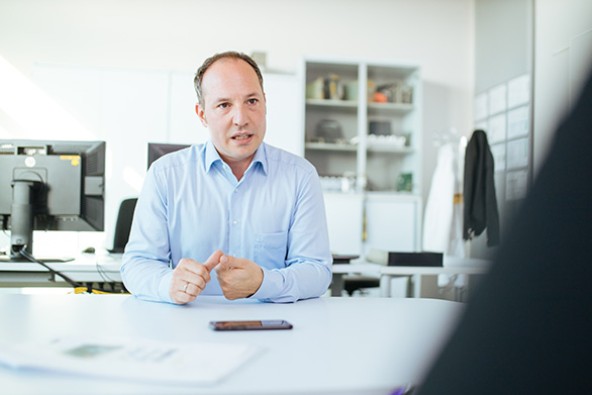
Mr Nuber, what are the advantages of Liebherr having its own testing lab for electronics?
Liebherr Electronics is the centre of excellence for all electronic parts produced within the Liebherr Group. At our site, we develop and produce electronic control units and power electronics that are used in all kinds of Liebherr products and technologies. These electronic parts must undergo rigorous testing both during the development stage and before they are approved for batch production. Depending on where they will be used, the parts are exposed to various external influences which they must be able to withstand without loss of functionality. Our various testing processes enable us to verify the quality and reliability of our products. In addition to testing resistance to the usual external influences, we can also conduct individual tests in accordance with international standards, right here at the Test Centre. Since 2012, we have also offered our testing services to external clients.
Which electronic parts do you test here at the Test Centre?
Liebherr’s products span across many different industries, from construction machinery, mining and gear technologies, to solutions used in the aeronautics and transport industries. So, we test all kinds of parts here, from operating and display units, to control units and power electronics, which are intrinsically related to product safety. If a control unit fails, for example, as part of a climate control system on board an aircraft, it can have devastating effects. If the control unit fails to properly regulate cabin pressure, it can impact the health of everyone on board, even if these parts are only one small part of the entire structure of the aircraft.
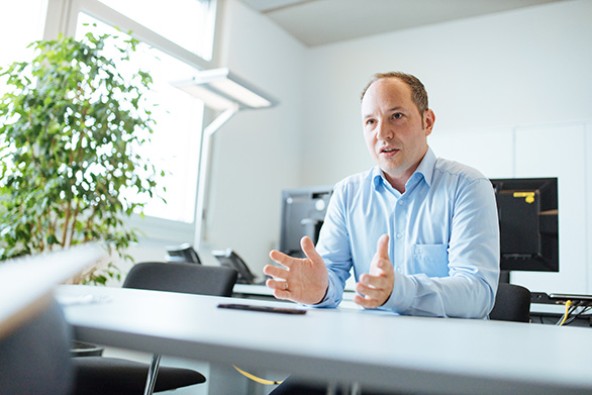
What does the usual testing sequence for an electronic part look like?
It’s difficult to generalise. There’s a lot of variation. The parts all have to meet specific requirements, depending on where they are going to be used. These are defined by many different national and international standards and norms. We use multiple test procedures to prove that the parts meet these requirements.
The parts being tested have to be able to withstand specific external influences, such as temperatures, vibrations or electromagnetic waves, all of which are defined by the various standards. So, for example, power electronics that are going to be installed into an offshore crane have to be tested inside a salt-spray chamber, which simulates the salty atmosphere at sea.
Electromagnetic compatibility
Parts are tested for electromagnetic compatibility inside an EMC chamber. An antenna is used to create electromagnetic fields, to test how the electronic parts react to them. We can also test which electromagnetic waves are produced by the part being tested. The chamber is electromagnetically sealed off from the outside world to simulate an open space without interfering, reflecting radiation.
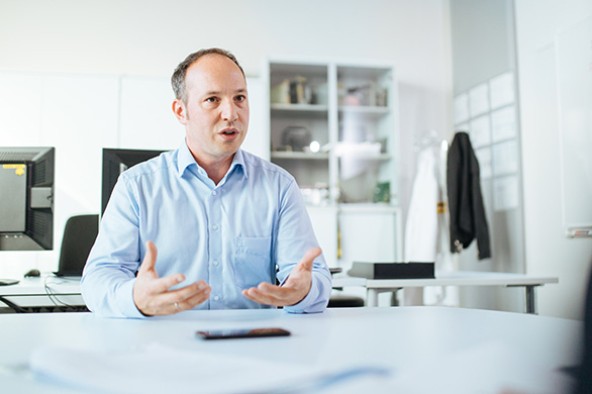
How do you test parts for external customers?
There's also a lot of variation here. Some of our customers, for example, in the automotive industry, are very familiar with the relevant standards themselves, and only come to us to have specific tests carried out. But there are other customers that need our support throughout the entire approvals process: from selecting the correct standards and norms for their product, to testing it during the development stage, to performing the final tests before batch production. Depending on which industry the client works in, it can be quite difficult to even select the right testing profile.
We are not a conventional testing lab. Here, at a single location, we pool our expertise and experience to assist in the development of electronics solutions. We have our own commissioning lab, where assemblies can also be electrically as well as mechanically reworked. We can rely on both of these, for example, when our customers want to undertake minor modifications on their equipment after a test procedure is complete. Sometimes, it can be helpful to discuss a problem with another developer, so we can find an easy solution. That is something we enable our clients to do.
Are the current megatrends of digitisation and electromobility having an impact on your work at the Test Centre?
Yes, of course we are seeing the impacts of these developments. In terms of digitisation, the topic of increased connectivity within the internet of things (IoT) is especially relevant for us. Liebherr Electronics also makes telematics products, which of course have to be approved according to the latest standards.
Electromobility is also an important topic for us. Many of our clients from the Lake Constance district in Germany work in the automotive industry. They’re primarily concerned with creating control electronics for batteries with even more power, and these still have to be developed and then submitted to the appropriate tests. We are currently unable to test such large electronic parts at our site. We are now exploring the possibility of expanding our Test Centre to keep pace with these developments.