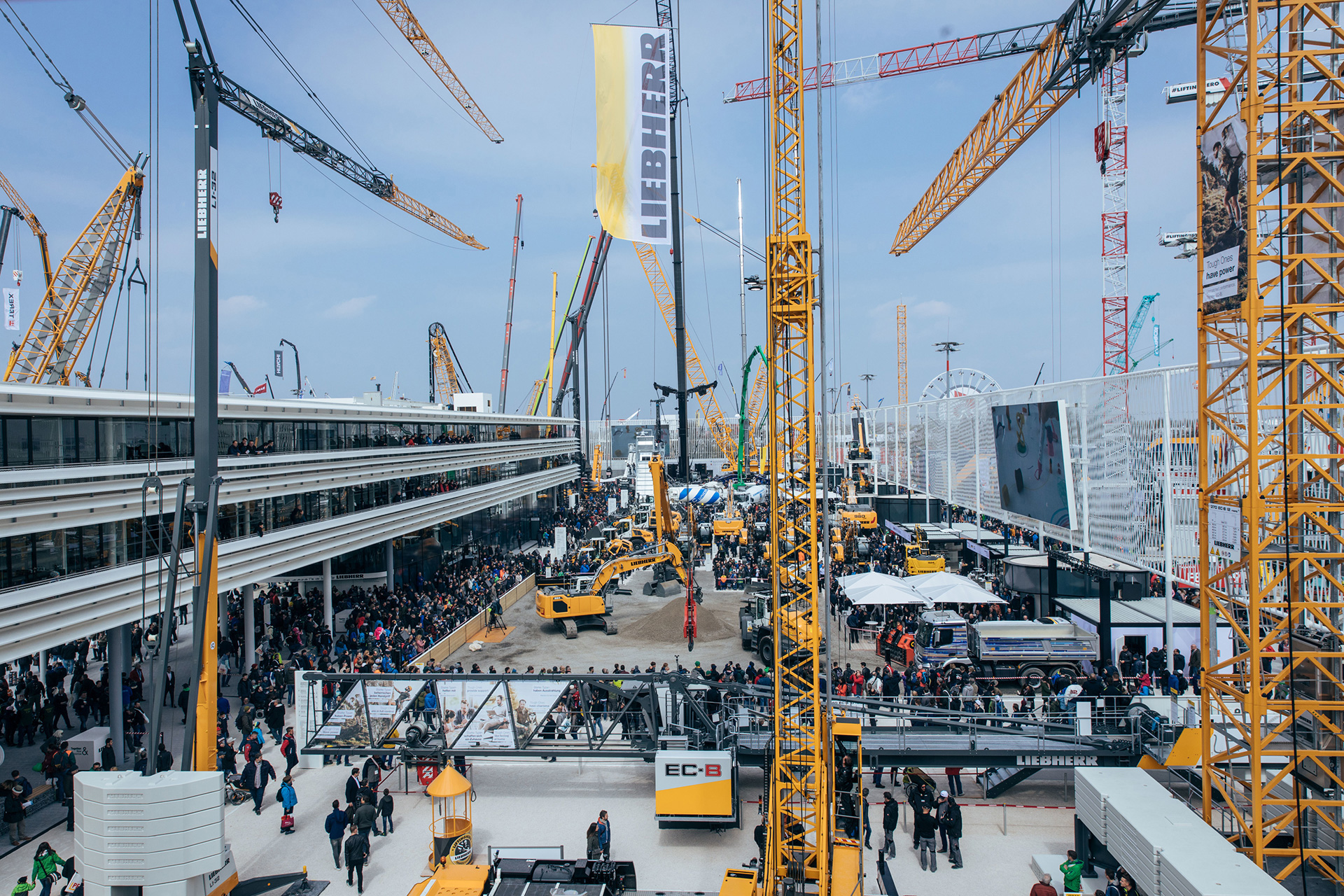
Click RELEASE VIDEO and follow the data protection notices.
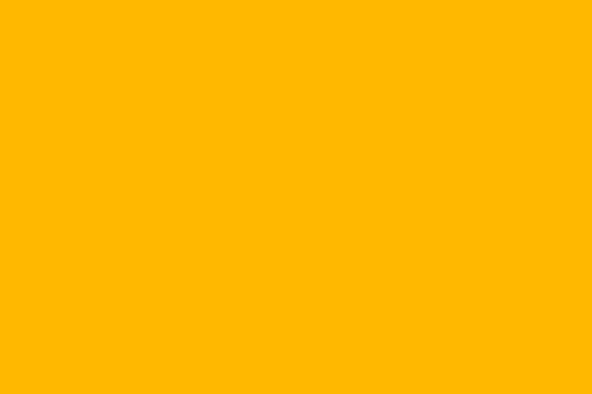
Dimensions
Bauma is the largest construction machinery trade fair in the world and Liebherr is one of the largest exhibitors. Every three years Liebherr presents innovations, solutions, giants and future trends on an area of 14,500 m². An international audience from all over the world dives into the fascinating world of construction and mining machinery for seven days.
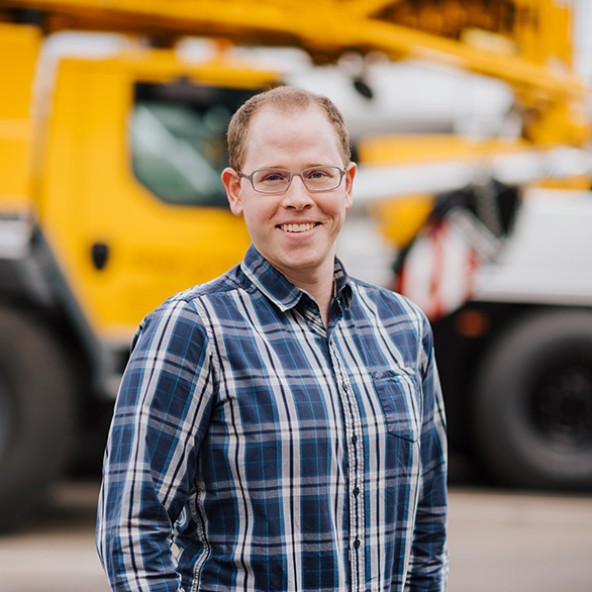
From Bauma to a dream job
Ricardo Dieing just wanted to have a look around at the Bauma trade fair. But the 29-year-old soon found he had landed his dream job with Liebherr, in Ehingen.
“A walk through the Bauma site is a must for me,” says Ricardo Dieing. The 29-year-old construction engineer has visited the world’s largest construction machinery trade fair three times, and each time his path led him to the Liebherr stand. “The large machinery, and especially the cranes, have always captivated me,” he says.
Quite by chance, this time he also spent some time at the careers stand and happened to strike up a conversation with HR manager Stefan Füller. “After I finished my studies, I landed a good job with a major scaffolding construction company, so I wasn’t looking for anything in particular. Two weeks later, Stefan sent me a job description that suited me perfectly,” he recalls.
Dieing started his new job in Ehingen in October. “Likeable colleagues, appealing tasks and a fantastic working environment: I couldn’t have got off to a better start,” he declares.
Steelwork and finite element calculations were particular interests during his studies. “Calculating the structural analysis of a crane grid at the very limits of the material is exciting stuff,” says Dieing.
Was it mere chance or destiny? “I don’t mind either way,” says the young construction engineer. “It’s a great leap forward for me. I’ll never get bored working in crane construction.”
Bauma is part of Liebherr and Liebherr is part of Bauma
Liebherr has been represented at the leading fair for more than 60 years. A lot has changed over the years.
That was Bauma 2019
Passed with flying colours: the emission-free construction site of the future
The construction site of the future has been successfully tested in Vorarlberg. The electric machines presented by Liebherr at Bauma have paved the way for “local zero emission”. We discuss the results achieved so far with Martin Hofer from the i+R Group, which worked with Liebherr and their start-up Suncar HK to convert the drilling rig LB 16 unplugged – to run on electricity. A world premiere with excellent prospects.
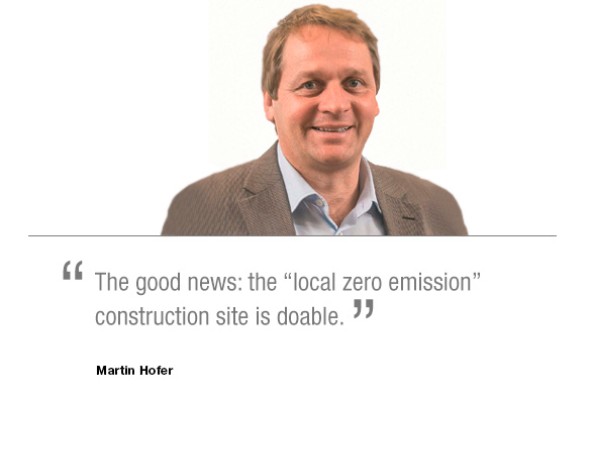
Mr Hofer, there’s a lot of deep and dirty work on construction sites, especially in foundation engineering. Where do sustainability and energy efficiency come in?
Sustainability, energy efficiency and resource conservation are just as important on the construction site as they are in the rest of our working lives and environment. After all, this planet is the only one we’ve got. The good news: the "local zero emission" construction site is doable. This is a step in the right direction, especially in densely populated areas where noise and exhaust emissions are a particular concern.
What experience can you draw on for this?
We have already converted over 45 compact excavators to run on electricity without cables. The starting point was the world’s first cordless, battery-powered electric excavator, which we built in cooperation with mechanical and electrical engineering students at ETH Zurich.
You recently collaborated with Liebherr to bring the first local zero emission construction site in foundation engineering to a successful conclusion at the junction of the A14 Bludenz-Bürs in Vorarlberg, Austria. What challenges did you encounter there?
Bludenz-Bürs was the perfect pilot site for us. It is a very busy junction, with frequent traffic jams and other obstructions. We also had to contend with the very constricted spatial conditions on the construction site, where the excavators, drilling rig and mixing vehicles had to operate in very tight spaces. Liebherr’s LB 16 unplugged, the world’s first battery-powered large rotary drilling rig, was used for the foundation work. We converted the machine within eleven months with the aim of ensuring that there would be no loss of performance or use factors compared to the conventional version. We also used a number of other electric excavators and a Liebherr ETM 905 concrete mixer with an electrically powered drum to supply a large part of the concrete. The results: virtually no local exhaust fumes and significantly less noise.
Can you imagine implementing this kind of fully electric construction site everywhere?
Definitely. In principle, we can equip every machine with an electric drive. We would install the electric motor and a correspondingly powerful battery or supercaps in the place where the diesel engine and tank are usually located. Of course, the simplest option is for the manufacturer to deliver a suitably configured basic model from the outset, where there is no need to remove the fossil fuel combustion engine drive train beforehand. This was the case with the LB 16 unplugged.
What are the particular challenges associated with electrification?
Electric motor technology is very highly advanced. Major advances have also been made in recent years in the field of lithium ion batteries. Our particular development focus is on battery management. Temperature control plays a crucial role in battery performance. It’s the same as with your mobile phone. If you leave it lying in the blazing sun in your car, the battery will eventually die. Or in the winter, if you let your mobile phone get too cold while you’re skiing, it tends to give up the ghost just when you’re about to take the perfect photo.
Electrically powered machines will have the edge over conventional combustion engines over the long run, especially when you factor in energy and maintenance costs. There is a large potential for savings here.
At what point does this type of electric drive start paying for itself?
The initial costs of purchasing electrically powered, battery operated construction machinery are much higher. However, the machinery has a service output of over 15,000 hours, so from a life-cycle perspective the costs can be recouped after a certain point. Electrically powered machines will have the edge over conventional combustion engines over the long run, especially when you factor in energy and maintenance costs. There is a large potential for savings here.
You can’t measure the CO2 performance of a construction machine solely on the basis of the emissions it produces. What does the overall CO2 footprint look like?
Much like the electric car, when it comes to construction machinery we have to look at the big picture and factor in production and supply chains as well as energy consumption when calculating CO2 emissions. The turnaround doesn’t set in until after the electric construction machine has reached around 60 percent of its service life, which is when it becomes CO2-neutral. This is only the case, however, if it runs on electricity generated from clean, renewable sources. If the energy for the electronic drive is supplied by coal-fired power stations, this does us no good whatsoever on the climate front.
If the local zero emission construction site is already a technical possibility, how long will it take to implement it on a large scale?
This won’t happen overnight. At present, what we mainly lack is sufficient available capacities in clean, renewable energy sources. Similarly, the grids have not yet been designed to cope with the increased strain associated with a consistent shift towards e-mobility. If everyone tried to charge their e-mobiles and construction machines at the same time one evening, the lights would probably go out all over the country. So there’s still a lot to be done.
What in particular?
The technology is in place. However, there will probably not be any decisive changes until the government decides to set a new course by passing appropriate laws and regulations. Take the Netherlands or Norway, for example, where the use of fossil fuels is now being successively barred from rivers and urban construction sites. Incidentally, the coronavirus crisis shows how quickly changes might also be made towards improving sustainability if all the politicians are in agreement.
Our project with Liebherr has shown that we already have the technology and expertise needed to implement a local zero emission construction site with very good results.
What are the next steps for the construction site of the future?
Our project with Liebherr has shown that we already have the technology and expertise needed to implement a local zero emission construction site with very good results. If you annualize the energy and emission balance of the pilot construction site in Bludenz-Bürs, using only electric machinery would bring about savings of about 35,000 litres of diesel fuel and more than 92 tonnes of CO2 emissions on a construction site of this size. In other words, it would definitely be profitable to continue to develop the technological potential of electric drives, batteries and fuel cells. With strong partners like Liebherr, we are well on the way to achieving this. The next few years should be very interesting.
Liebherr is looking forward to Bauma 2022!
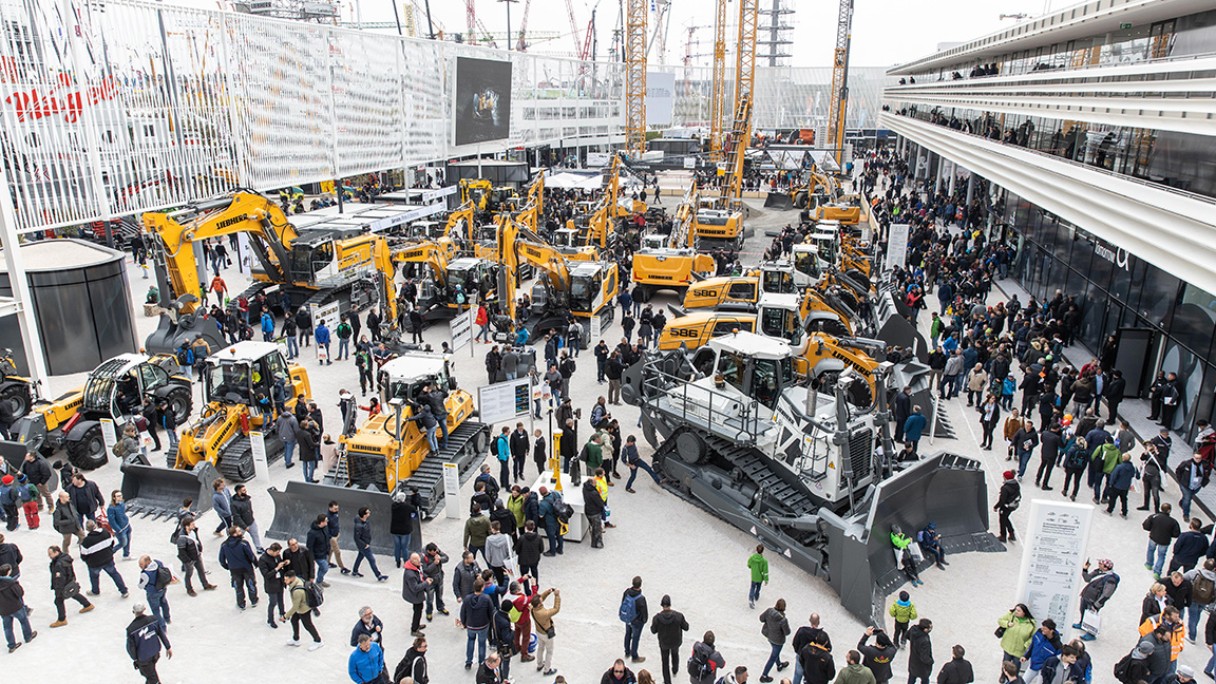
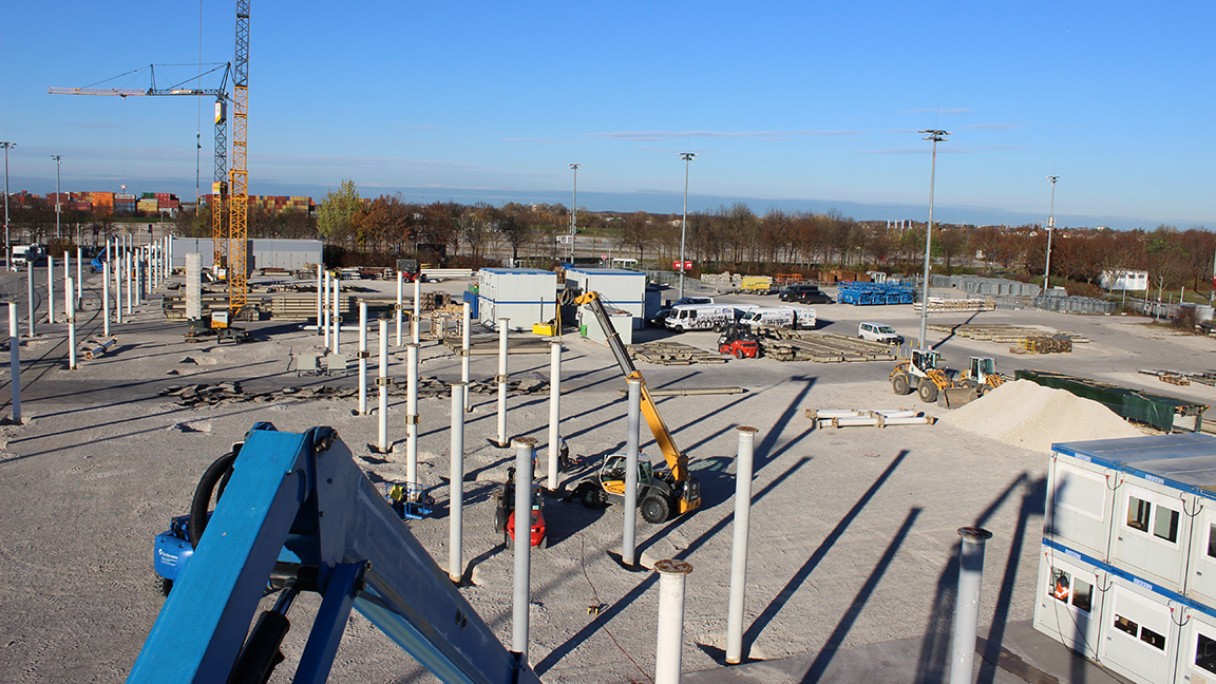